The Team:
William Forney, Konnor Kuppernus, and Xavier Haupt
General Description:
Recyclebot is a project designed to take filament pellets or old 3D printed parts and turn them into usable filament. We started off this semester focusing on ways to make Recyclebot more consistent by improving the hardware, introducing new processes, and refining the code. However, about halfway through the semester we ran into issues with the design that prevented us from making any more forward progress in this iteration of Recyclebot.
Functional Requirements:
- The entire device will have design files originated entirely from free and open source software.
- New designs this semester were created in Inventor, but were exported in an open source format.
- A new cooling system will be designed and implemented to improve consistency.
- A new cooling system was designed to increase the speed of cooling to help run through the downstream components of the system. The idea was to use running water to cool the extruded filament. This would have been done by flowing water over the filament. This water would be flowed over a 3d printed part designed to guide the filament through the water, collect the used water, and to blow the remaining water of the filament prior to the measurement unit.
- The auger motor will be replaced to increase extrusion rate.
- We replaced the auger motor with a 51k120rgu-af, a much more powerful AC gearmotor. The only downside with this motor is that speed is controlled by a potentiometer on the attached motor controller, but we purchased and have begun to implement a digital potentiometer to allow for automatic speed control.
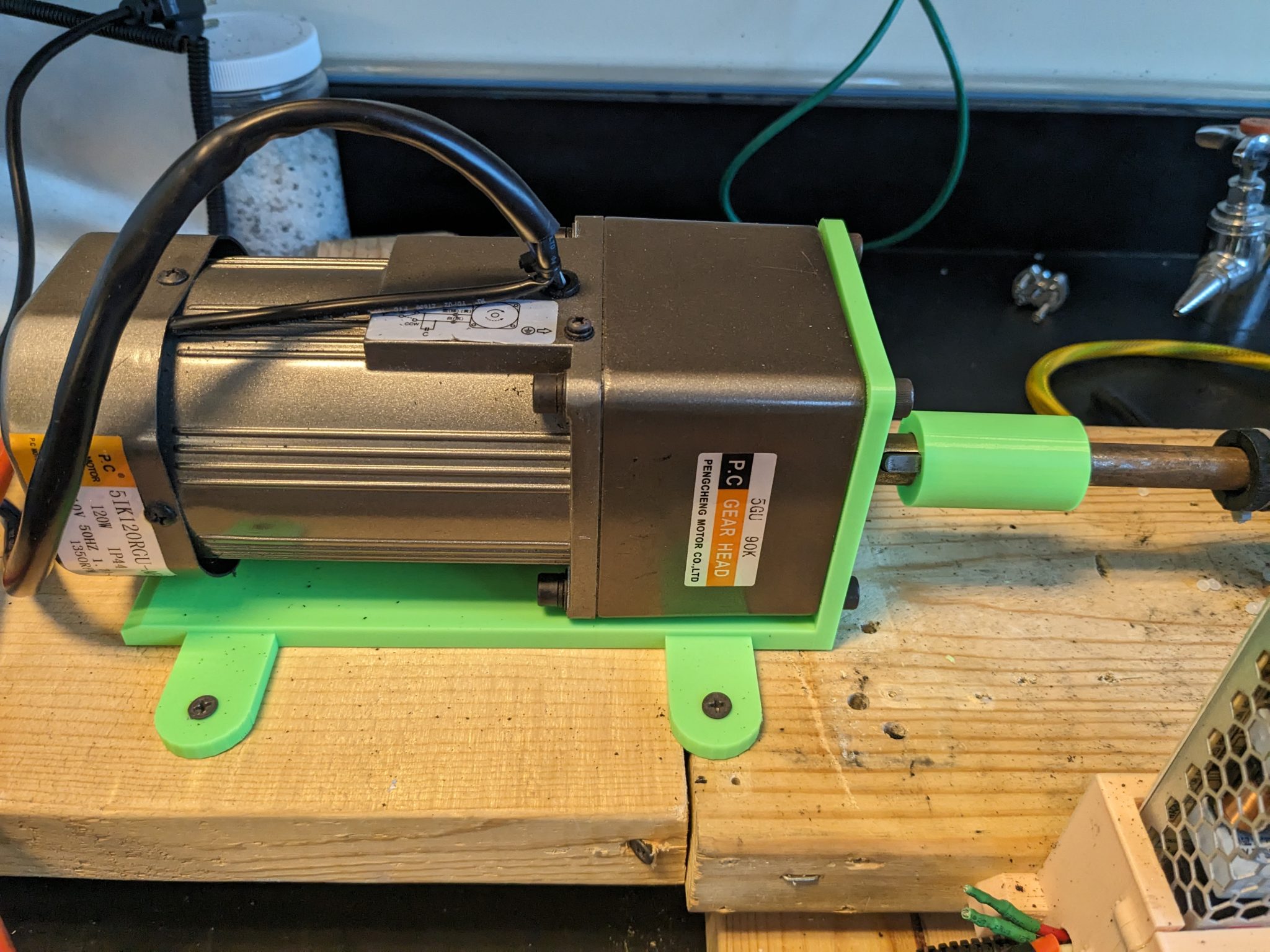
- A cleaning process will be developed.
- A cleaning process was developed to help improve the consistency of the extruded filament. This process includes using Chem Trend’s Ultra Purge 3615 and a changeover document. Ultra Purge 3615 is polymer based material designed to be extruded. While it is in the extrusion barrel it pulls impurities like carbon and pigments from the screw and barrel, which help clean and reduce changeover time between colors.
- The control loop in the code will be updated, along with the user interface.
- The control loop was updated to reflect the changes made to the auger motor. Code to control the auger motor using DS3502 digital potentiometer was implemented along with work starting on a user interface to view temperature, diameter and control motor speeds.
- Redesigning the hopper to reduce moisture uptake.
- The new design for the hopper is entirely 3D printed, and includes a lid that can be bolted down. We are also looking at a way to include a container for silica gel to keep the filament pellets as dry as possible
- Adding a dehydration process.
- We did not get to testing a dehydration process, but the idea that we came up with involved warming the filament pellets to 65oC for ~6 hours. We are also looking into ways to build this process into the new hopper design
Testing and Evaluation
While testing the new auger motor and cleaning process a new failure point was found. Due to the torque produced from the new auger motor along with the thicker consistency of the Ultra Purge 3615 pellets, plastic pellets were forced through a vulnerability in the 3d printed plastic coupling and hopper. Due to the presence of red filament pellets it is clear that this problem has been happening since the original design in 2018. While disassembling the hopper it was also found that the extrusion barrel was softening and burning the plastic coupling.
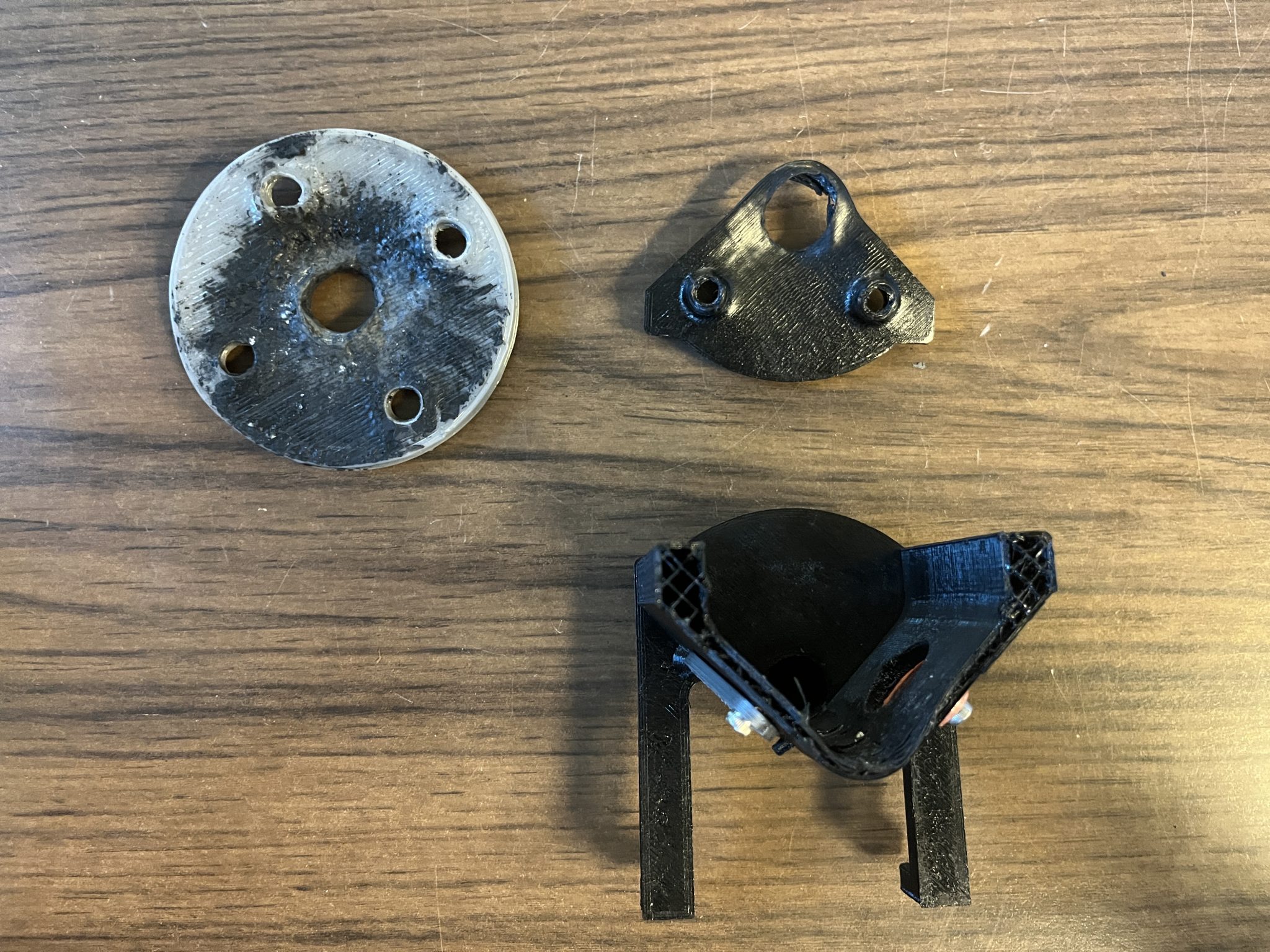
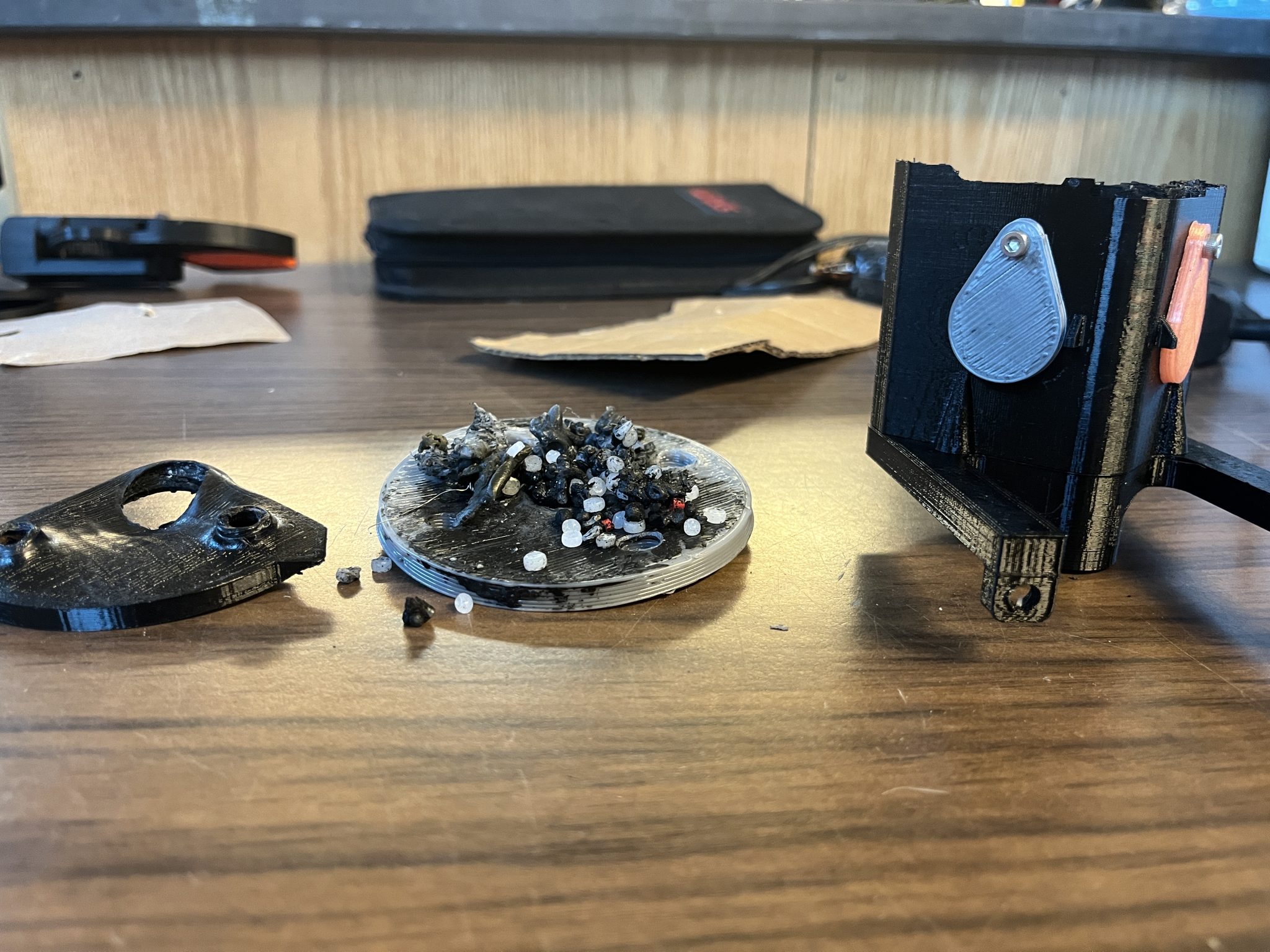
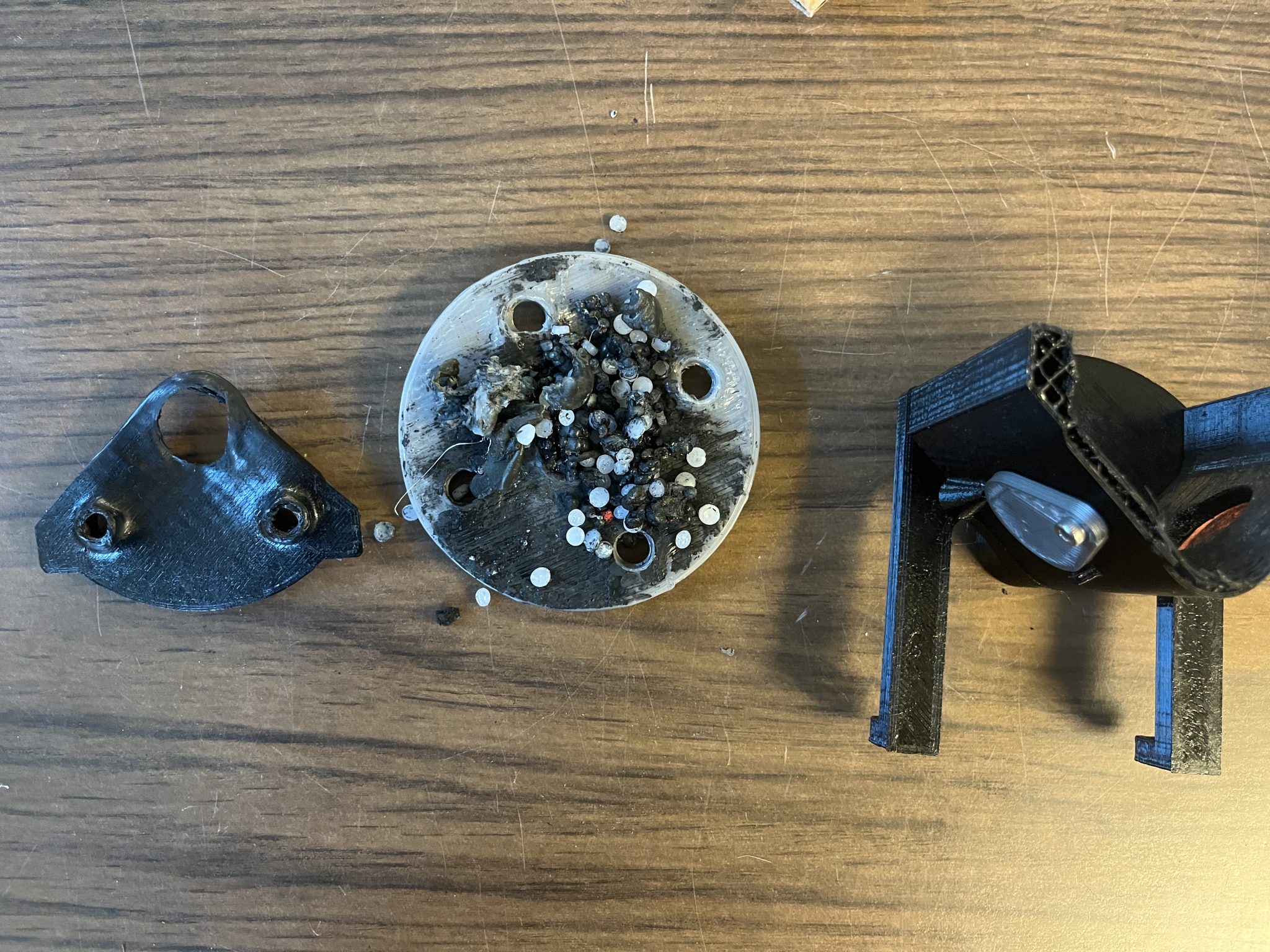
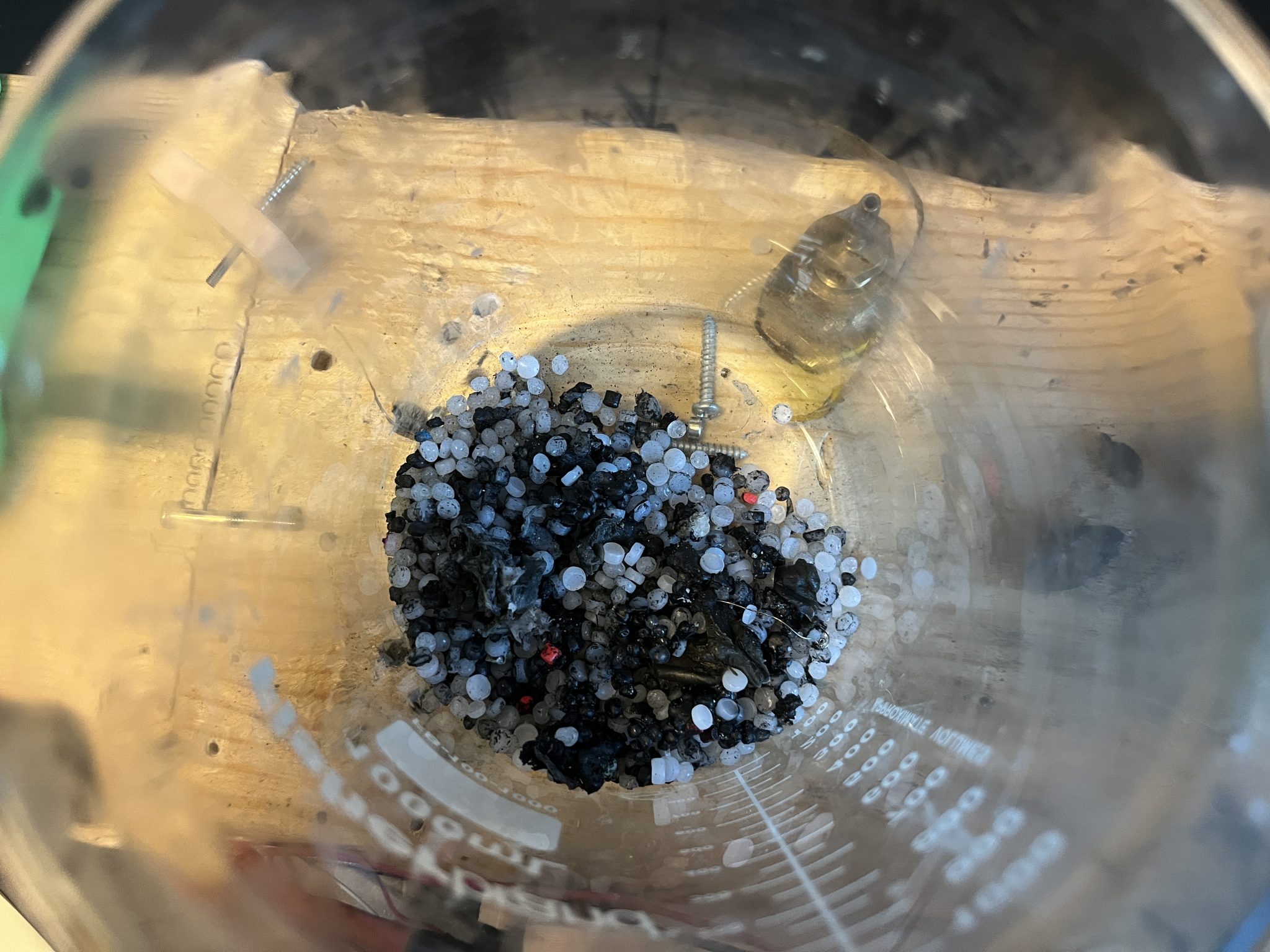
Moving Forward
After these failures we have determined that the best course of action will be to redesign most of Recyclebot. The key points we want to focus on are:
- Using an extrusion screw designed to extrude molten plastic
- The flighting in the extrusion screw will allow for a more uniform melt
- With less unmelted plastic within the extrusion barrel we won’t run into any problems with unmelted plastic causing too much torque required to start extrusion
- Chain-drive the extrusion motor
- The new motor provides a lot more torque than previous motors and was damaging other components of Recyclebot when there was a lot of resistance in the extrusion barrel. Chain driving the motor allows us to install points that are designed to break in ways that are safe to the user and recyclebot.
- Allows for a more compact design
- Also allows for changes in gearing of the system, this allows use to change the RPMs and torque for a more adaptable system
- Switching to an 80-20 aluminum extrusion base for the frame of RecycleBot
- Increase the strength of the frame and reduce breaking of shifting of part
- Allow more adjustment and adaptive mounting to increase the potentially use of Recyclebot
- Allows quick changes to parts on the frame
- Modular design
- The main benefit of a modular design is being able to work on each subsystem (extruder, cooling, diameter sensing, spooling, etc) separately
- A modular design will allow Recyclebot to be easier to move around, and subsystems to be switch as different needs related to material arise
- Reducing the amount of plastic components in direct contact with heated metal components
- High torque and high heat is involved in extrusion so reducing the amount of plastics part will help remove run based part failure
The overall goal for next semester will be working on the extruder module and fine tuning it until we get consistent extrusion.