Spring 2025 MultiFX
week 1/6/25 – 1/25/25: These first couple weeks the MultiFX team has been busy. On my end I have been researching Linux audio servers, GUI development approaches such as using QT creator or coding it in pyQT, finding Linux plugin hosts. So far I have started work on developing the “Conductor Program” which will take in rotary encoder inputs, midi inputs, and update the GUI and parameters accordingly. It will also send signals to the plugin host to update the running effects. A lot of the design I want to focus on nonblocking functionality and only responding to signals in order to free up the CPU for DSP time. Thankfully the Raspberry PI has a fast enough processor that it is a little forgiving if something isn’t implemented 100% efficiently. This weekend I will be working on designing the rotary encoder circuit.
1/26/25-2/1/25: Worked more on the Conductor Program along with downloading pipewire for Linux. I made this simple layout to brainstorm how the Conductor Program will interact with all our peripherals and software
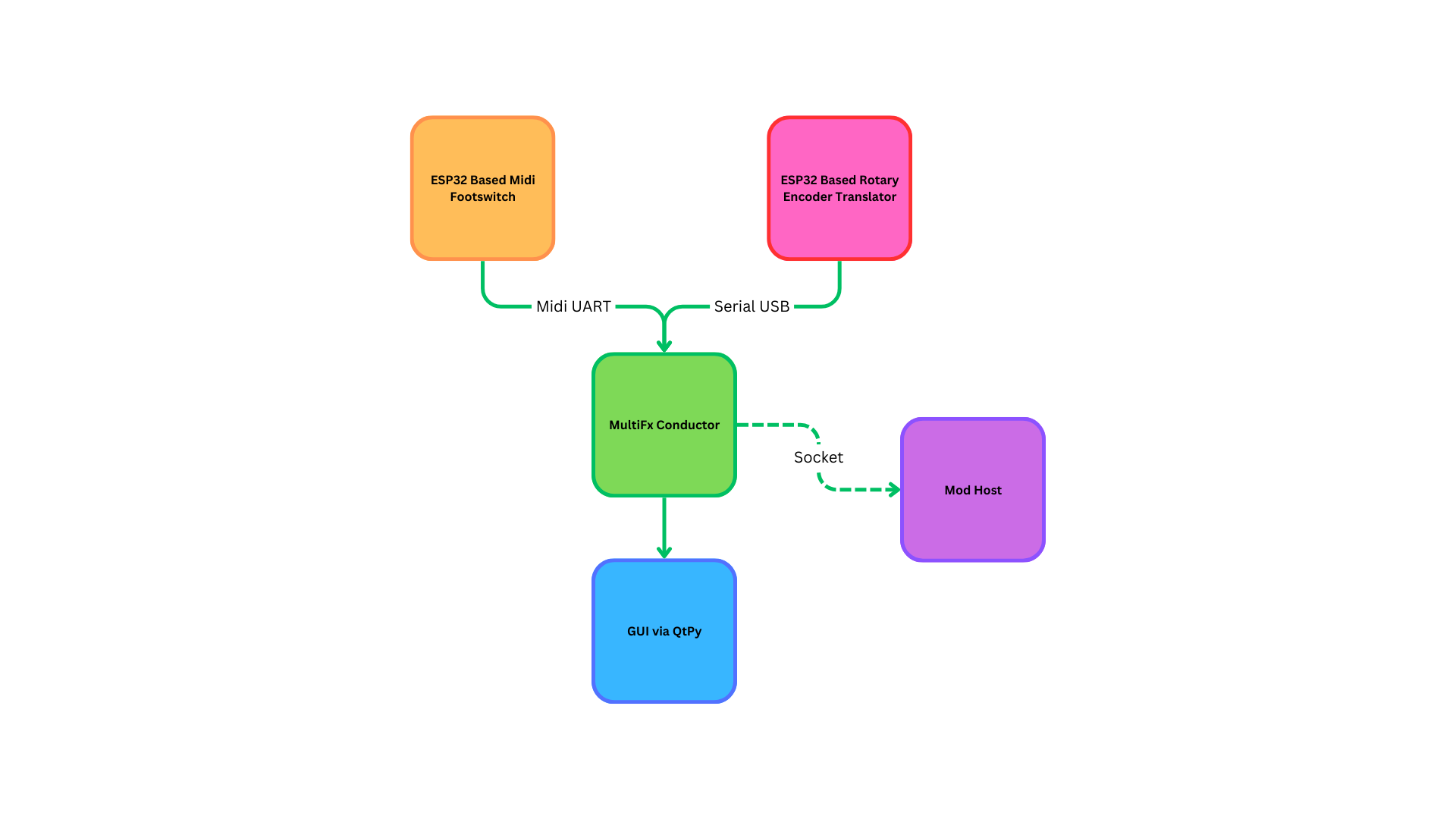
weeks 2/2/25-2/15/25: Over the past three weeks the team has busy working on our deliverables. Some key decisions that were made after research was that we are still moving forward with using jack as our linux audio server for the project. By interfacing with qjackctl it should be simple enough for users to use the patch bay for custom connections or rely on mod host. Another key decision was the use of mod-host as our plugin host. Mod-host will be great to use since it will simple be just socket communications. I have already ran a test where I initiated a plugin and configured its input and output.
When it comes to physical controls I worked a bit making sure our rotary encoder input was handled efficiently and effectively. My first tests concluded that maybe the digital read was too inconsistent due bouncing in the rotary encoder. To fix this I used the analog read to try and get a range of voltage that we know will be a digital 0. Therefore by setting the the analog range less than 25 it resolved most of the issues I was getting where it couldn’t detect if it was going left or right.
My todo list is as follows:
- Make the Arduino code send a serial q,w,e for the first encoder
- Make the Arduino code send a serial a,s,d for the second encoder
- Make the Arduino code send a serial z,x,c for the third encoder
- Make the GUI program have a passthrough button
- Make the GUI programs logic move connections around in jack
3/16/25 – 3/22/25 – This week I finished development on the supporting modules for the GUI. In order to abstract functionality of the GUI to different python classes I decided that the GUI conductor could utilize a manager for the mod-host side of thing and a manager for plugin side of thing. The mod-host manager manages the connection with mod host and is responsible for sending the communication messages. The plugin manager manages the plugin class and helps change parameter values and bypass values. Together these two can call each other and change parameter values in mod-host and keep track of these changes. My biggest addition is the ability to load in plugins via a Json file. This take a preconfigured json file of my own design and initializes a plugin manager based of the json. With this the mod-host manager sets up the patch and allows for real time manipulation of parameters.
3/23/25 – 3/30/25 – This week I finished development on the Conductor GUI. Utilizing the modules modhostmanager.py and pluginmanager.py I was successful in taking in character inputs via the keyboard and changing plugin parameters. One big addition which was made last minute was the ability to load in 3 different preset Pedalboards from Json files. This will hopefully make it easier for the check off and to demonstrate functionality of the MultiFx pedal. My next steps after the check off will be to document how to install the GUI and document how to create the Json files
3/31-4/5/25 – This was the big push to finish out the semester work. The finalizing touches were added to the GUI and the module was built for making it able to be opened on start up. The biggest challenge was assembling the case and ensuring everything ran smoothly. Testing was performed to ensure the rotary encoders, foot switch, and screen worked in conjunction together.
4/6-4/12/25 – This week documentation was worked on for the pedal. The team got together and worked on how the unit was going to be assembled and documented the process with pictures and tips. Also we met with Dr. Pinar and laid out some next semester goals.
4/13-4/20/25 – This week I worked on finalizing the report and migrating all my code into the github. I also documented the code with comments so that future users wanting to edit my code can understand the choice behind some of the QT elements. All I have left are to finish the instillation instructions.
Fall 2024

Week of 9/8/24 – 9/14/24: This week the Viola Pedal board team started to explore whether or not the Delay effect and Reverb effect should be digital or analog. Next week the team has a meeting with Dr. Pinar to see how we could interface our project with his proposed project. If Dr. Pinar’s project seems like the correct direction then we shall focus into developing Digital Delay and Reverb Pedals. My To Do list for the coming week is as follows:
- Work to see what Digital components we would need for our pedals. DAC? PWM generator?
- Decide what embedded system we would need to do the DSP. RaspberryPI? Arduino?
- Start work on the circuitry required for interfacing the embedded system with the Viola.
- Design a mock test circuit and start work on embedded system programming
Week of 9/15/24 – 9/21/24: This week the Pedalboard team had a meeting with Dr. Pinar and completely changed our project to help with his personal project. Our effect will be entirely digital and we will design a multi effect pedal. This required us to take on a Raspberrypi b4. The team did research on what operating system to use for the pi along with what plugin host and developer we are going to us. Ultimately we are going to run elkOs on the Pi and use sushi and JUCE to run the plugins. I did more research on how to develop JUCE plugins.
- Begin work on user interface
- Begin developing JUCE plugins
- Run an already developed JUCE plugin off the raspberrypi
Week of 9/22/24 – 9/29/24: This week the Pedalboard team started work on running JUCE plugins from SUSHI running on the RaspberryPi. We struggled with some of the configuration for sushi and ultimately did not get the plugins running. Future research needs to be done this week in order to progress. Other than that I have been slowly making progress on picking out components for our GUI and interface. My current choice is using a 2.5” HDMI compatible screen along with a rotary encoder trinkey which can hook up to USB adapters on the Pi. My To Do List for the coming week is as follows:
- Begin developing a JUCE Plugin
- Begin work on developing GUI
- Buy components for interface
Spring 2024
1/27/24: This week the RecycleBot team got together to layout what the new iteration of RecycleBot will look like. With the coming changes I started laying out the electrical box and proposing where the best place to put the power supply and heater controllers would be. My To Do list for the coming week is as follows:
- Design a more in-depth controls box
- Decide where power supply, arduino, and wiring will go.
- Decide a final placement on where the power supply may end up
- Explore how to connect motor and power supply to one power cord
- Create electrical parts list and create a draft bill of materials
- Explore thermistor options
- Figure out what electrical items are available within the lab
- Explore funding opportunities
- Set up meeting with Len Switzer and discuss how to join EMI
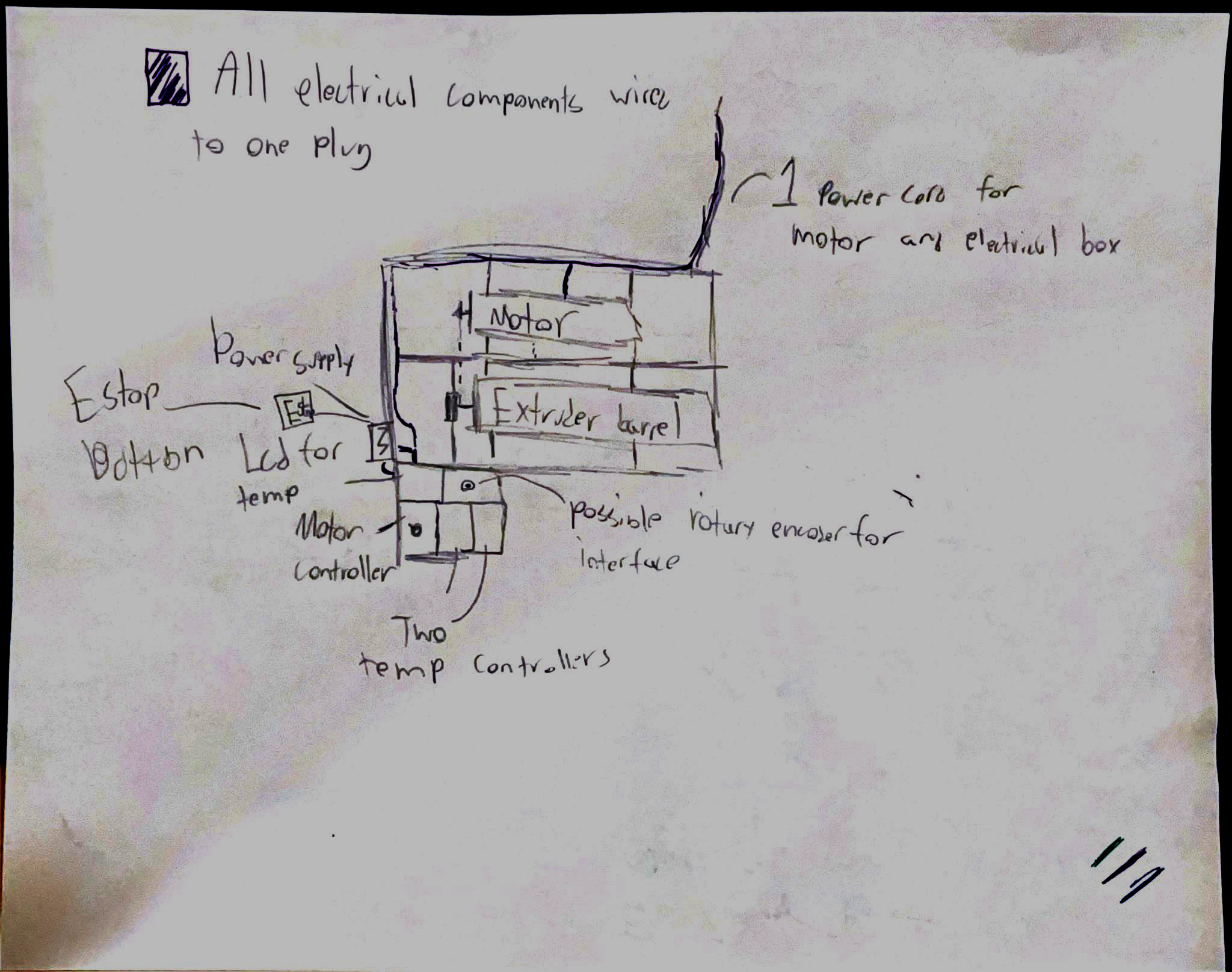
2/3/24: This week with RecycleBot continued its development of the initial layout for the extruder module. It was decided that the electrical box will be developed once the initial frame is constructed. With Aluminum extrusion found within the lab it is possible that RecycleBot will not have to wait for the ordering of more extrusion before we can move on to constructing the frame. I started working on circuit diagrams from initial power supply box and will continue to try and flesh out the electronics box for next week. A meeting with Len Switzer showed us that EMI is a good possibility to try and get RecycleBot funded. My To Do list for the coming weeks is as follows:
- Finish the rough draft of the circuit layout of the electronics box
- Figure out how to wire thermistors and temperature controllers
- Learn how our power supply works
- Continue to work with James to develop the electrical parts list along with bill of materials
- Explore funding opportunities
- Draft a proposal and have it submitted to Len Switzer before winter carnival break
2/24/24: The final draft of the EMI proposal has been submitted to Len Switzer. There will be about a two week period in which the EMI team will look over out proposal and give us funding. With the new extrusion barrel delivered work has been started on the electricals of the system.
3/24/24: Recycle bot team now has to meet with the General Motors committee to accept the funding received through EMI. This will also allow us resources such as experts to discuss our design choices. This week I worked on the wiring layout for recycle bot. My current plan is to use the 80/20 aluminum extrusion to pass the wires from the motor controller through the frame and connect it with the power supply and E-stop button we are using. My To Do list for the coming week is as follows:
- Finish wiring
- Connect first header controller and relay in parallel with the power supply
- Run nichrome wire and wrap with Kapton tape
- Connect power supply to the frame of the recycle bot
- Create a 3d printed box which will hold both heater modules and a LCD screen for extra temperature readings
- Work on web developer work
- Explore possibilities to improve the SEO of the website
- Work on creating a character count limiter for future posts such as author bios and project overviews
3/30/24: This week the Recyclebot team ordered parts. Work has been started on a case for the wiring and I am waiting on the next header controller to be delivered. As soon as the header controller is delivered I will be able to wire them up to the barrel using nichrome wire and Kapton tape. This will achieve our goal of extruding plastic an allow us to start working on testing and optimizing for our barrel. My to do list for the next week is as follows:
- Finish wiring case
- Design case to fit a rotary encoder to interface with the arduino
- Allow for expanability
- Possibly incorporate a section for the motor controller
4/6/24: This week James and I wrapped the Kapton tape around the barrel and wired the Nichrome wire. This process took around an hour since we ensured we had the barrel wrapped correctly. I also did research on wiring the heater controller. During this week talks with bread have revealed we will outsource help from bread in order to integrate bread into the Recyclebot final design for temperature sensing.
4/13/24: The wrapping on the barrel has to be redone in order to ensure none of the Nichrome wire was shorting out. A secondary wrapping of kapton tape was also placed around the Nichrome wire to ensure that the wire does not move around on the barrel. Work has been started on making the slides for our EMI presentation. My to do list for the next week is as follows:
- Print case and wire
- Begin printing on Wednesday afternoon
- Wire on Thursday
- Explore the possibility of a barrel test to test that temperatures will reach out desired threshold.
Fall 2023
9/23/23: Continued my Arduino research by diving into the recyclebot.ino code to understand what libraries and functions that are currently implemented for recycle bot. This researched gave me a better understanding of what code needs to change once some of the other functional requirements get met.
From the meeting held on 9/22/23 my goals moving forward is to research how to have the Arduino act a potentiometer for the new auger motor. I also need to look into adding functions which will allow for us to test the cleaning procedures.
10/6/23:
Looked into ways around using a physical potentiometer. One of the solutions found was outputting variable voltage from the Arduino using the PWM pins and an RC low pass filter. The PWM would pulse 0 and 5 volts and based off the duty cycle we could control the average voltage. The RC low pass filter was to smooth out the pulses to get a more analog steady state voltage. This implementation could have worked although after further research we have ultimately decided to purchase and use a digital potentiometer.
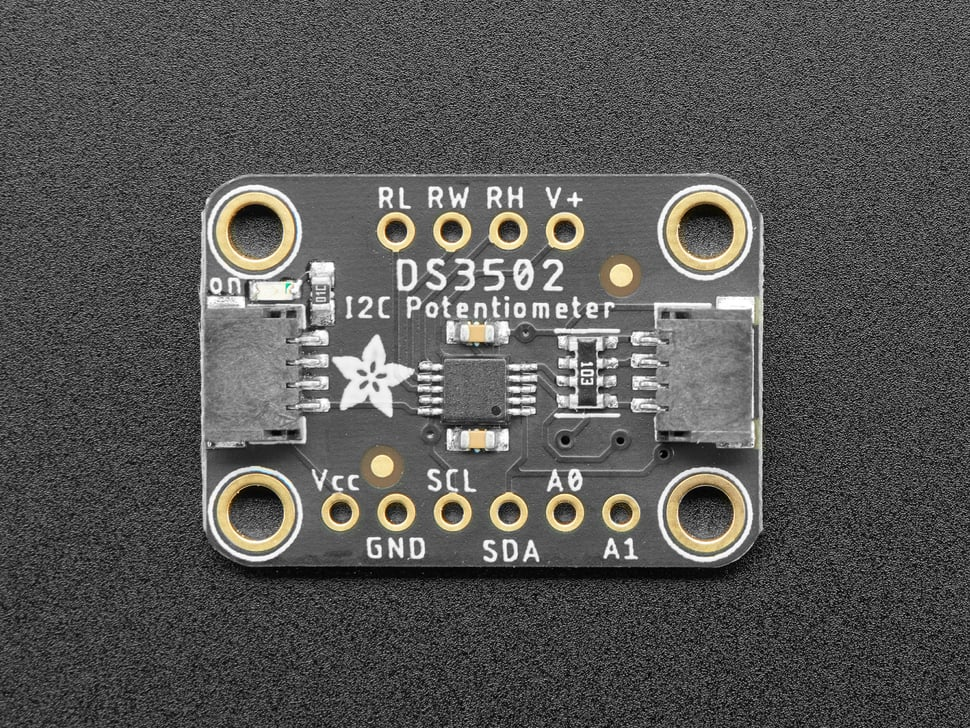
Using the Adafruit DS3502 I2C Digital Potentiometer and the existing open source libraries we can replace the analog potentiometer(pictured below) and have great digital control over the voltage that needs to be inputted into the motor controller. The digital potentiometer’s “wiper” is adjusted base on an integer from 0 – 127. Using the 3.3Vout from the Arduino the wiper can be adjusted from 0 – 96 to control a voltage from 0 -2.5V. I have started on creating test code for the digital potentiometer.
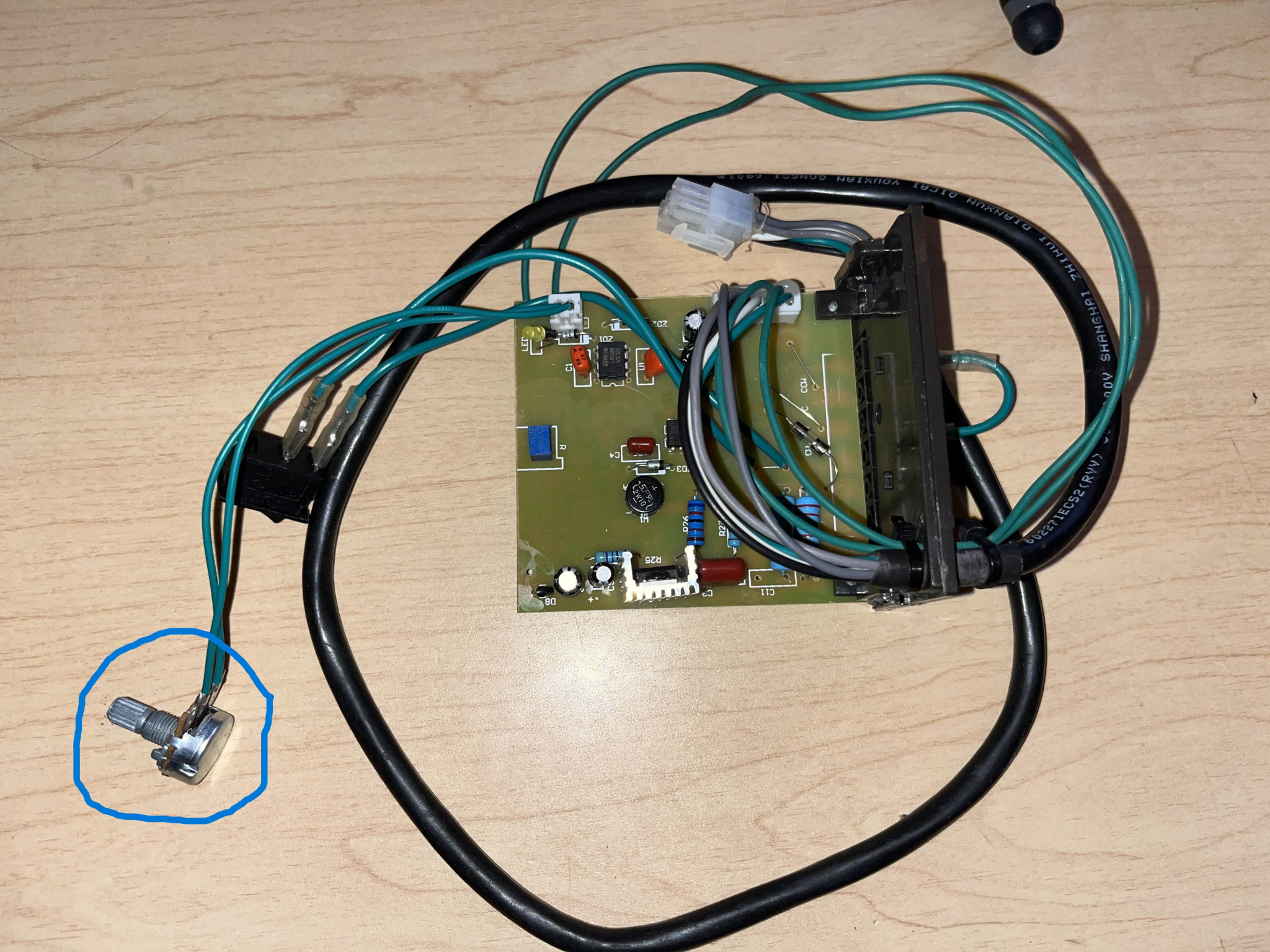
10/28/23
The digital potentiometer was connected via the I2C pins on the motor shield. This caused the LCD display to be connected to the passthrough I2C port on the digital potentiometer. The digital potentiometers RH(Wiper High) RW(Wiper) were soldered in order to connect into the motor controller. Due to the motor putting pressure on the barrel the potentiometer has yet to be tested with recycle bot functioning.
11/4/23
While some of the issues with the motor screw are being resolved I have started work on flowcharting the interface as well as researching how we can interface with the Arduino via the rotary encoder we have. The current idea is to use the rotary encoder to start the extrusion process as well as access menus in which motor speeds could be adjusted.
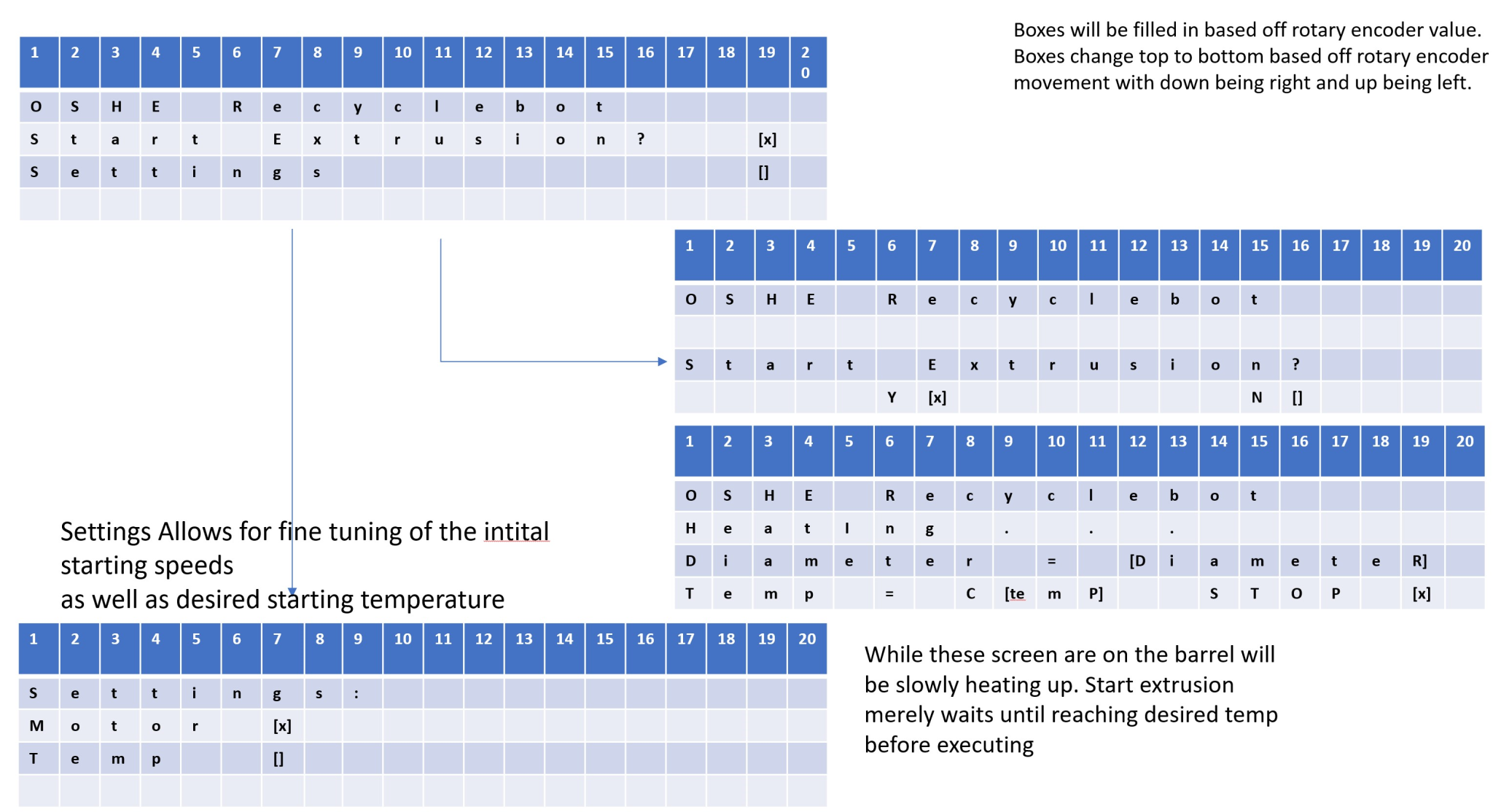