Update 9-10 wombo combo
Since last we spoke: I finished the voltage read from the board and passed the code to the rest oof the project team to combine into our total code. It was the channel 0-1 pair being burnt out. I was able to get reasonable readings in all three ranges and pass it on to the rest of the team allowed some time for some coordination and calibration for accurate readings. We created a function from known data and calibrated a correction factor for a given input and range. We passed our project sign off. Woo . Since then we have been working on our documentation. I might also order a second set of components and build myself a meter of my own. We need to assemble some documents that cover the operational theory and background to cover the educational aspect as well.
Update 8:
Since Last week I did a whole heap of trouble shooting for I2c and communication issues with the Adafruit brakeout board, only to find that my code worked the whole time and that channel 0-1 is burnt out probably. Any way I switched my code to read the differential across channels 2-3 and suddenly i was getting voltage measurements that responded to a voltage sweep on my inputs and life was good.
Next week: I need to expand on my code now that I have it working and figure out how to pass which mode the dial select is in. that will set what gain is applied to our output math. for instance I was reading 0.84 volts when passing the board 8.6 volts from the bench, so we would need to multiply the readout by a factor of ten and also do a little bit of calibration for our actual internal resistance values in order to get really accurate readings. As of right now I meet the project spec (Pretty sure)
koncerns… Given that I managed to fry a channel on our break out board I’m thinking about how to fix that issue for the users but we already ordered our PCB so its too late to fix this semester. Well, at this point I’m pretty sure we included breakout pins on the board at the inputs so the user can make a jumper connection to other branches of the differential so maybe they can use the same trick I did to fix it.
Update 7 : Photo:
Since last week: I worked with peter and Caleb to finish selecting components for the board and Peter got the board ordered. We built the circuit on a bread borad again and spent a few hours verifing it operated as intended but we struggled to collect readings with the ADC on the adafruit board we have for testing. Our test bench circuit is sending the ideal signal to the board so now its just a matter of cracking whats going on in the ADAfruit library. might be something with I2c or maybe its a hardware issue with our board. We did end up switching out bread boards to ensure we got the right outputs, because the one we grabbed from the drawer was broke. But ah well, that’s troubleshooting.
To do… try coding for another couple hours with Caleb or peter to decipher the Arduino IDE to get through what’s going on the this circuit. I expect it to be off a bit but we just aren’t getting readings. so that’s not so great.
Concerns… uh, i’m really hoping this works as intended.
Update Project 6: I kept procrastinating with actually working on stuff, so now this is 5 and six. Since My last update I worked pretty hard at getting my voltage read circuit up to spec and doing input protection with Caleb. I worked through a few complicated ideas with my team mates, Dr. Bergstrom, and Dr.Shane before one of my team mates pointed out I made a mistake in reading the data sheet for the ADC and we ended up reworking the circuit we had as part of the meeting we had last Friday to work through the last of PCB design.
TO-DO: finalize PCB board design and ordering, Double check schematics and ensure board passes design rule check. Should be pretty solid.
Double check the switch positions will line up as expected and make notes about that for programming the adc.
familiarize myself with the adafruit library and the arduino IDE, play with the code and the existing module we have.
Concerns… a few. Making sure my work is up to the rigor of capstone level work. My design had to be chopped to fit in order to make the board deadline and I’m not sure if the accuracy will be there in the measurement as we shipped it. It will work. It will read. I’m not sure it will read well.
Update 4.5: spring break training montage.
Todo. Copy hassell file onto new SD card. *done*
Print one bracket (in progress)
Watch two lectures *done.*
connect to github on desktop and figure out how to upload my schematic to team drive. continue work on the full schematic from data sheet to make the ADC happy.
Double check with team about ordering parts.
Double check about break out board.
Charge DSLR camera to bring with for next week.
Secure apartment for Internship. (SOON)
Call bank for same. ^^^
—–fiddle with pen
Update 4: 2/20/2025
A few days late but I have a to do list
Last week was CDR. I managed to get our presentation done and helped host CDR. Not a lot of work was done on the project. I have further developed the model we have for the voltage divider after looking at the data sheet for things like pull up resistors. I created a new github account to work with the team.
For this week I need to add my voltage divider schematic to the larger team schematic and get with peter for what parts we are ordering.
I think we just got the voltage divider break out board so I need to play with the physical circuit. I also have some 3d printing to do over the break.
For
Update 2/5/2025
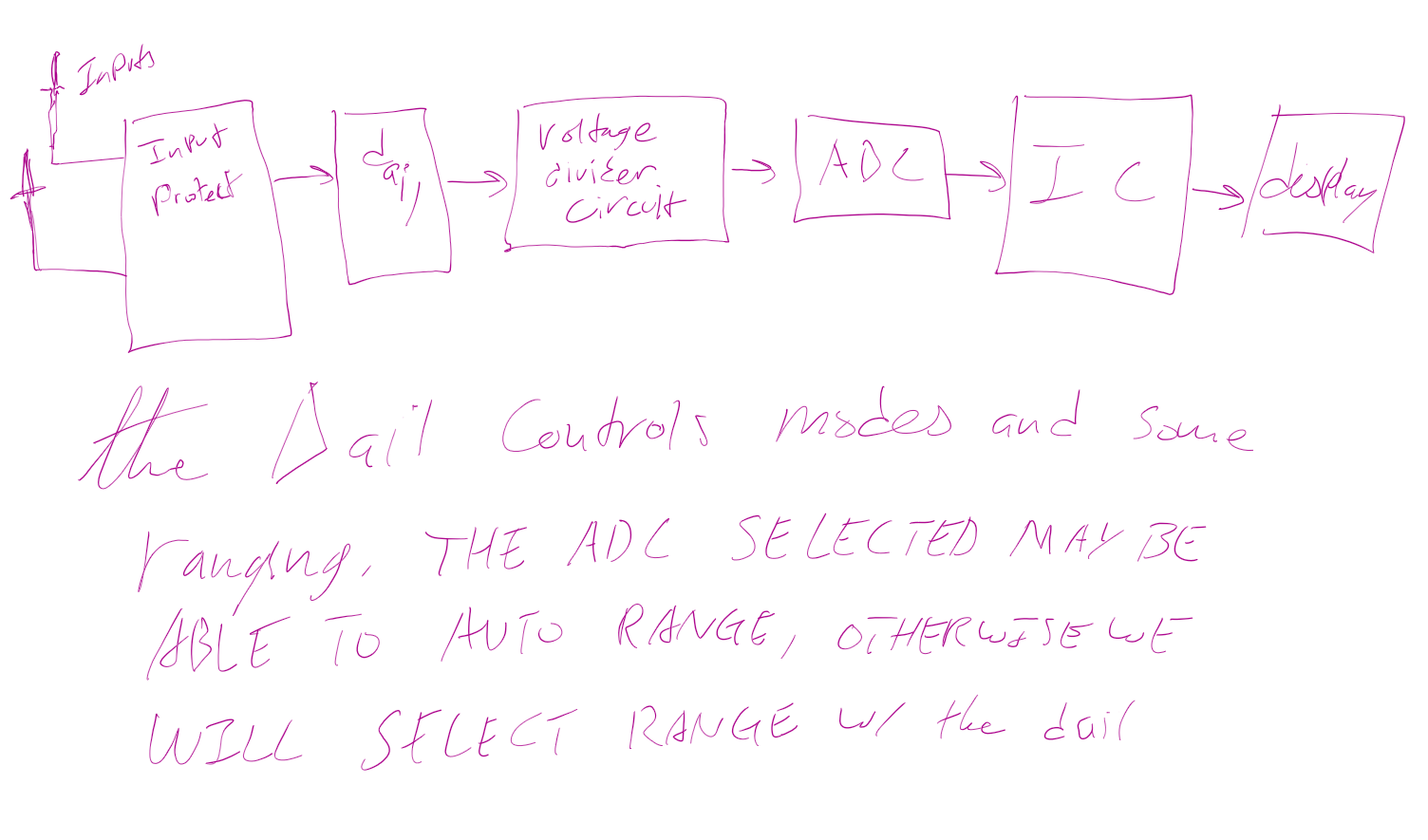
Mode select dial will most likely be setting our range unless we can figure out if the library we are using supports auto ranging. we currently plan to have 4-5 range spots for voltage measurement which is my responsibility.
Last week I was able to create a schematic for the voltage measurement circuit and our team was able to decide on which ADC to order that has 16 bits and I2C support. we are planning for cdr and working on our slides.
My to do list includes neatening up the schematic for the voltage circuit and finishing my slides for CDR. I need to find a meeting place for the Thursday’s section of CDR. I suspect we will use the maker space but I have a couple emails to send first.
I worry about way too many things to really list a concern. Have a good week.
Update 1/26.2025
I feel like we just did the last one a few minutes ago.
Reflect on what you were able to complete last week. What items need to get moved onto your To Do list for this next week? Which items are no longer necessary?
I watched the rest of a schematic tips and tricks video so That’s gone. I have a couple more on PCB design still to watch, but I’m kinda in the need to move onto more focused Research for our project and those videos add up to a couple hours of watching which is hard to find. Those might get dropped in favor of my core responsibilities I took the responsibility for the ADC and buffer circuit for DMM so I need to dive into data sheets and some reference libraries for how Multimeters do stepdown in order to not fry ADC’s. One of my team mates is working on input protection and I need to see what he comes up with as his work is higher up the signal chain from me which will affect my design choices.
Create YOUR To Do list for the coming week – and make it as exhaustive as you can. Start with a goal and break it up into as many pieces as you feel makes sense.
-Research multimeter signal stepdown. how is 600 v broken down into something an ADC can use without frying?
-Hammer out exactly what the measurement specs are going to be with team.
-Start work on: Create input circuit to an ADC to measure voltage and current .
Finish is possible PCB design video to be helpful with team design coming up soon,
List any concerns you might have about the next week. I am concerned about the world at large… I’m getting distracted by current events and its not super helpful. Its also career fair week and its getting to be exam season. time is going really fast this semester.
Update 1/23/2025:
- Upload YOUR sketch of what the project might look at the end of the semester. It doesn’t have to be a perfect picture, but try and include as many details and annotations as you can.
- Create YOUR To Do list for the coming week – and make it as exhaustive as you can. Start with a goal and break it up into as many pieces as you feel makes sense.
- List any concerns you might have about the next week.
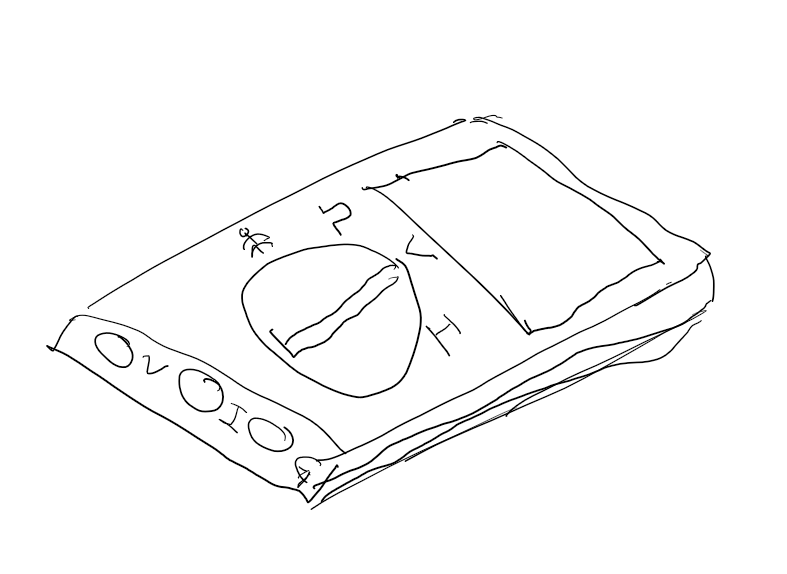
TODO
Finish research video playlist I have on schematic, PCB design, and Existing Multimeter projects.
Attempt to find a solution to ADC , find a 12 or 16 bit ADC that will play nice with our circuit.
– I need to find a way to step down my inputs to levels that the ADC can handle without burning out. This is a solved problem I just need the right term to search for to find it to go researching it.
My goal is to start designing the circuit by the end of week 4, so we can design a pcb week 5 and order parts by week 6 or 7.
Concerns. : not knowing what the heck to select for an ADC and not knowing what exact voltage range we want to measure.
Update 1/17/2025
Switched to Digital multimeter. this week wo completed work assignments for our team to split and work on. We are searching for good parts, practices, and existing topologies to adapt to our own needs. That’s mostly going to be over the weekend, and might require some discord meetings and the like.
Update 10/13 2024
There hasn’t been a formal update assignment for two weeks, but here’s what I’ve been doing since CDR. I got with Shane and ordered a new relay for the solar unit. A few days later I’ve installed the wires into the relay for the power side, which was straight forward. I need to order or modify some leads from the PI GPIO connections. for our secondary goals, I estimated the battery life of the solar unit using a multimeter. The average current draw at the batter with sound playing was around .3-.35 amps, but the highest value I saw spiked to 0.4 so that’s the worst case I used for my estimate math. 35 amp hours divided by .4 amps gives a battery life estimate of 87.5 hours of continuous operation. That’s worst case draw playing sound full volume with no charging for over three days straight. using .3 gave 116 hours so the truth is somewhere in the middle, call it 100 hours. We will test again after fully implementing the relay and disabling a few nonessential draws from the PI. I also used the pi in the lab to draw a menu logic tree, so we can start making instructions for users.
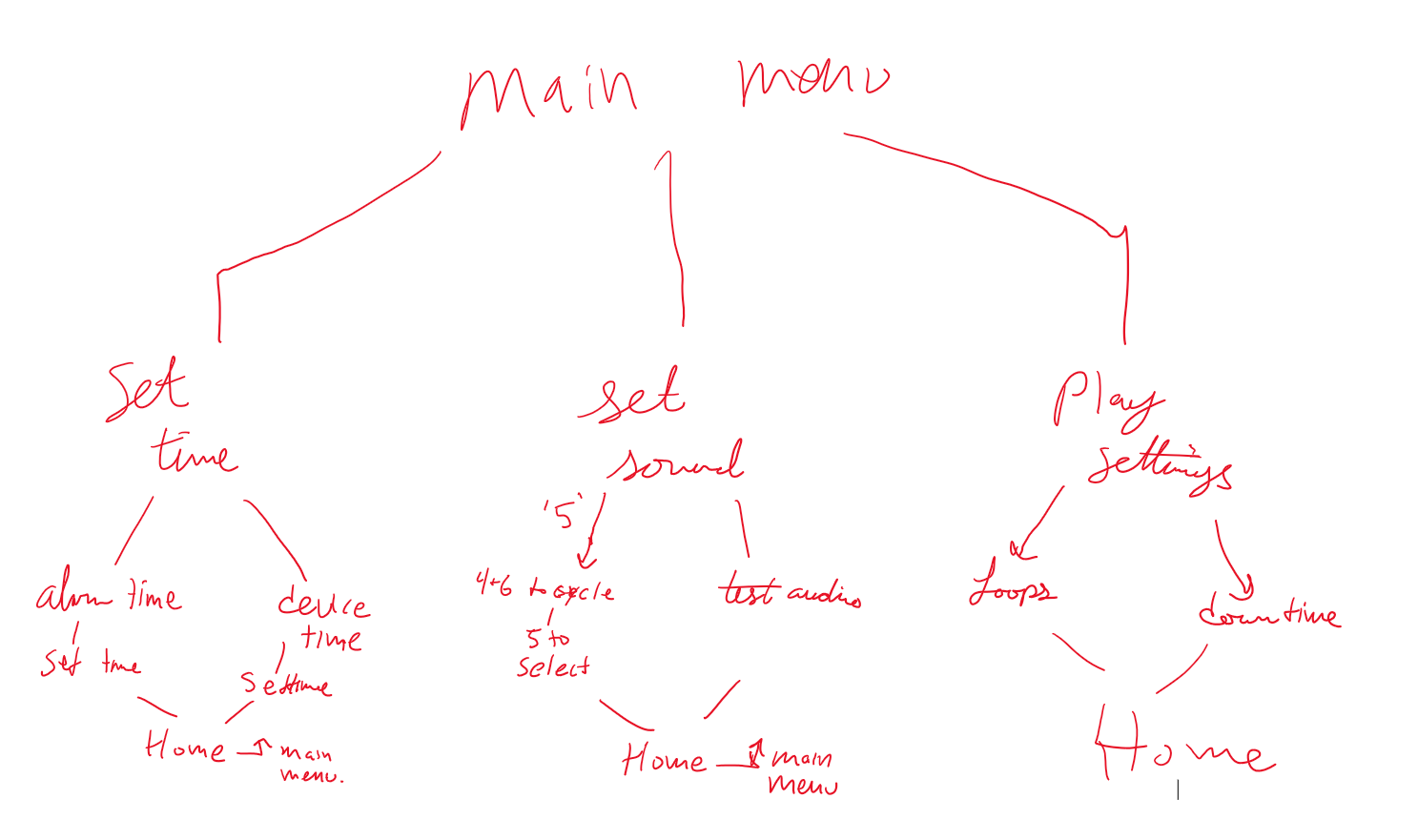
Update 9/29/2024
Completed third solar unit, well its electrically connected and it runs. Still awaiting the RELAY we ordered and then we need to implement that line of code. In the meantime its on hand and running and we can demo it at CDR to answer questions and help present. We also met as a team on Saturday and tested the range of the speakers to establish a baseline, and we got 70dB at 70 feet, and audible data at 500 feet.
To do for this week include the Install for the relay, redo our slide show to be CDR format. I need to contact DR. Wolfe and ask about what sort of hearing range birds have. but I think this should be fine for our standards. If we can cover 1000 feet with two units that works wonderful. Otherwise personally ITs all CDR for me.
For states. Theres a clock menu, and alarm menu, and a file select and test page. more will be implemented.
- Update 9/22/2024
Parts ordered for next solar unit update. Did a bunch of work for prepping CDR, I need to order a relay to splice into the new solar unit I’m building, and get to work on routing all the lines in there. the team has been refactoring code. I’m awaiting connectors to come in to finish the third solar unit. I
need to make a good two hours to assemble and modify the thing.
- Update 9/13/2024
Switched to bird attractant and deterrent over the summer, then Dr.Shane named it SKY SHEPARD. which is sorta neat.
Since school started we did outdoor testing, discovered a fault in the wiring of solar case 2, replaced the wires and tested the solar unit before solar1 and solar2 were deployed for testing in Chicago. Lots of back and forth but its done.
Project update
will upload photo at home when my phone pushes the photos to google.
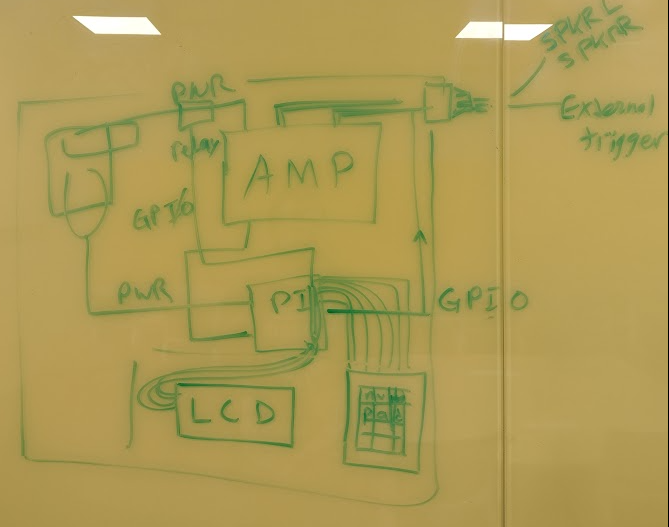
TODO;
Ask for an update after the weekend for the other project Idea Shane was asking about.
Order a new set of terminal connectors, need to be large enough for the bolt gauge in the solar kit.
Wire hot and return terminals.
drill bracket into solar case no.3.
flash new copy of pi with refactored code.
Update 4/20/2024
Xavier was able to make the freecad files for the 3d print of the faceplate as per my last update. We got our presentation put together from the EMI sponsorship meeting and we have a fairly decent idea of what the project is going to look like next semester in order to hit the ground running as early as possible. That includes what tests to do, what tasks have priority, and what the goals of the project going forward are. Those being specifically a focus on assembling and testing the Extruder at varying speed, temperature, and mixture settings to get good material.
As for tasks this week. I’m going to make a time to go to the oshe lab around 10-11 AM and start the print for the face plate. It’s a bit on the big side and the computer says it will take 7 or 8 hours to finish which means we will have to baby sit this thing through the day, which has been part of why we haven’t gotten to it yet over the weekend. Once we get face plate in hand we can mount the Screen and two inkbirds to the frame and connect the wiring for the heater coils and the thermistors and the supporting wiring. That’s really the only big thing left to try to squeeze in this semester.
Other than that its going to be our group getting together at our usual meeting time to work on the semester report together. between final exams and the report I don’t think we are going to get plastic extruded from our device this semester without rushing and doing something unsafe.
Update4/13/2024
The project is wrapping up for the semester which is kinda sad. We are devoting most of our time to reports and documentation rather than forward progress on the module as it stands.
If I can find time for it I want to get with Xavier and finish making the freecad files for the controls box to mount on the frame. He said he was going to work on that and I taught him how to navigate free cad enough to get by. I designed the faceplate with him sitting over my shoulder. we drew up the technical drawing to work out dimensions. It will hold the two inkbirds and the display we are going to connect to our control menu stuff. I would like to push myself to finish a block to hold it all as that would make mounting everything MUCH easier but I can see us running out of time in the next few days and just having a half built final project. I know that as it stands the inkbirds can be wired in and powered on to prove that our idea works, but as this is version 7? 8? we already know it works as proof of concept. Konnor (our sorta project lead?) stated that we are just going to do what we can and not rush the first operation and testing that we will use for the beginning of next semester. then we can do all the testing for what speed to set the motor, what temp to set the inkbirds, and what percent recycled material to use.
As it stands we have most if not all the pieces we need to finally get somewhere, but its time to pack it up. I guess it would best be used to make a list of tasks for next semester… or maybe I could ask Shane If i could pop into the lab over summer? really I just need to do some 3d printing and routing of the wiring.
Focusing less on the material which is at work stoppage its time to talk about
For this week I have been working on the EMI presentation that we borrowed(stole) from Growbot. We are going to start giving updates to GM on a regular basis as part of their mentorship/partnership. I’m reworking one of thier old presentations to make a template so we have all the headings and formatting done and going form there.
Make template
fill in 1st presentation stuff.
assist in all the end of term documentaion and paperwork.
update 4/4/2024
We wrapped the barrel in heat tape and wire to get ready for actually heating plastic this weekend and also got the faceplate for the control panel created in CAD.
We are looking for the right connectors to connect the nicad wire to the ink birds without having to half disassemble the recycle bot each time we need to get into the barrel. quick disconnects and high temps are a bit of a thing to work around. we are thinking ceramic connectors, need to go digging to see if any are on hand. hooking up the connections the hard way wouldn’t be the end of the world, just not very nice looking and it gives us more work later.
current task is getting the barrel heated and trying to dial in the heat zones. to do that we need to get the mounting for the ink birds figured out and then power them. power shouldn’t be an issue, we have wiring and the power supply is wired up. need to double check the output on the DC meter to make sure we are giving the birds what they want to be happy. might need to adjust the potentiometer on the output side to make sure voltages are correct. at first glance it looks like 3-32 v input.
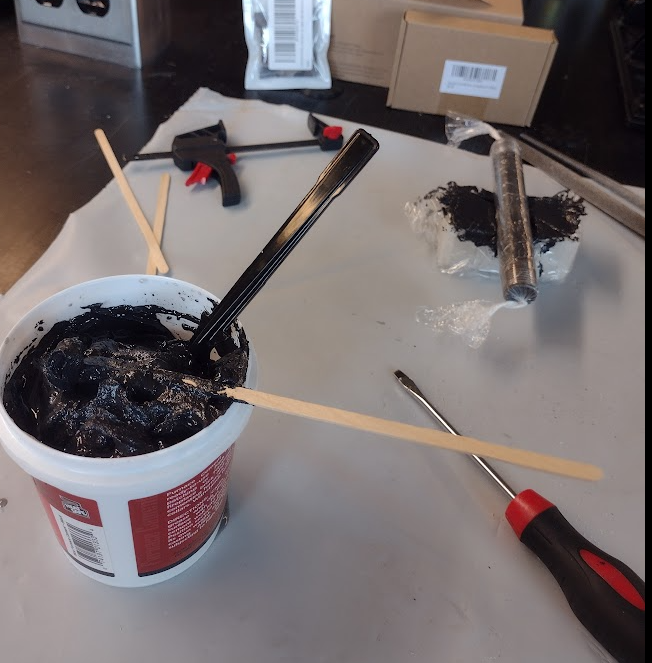
- UPDATE 9- 3/31/20204
- Hopper 3d print worked out for the mold, but the mold itself didn’t. I’m going to shelve it for now after discussing the project requirements with some of the other members. In a nutshell I’m going to knock together a temporary funnel going into the top of the extrusion barrel out of a sheet of aluminum. this has long term drawbacks but given where we are in the semester we can still have a working product on the cheap and in a hurry.
- I will revisit making the part long term out of a different clay and I can reuse all the work I did in the first place to make the mold and design something in line with our longer term goal.
- Since we got funding there has been a design goal add from the sponsor folks that comes down to chasing the highest quality out of our build, and that means changing our design approach for at least how we prepare filament like oven baking it and then quickly mixing it when extra dry. or desiccating it , or a combo of the two.
- Update 8 – 3/23/2024
- Made the negative of the part from the picture below and 3d printed the mold. I realized what i was doing wrong with the boolean print I was making, and it was indeed something simple with menu navigation.
- I need to go in to the lab Tuesday and make an attempt at molding this part into reality. Might need to drill some holes into the top/ bottom of the mold or the part when I’m done. gonna see if this method really works or not. It seems like a good idea, but Its improvisation with a bit of planning. The question is if I have selected the correct material or not, but the design/print for the part is well built.
- As a group we FINALLY got funding and we gave a parts list to order to our group to get ahold of. its running late and assuming stuff ships fast we can start getting everything we looked at built. its our biggest concern to make it work.
- I’m waiting to mount this part till we get a bracket built for the heat tube and its… a thing. gotta see what we can pull off. its going to hit crunch time, and if we are lucky we will be able to have parts when that happens.
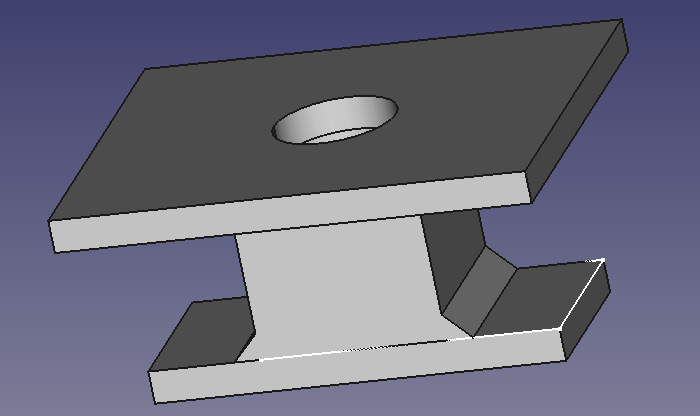
- UPDATE 3/17/2024
- Creating bracket mold. I sourced a material form the local hardware store for under 10$ its a fireplace mortar that is rated to up to 2000*F, and should harden to support the bracket and the hopper full of plastic. might not be the best large scale solution, but it will work and be safe. I was also able to do a crash course in FreeCad and make a 3d print design of what size the bracket should be. Now that i have that ironed out, I’m making a negative of that part. I’m stuck trying to make it with Boolean subtraction, which should make a perfect negative of what i want in a mold, but it’s kind of janky doing that operation in free cad. My next resort is to just sketch a negative of the part i designed and make it that way, which should take me like a solid hour of work when I make time for it. The plan is to make the negative one way or the other, print off the mold that results from it, and fill that mold using the fireplace cement to make a small part that is thermally immune to our heat tube and then attach the hopper to the top and we are in business for feeding plastic into the hopper.
- concerns – making sure we get the frame assembled and get the pieces working together before we hit the busy time for all classes and reports is kind of buzzing in the back of my mind. I think we can do it, but we have to really get on it. we are still missing parts like the NIcad wire we should have and the second inkbird, which to be fair is sorta optional. 1 will work, 2 would give better response and control for heating the plastic without overdoing it. it all comes back to waiting on our outside funding to go shopping and shipping for stuff. We got the frame cut this week and that helps a lot, so we can start putting the pieces together to have something to show for the time that has gone by, but I can already tell there’s going to be a big crunch later when we get everything together, and whether or not it works out comes down to Konnor’s contact coming through on funding.
- UPDATE 3/10/2024
- TODO lsit stuff.
- Learning Free Cad to design a negative of the bracket we are building. We decided against wood as overtime it would break down at the molecular level if exposed to constant heat. Making a print is proving difficult as the part has awkward tolerances that don’t really match up. like the corner screw holes match up by a millimeter or so. trail and error. We are looking at making the part we need out of clay/ ceramic.
- I have about half the design done, having trouble making an extrusion/ Pad. its slow going but pretty neat. the plan is to make a model of the thing we want, invert that and use the negative print to act as a frame for making ceramic.
- I still need to go to a hardware store and see what kind of clays are available that can handle heat. honestly I might be over engineering it, we could get away with placing a dowel in the center, installing some long post screws into the holes and then just molding a big blob of clay around the dowel and screws then fire it and move on with an ugly easy part. it might turn into a thing where I need to make a negative mold even larger like casting. where I make a shroud for the outer dimensions of the part.
- I need to check in with the other members as we are going to start assembly this week. cutting the frame and mounting components. so there’s a small time crunch on the bracket and prototyping. but thats the joy of prototyping.
- UPDATE 2/18/2024
- taking measurements form the part, create a sketch design bracket for the hopper the meet the heated parts.
- Oshe CDR sched.
- Group slides
- check about buying status again.
- get with others about CDR presentation.
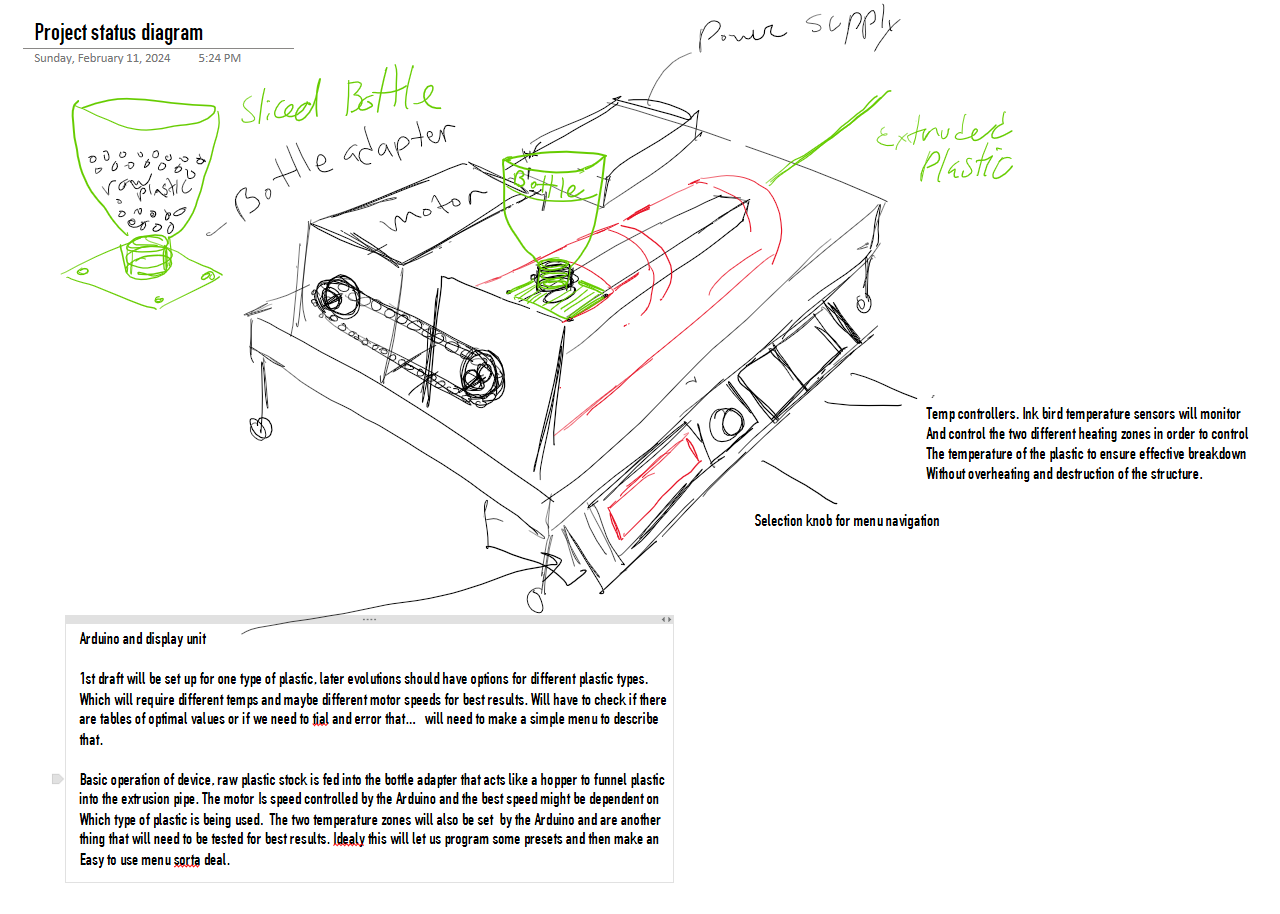
- 2024-02-04 to do list
- still need to check with others in group about making sure all bits are bought.
- talk with team about some of the smaller details like quality of life details. (lights to indicate heat sources are on?)
- double check with shane on CDR.
- 2024-02-03 To do list . Rough electronics parts list completed. not up to full parts numbers or sourcing for buying components but a list of all the big parts is together.
- Check in with team about the funding meeting and try to close out our project shopping / order list.
- Look for a generic voltage supply since ours was scrounged from an old project and will make our build a little janky.
- Compile results from whenisgood poll.
- CDR!! Get together with Georgia and maybe Shane about CDR and making sure everything is sorta in order. find the best times in the evenings and just tell people to make it. folks might have to miss labs or something but its what it is…. it reminds me of scheduling for dnd, trying to get a gorup of adults together you just have to make a time and full send it.
- concerns: just gotta figure out how to herd 50 cats.
- 2024-01-27 task list for week 4
- Create an electronics parts list for recycle-bot extruder module rebuild. (DONE)
- get together with other members in weekly meeting and ask for requests. (DONE)
- power killswitch questions (kinda vague, not important at this point in the build, dropping it going forward)
- work with team to find a way to hold extrusion barrel to resist torque of motor and to maintain a steady position for easy plastic extrusion. (we have a prototype idea worked out that will need testing once we have the big parts in hand and on the frame)
- check with team for dimensions of barrel on order and seek insulation solution
- bracket under insulation or over insulation from commonly available parts source.
- check with team for dimensions of barrel on order and seek insulation solution
- concerns: still waiting on funding and we are in pre design purgatory.
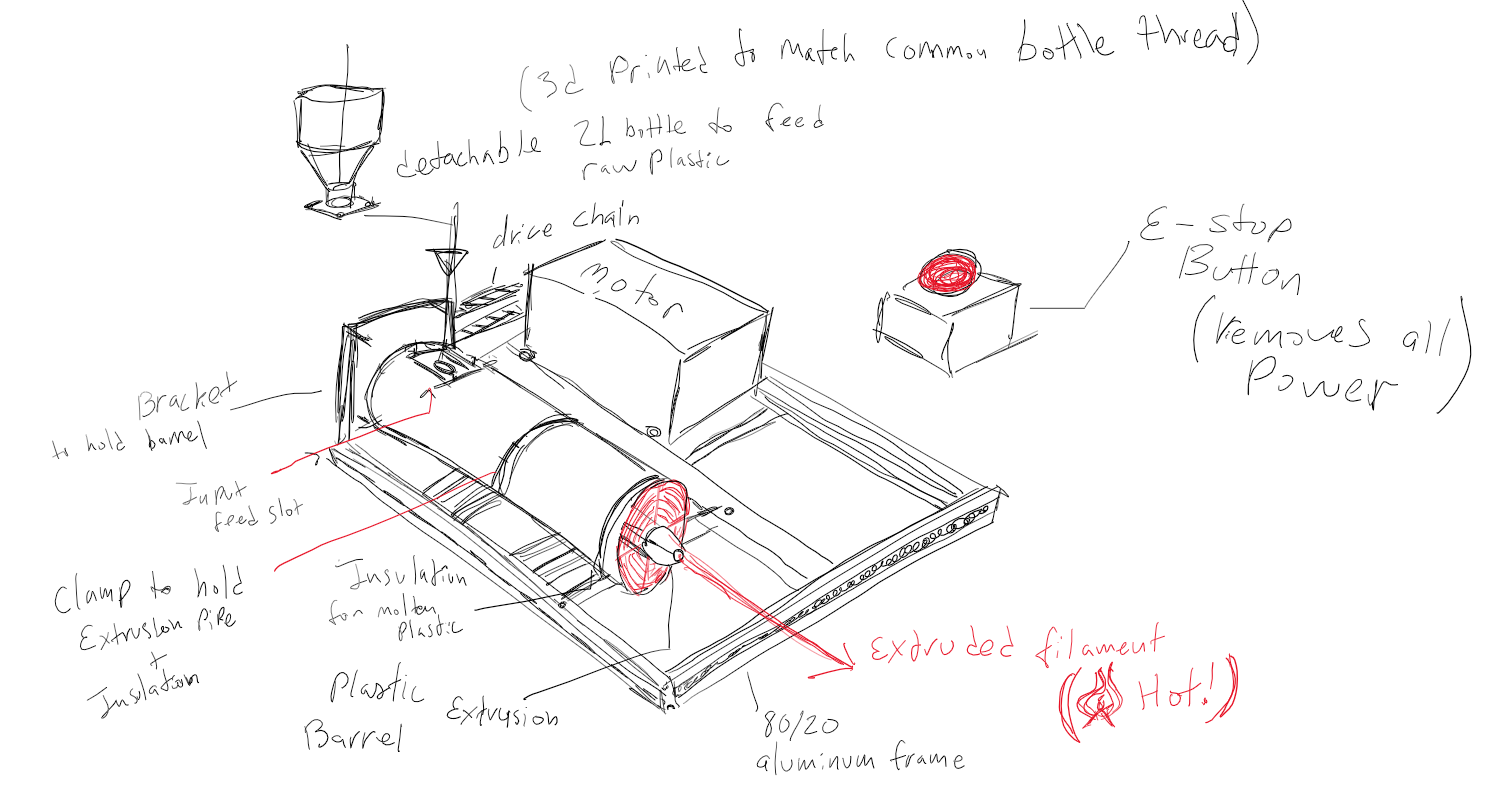