(9/13/2024) This week, I will be collaborating with my team to identify the necessary components for a dryer unit designed for the filament flip-flop system. This unit must function even when the printer is off to maintain the filament’s quality and prevent any printing issues. Additionally, I will be researching the best methods to protect the filament from environmental factors to ensure optimal performance.
Goal: Design and plan the general dryer unit for the filament flip-flop system.
- Research: Investigate dryer units, environmental factors, and best practices for filament storage.
- Component Selection: List necessary components, research suppliers, and compare options.
- Design: Create a detailed design that works even when the printer is off and plan integration.
- Team Collaboration: Meet with the team, assign tasks, and set deadlines.
- Documentation: Document findings, prepare a report, and update the project timeline.
Concerns for the Next Week:
- Component Availability: Ensuring components are available and can be soured in time.
- Design Challenges: Designing a unit that operates independently off the printer.
- Team Coordination: Effective communication with the team with updates and jobs.
- Time Management: Balancing this project with other assignments and meeting with the team when we don’t have much time to do so already.
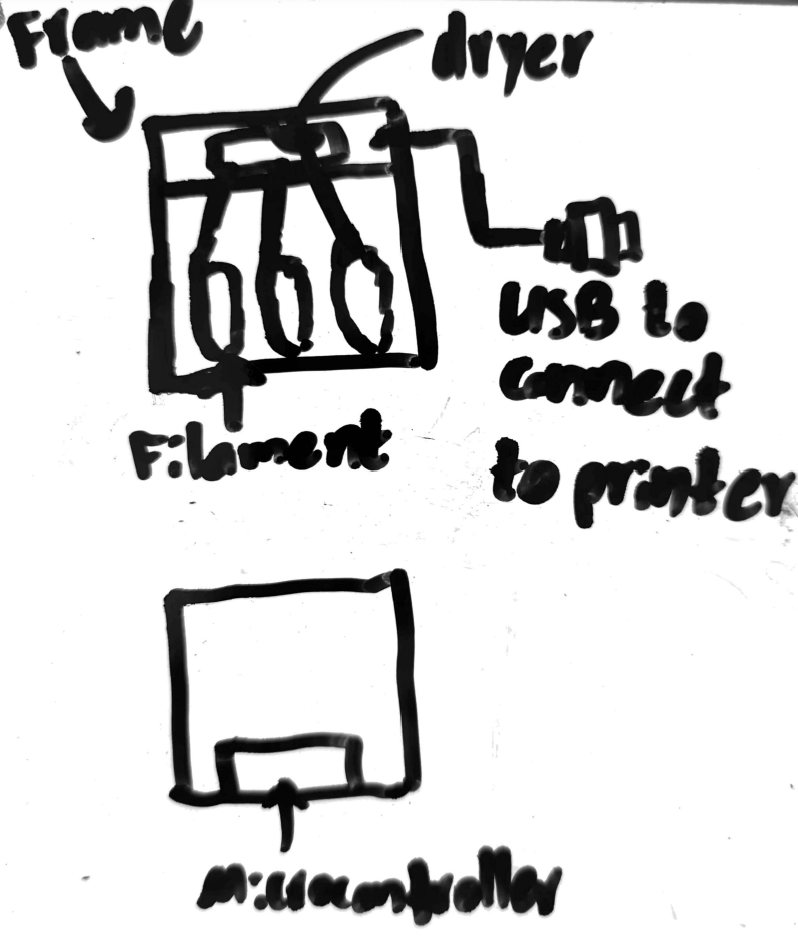
(9/22/2024) This past week, our team successfully completed our presentation slides, detailing our project and execution plans. We collaborated effectively, brainstorming ideas for the materials list and identifying what we need to order to begin construction. We also finalized concepts for the finished design and purchased some materials for the base structure. Items to add to the to-do list include initiating the build and acquiring the correct parts. On the other hand, assigning jobs can be removed from the list as it is no longer necessary.
Goal: Develop and outline the overall dryer unit for the filament flip-flop system.
- Analysis: Explore dryer units, environmental factors, and optimal practices for filament storage.
- Evaluation: Identify required components, research suppliers, and compare available options.
- Integration Planning: Develop a detailed design that functions even when the printer is off and plan for seamless integration.
- Scheduling: Convene with the team to set deadlines and ensure smooth coordination.
- Reporting: Record findings, compile a comprehensive report, and update the project timeline accordingly.
Concerns for the Next Week:
- Sourcing: Ensuring all components are available and can be soured in a timely manner.
- Independence: Creating a unit that operates independently of the printer.
- Communication: Maintaining effective communication with the team and providing updates.
- Scheduling: Balancing this project with other assignments and coordinating team meetings despite limited time.
- Project Initiation: Ensuring the project starts on time.
(9/29/2024) This week was pretty busy with the career fair, so we didn’t get as much done as we hoped. We decided to switch from Fusion 360 to Onshape for CAD because the free Fusion 360 licenses don’t support an editable shared folder for the team. We started a shared drive for CAD files and ordered some more parts, but we’re still waiting for them to arrive—hopefully today or tomorrow—so we can finish a rough CAD of the dryer before our CDR. Some of the team has been working on an adjustable holder for the rolls, inspired by DIN rails, and plan to make a mostly 3D printable rail with mountable bearings for the roll’s walls. Once the parts come in, we can measure them and create the unit to scale with precise features on Onshape. I’ll be focusing on the dryer unit in Onshape, and as a team, we’ll be preparing slides for the CDR and figuring out the best way to handle the switching unit in our next meeting.
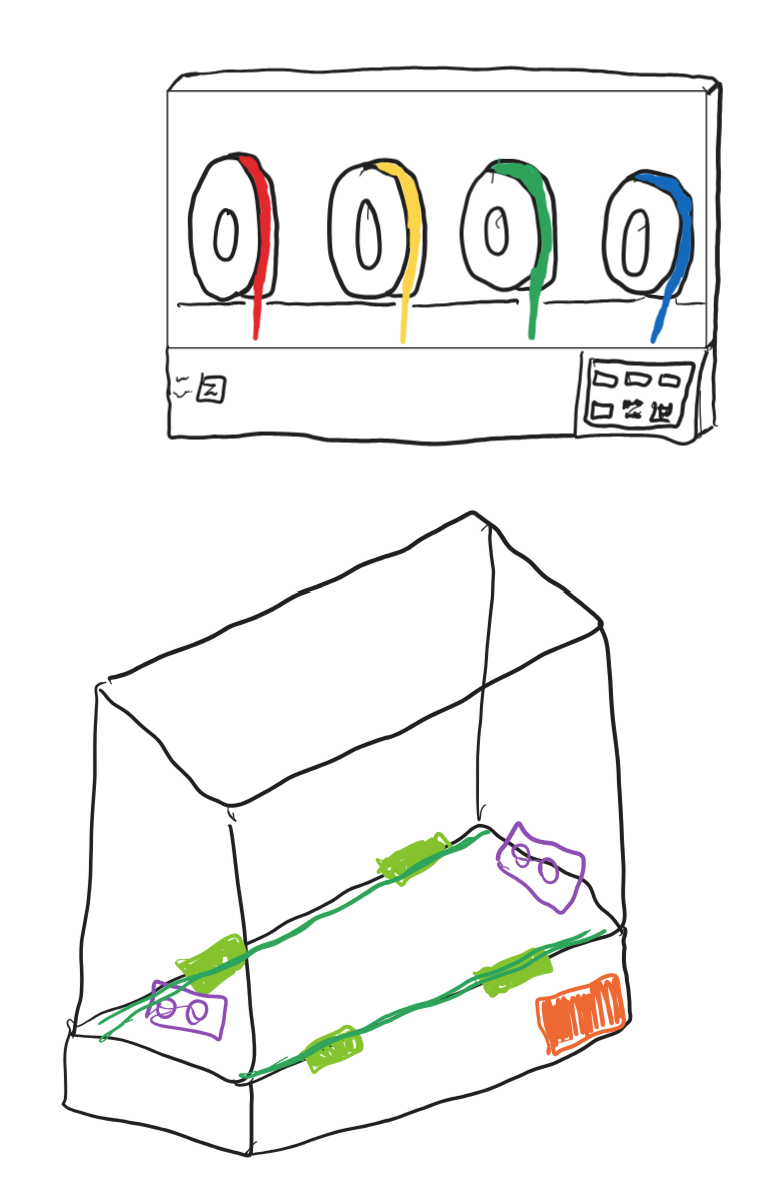
Spring 2025 Filament Flip Flop
(1/23/2025) So far, our semester goals for this project have been achieved successfully. Key lessons from the fall semester include the need to enhance our control system, heating power, and filament stands. This semester, our aim is to achieve printing capabilities with the printers, which involves several steps to reach an acceptable state. Our plans include expanding support to accommodate 4 rolls, improving the rollers for individual control, enhancing the heating system, refining our wiring diagram and power system, and improving the overall rigidity and interface of the entire system. We also are trying to organize our electrical set-up and making our raspberry pi a touch screen for easier access. Our screen will also show warnings or feedback needed to taken into account along with important information like heat temperatures.
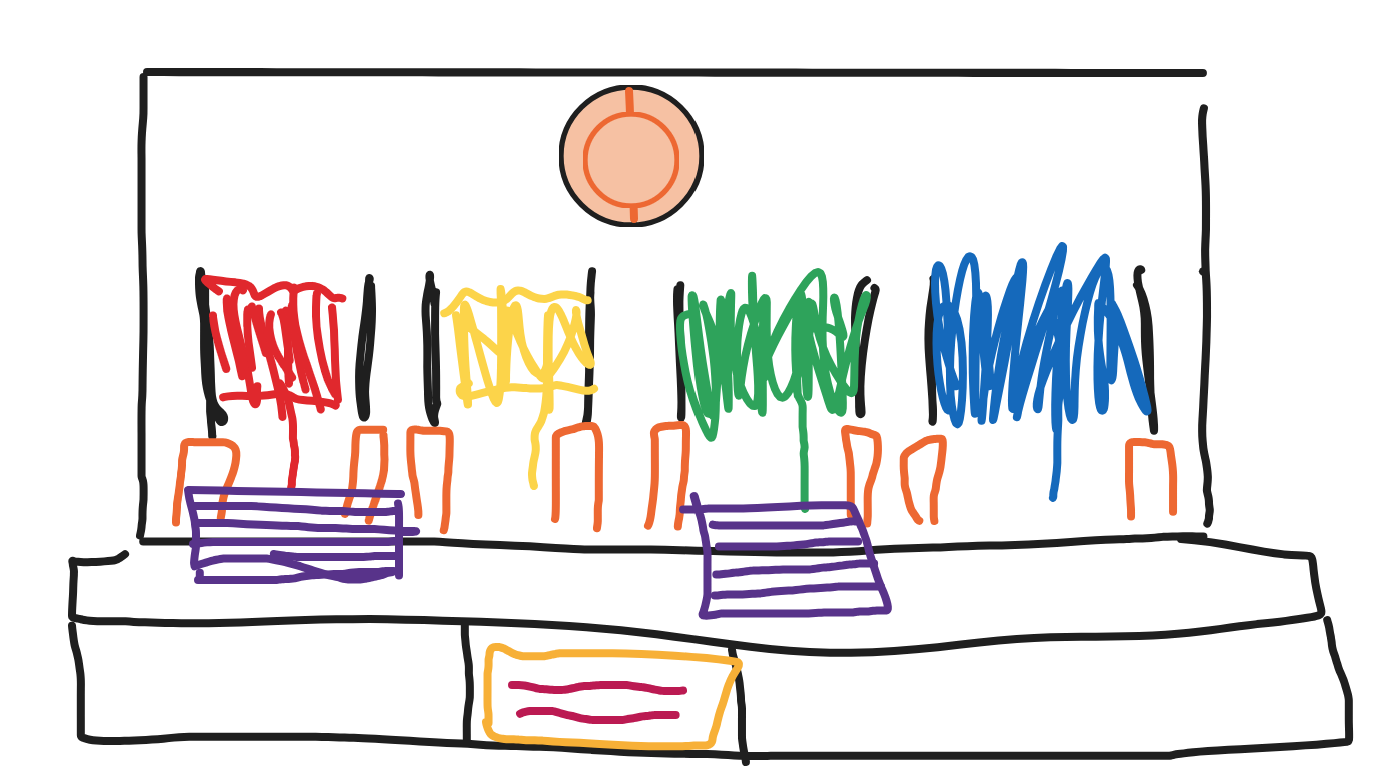
Small update (1/26/2025) This week, we showed the project’s current status and outlined our plans for the semester. We’ve ordered parts for the extension to support four rolls, as well as for heater improvements, electrical consolidation, and an Octoprint interaction screen. We are currently waiting on parts and talking about what to start and do next.
(2/4/2025) This week, a few team members are working on connecting the switch for the printer and installing some electrical wiring. Some of our other members are working on the Firmata system. For the Firmata system, we are using the FirmataExpress library, which adds support for DHT sensors and stepper motors. This provides the necessary commands to control the existing FFF prototype, aside from the small display. The display can be reconnected directly to the Raspberry Pi.
(2/16/2025) During our recent CDR, our team provided an overview of our current designs and plans to complete the project. We’ve taken the basic design from last semester and expanded upon it to enhance installation, offer individual roll rewinding, and create a more modular final product. This week, our focus is on further refining the CAD model by repositioning screws for better placement and reinforcing the structure to improve its rigidity. Moreover, we will be migrating our control code from the Arduino board to the Raspberry Pi using Firmata/Pymata. This change is intended to ensure that the management of the motors and heating systems is seamless and without interference.
(3/3/2025) Parts have been ordered for the new 400W heater, which should significantly reduce enclosure heat-up time. We also ordered a PWM-controlled AC dimmer for analog heating control. After testing with Firmata, we decided to update to Telemetrix for improved stepper motor control. However, these protocols only communicate input changes, so filament sensor states are unknown on startup. We’re addressing this with a txt/config file to store device states for use on boot. This week, we refined the roll stand modules, nearing completion, and worked on the Arduino and Raspberry Pi control environment. The focus remains on resolving the startup issue caused by Firmata’s input handling limitations.
(3/9/2025) We are beginning work on the wiring diagram and will also replace the current switch with a more suitable option. As a team, we are finalizing the design of the new electronics box and preparing it to be printed in sections. Our goal is to complete and assemble the new physical components by the end of this week or early next week.
(3/16/2025) This week, we are going to finish organizing the wire diagram/schematic. We decided to try and do it in a program called KiCad. We are also making our presentation for the week to keep updated. We are also finishing up the box for the project and talked about putting a high level block diagram int the presentation.
(3/23/2025) We are currently in the final stages of completing our KiCad sketch for the schematic design, which is progressing well. Most of the prototype has been assembled successfully, with the exception of the electronics box that is yet to be completed. The movement system is fully functional, marking a significant milestone in our project. Our next focus will be on refining the control systems to enhance performance and reliability. Once the electronics box is finalized, we plan to conduct thorough tests within the week to ensure everything works as intended and identify areas for further improvement.
(3/30/2025) The project is nearly complete and functioning well. We’ve successfully implemented filament swapping, retraction, feeding, temperature control for filament drying, and printer operation. The remaining challenge some team members are addressing involves the Octoprint custom commands plugin. Specifically, it’s failing to execute the Python code and shell scripts needed to initiate a filament swap when a tool change command is triggered in the 3D printing G-code. Aside from this issue, the device looks impressive and has come together as a well-designed project. I’ve completed organizing and labeling the KiCad design for clarity, and we’re now testing everything to ensure it works as expected for this week’s checkoff.
(4/6/2025) This past week marked a significant milestone in our project as we successfully concluded the review process, meeting all fundamental requirements. Early in the week, we finalized the assembly of the system, completed the implementation of the control code, and conducted our first comprehensive test of the setup. The initial test was successful, as we achieved the primary objective of printing. However, we identified several challenges during this phase, including slicer-related issues, mechanical limitations, and some inefficiencies in the code. Despite these hurdles, we are proud to have met the overarching goals of the project. The core functionality is in place, demonstrating that our approach to Filament Flip Flop (FFF) is a viable option for multilateral printing. Moving forward, our focus will shift to addressing the remaining issues and enhancing the reliability of the system. By refining the slicer settings, optimizing the mechanical components, and improving the control code, we aim to ensure smoother operation and elevate FFF to a level where it can effectively compete as a robust and dependable option in multilateral printing. While we have yet to finalize the build and usage documentation, this accomplishment marks a pivotal step in bringing our project to a finish.
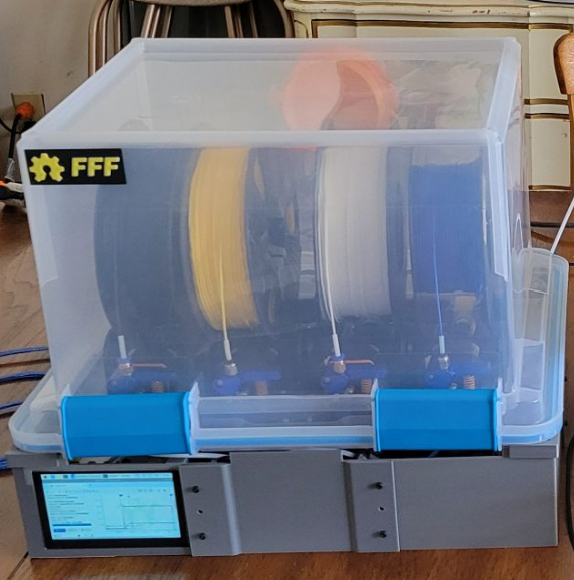
(4/13/2025) This past week we have been working on the report rough draft. In the report, we are providing step-by-step instructions on how to build the product as we did. For the final report, we still need to add the wiring directions, slicer setup, and operation directions. For the most part it’s up to the capstone members to figure out if they want to perfect the last of the project to potentially keep around for future use in OSHE.
(4/20/2025) This past week we watched our capstone members do their final presentations. The team is now doing the final report by cleaning up our report draft to turn in. After that, we will have finished the FFF project and the semester.