9/22/2023
Nathan Kurth from Chem-trend is sending a sample of ultra purge resin. The purpose of this is to develop a cleaning procedure for the recycle-bot extruder. Once the sample is received sometime next week for trialing can proceed.
Ideas are still being formulated on how to improve the cooling of the filament out of the extruder, but design and construction should begin next week.
10/7/2023
Testing of the purge resin began on 10/6/2023 but due to a break in the connection between the part ant the screw the trial needed to be stopper. A redesigned connection piece is current being made and will be implemented ASAP. This new part will include thicker side walls, PETG material, and 100% fill to increase the sheer strength of the part.
3d Modeling of the first design of the new cooling system has begun and should be completed this coming week.
Next Steps
-Repeat Purge Cycle
-Finish Cooler Design and work on implementation.
10/28/2023
-The motor was reattached using L bracket steel after the it was found that screws were not strong enough. This allowed us to restart the units with the new PETG part that was previous ally printed. Now we need to continue work to reenforce the strength of the unit and continue work on the cooling unit.
11/4/2023
Recyclebot was taking apart due to stress issue stemming from the introduction of ultra purge and a new, stronger motor. Once taking apart it was discovered that recyclebot has critical failures in the hopper and connection parts between the hopper and the barrel. Most of these were caused by the screw itself or the heat from the barrel. The decisions was made that ether a redesign or rebuild will be necessary. What this will look like is still developing.
1/27/2024
Below is a drawing of the new base idea for Recyclebot. This involves an 80/20 aluminum extrusion frame. The plan is to chain drive the unit to allow for gearing and to add shear point to reduce unit damage during operation. In this coming week, we need to finalize part list for the extruder and work on funding to project through EMI. The biggest concern is getting funding in adequate time.
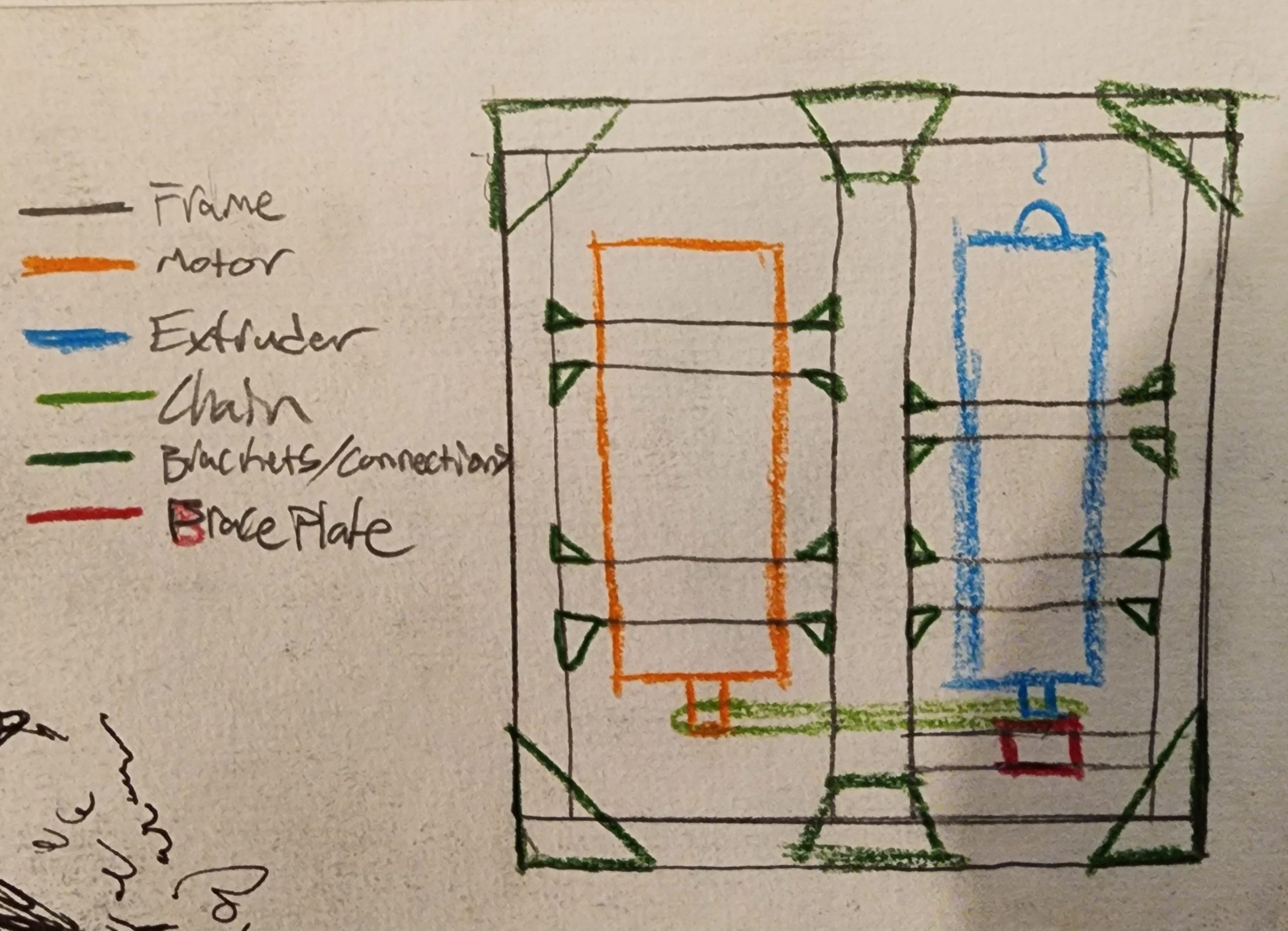
2/3/2024
Recyclebot is still moving forward with the same plan. We are working to finalize parts list and budgets. This will all be rolled into an application to the EMI program for the need funding for Recyclebot.
2/10/2024
Recyclebot is still working on the EMI program application. Will be completed early the week of the 12th.
2/17/2024
Recyclebot is still working on the EMI program application. The rough draft was submitted to the rep to go over before final changes. We also received the barrel and screw unit this week. Recyclebot will begin drafting mounting parts for the frame, motor, and extrusion unit. The picture below is the new extrusion barrel compared to the old barrel.
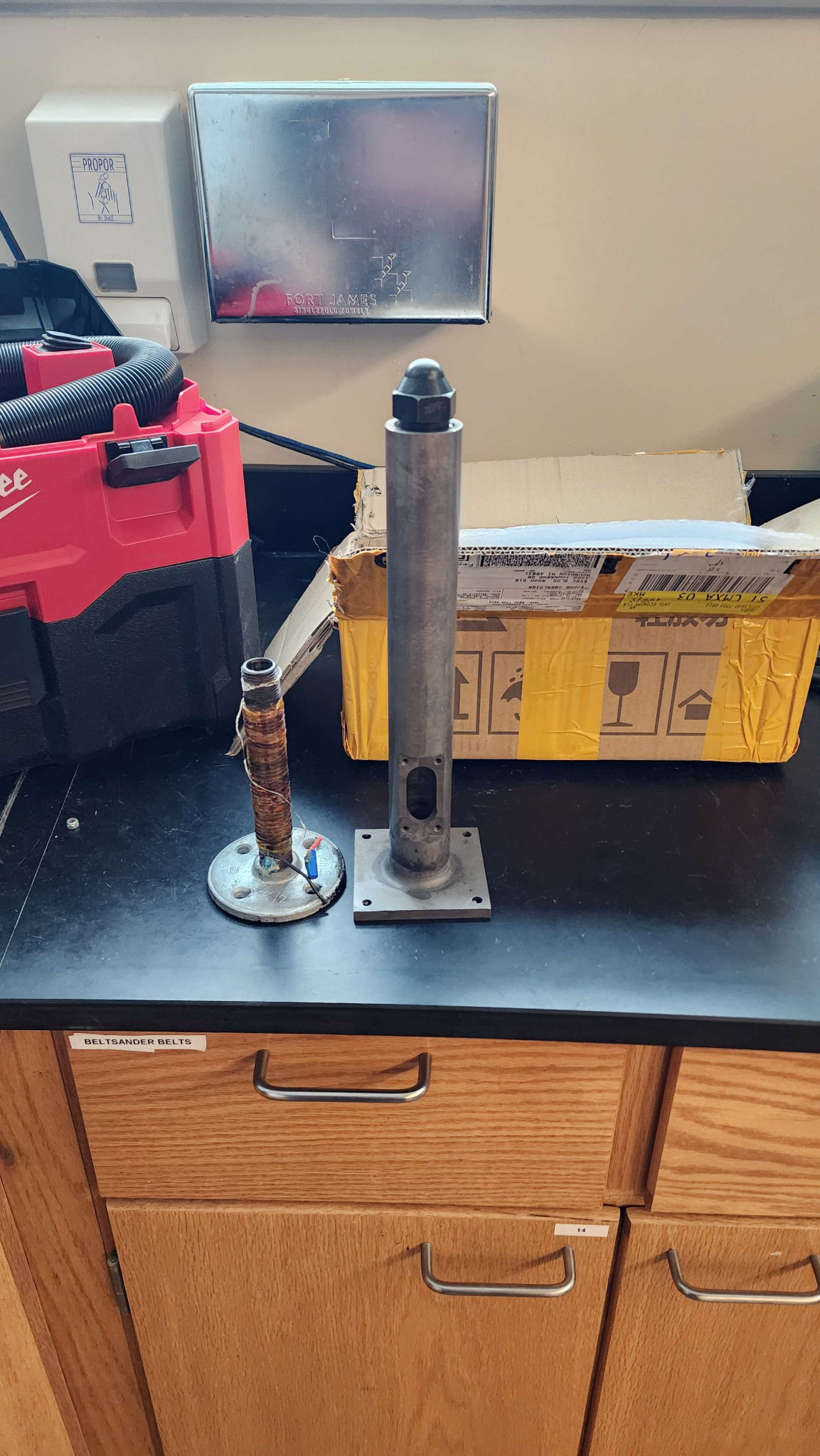
2/24/2024
This week most of the work was done on the CDR presentation. Also, the EMI proposal was submitted to GM.
3/9/2024
This week the team is still waiting for a response from EMI. We are a bit locked down until funding is acquired. Below is the working idea for the barrel mount system. The idea is to use angle iron to mount the barrel to the frame. Then attach a plate to properly behind that to provide the thrust bearing for the screw stop. Next week will being the frame assembly.
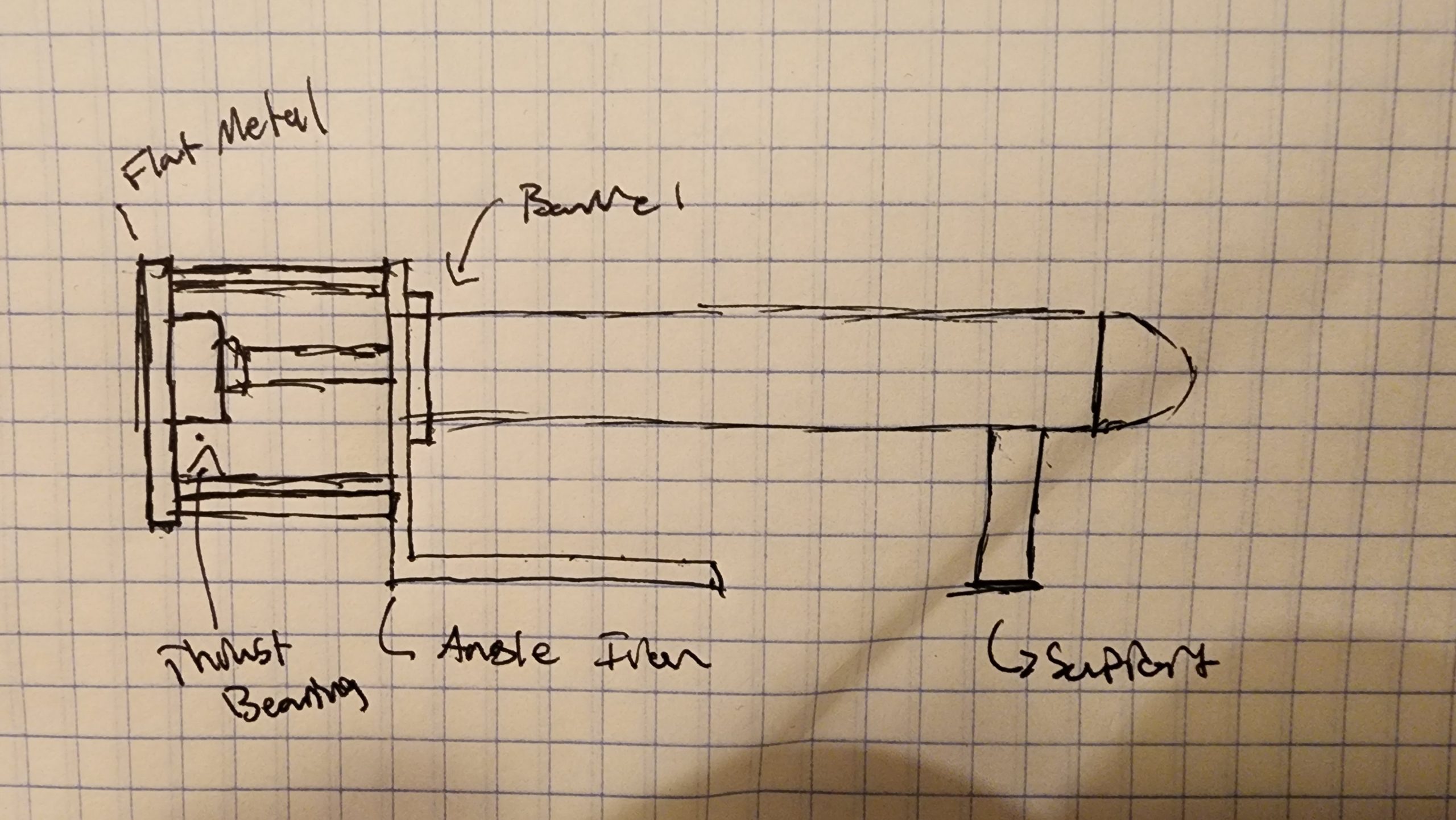
3/16/2024
This week I work on the external portion of the frame of the new Recyclebot. This involved cutting, squaring and mounting double wide extrusion. Next week I will cut the internal supports for the mounting of components.
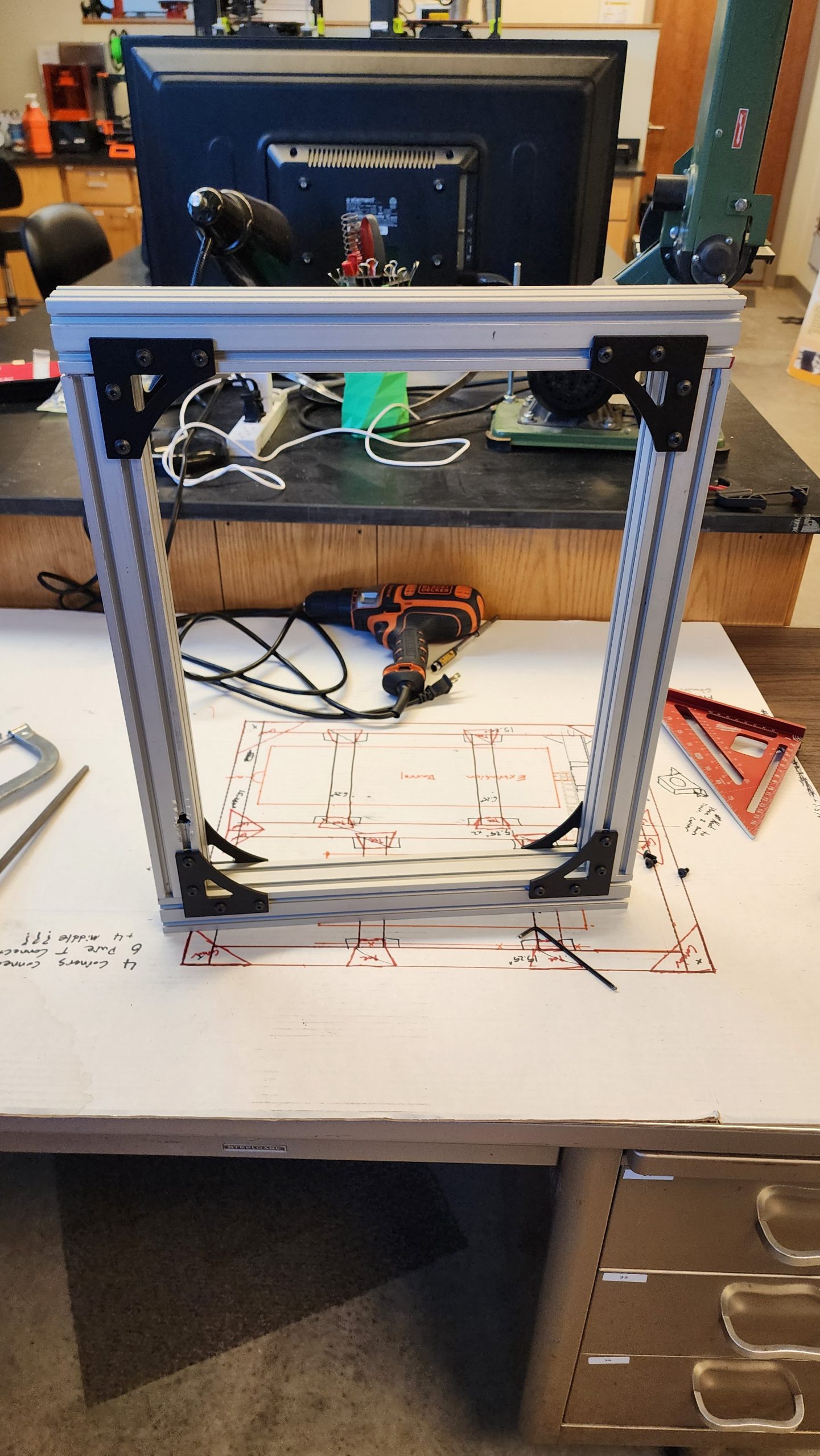
3/24/2024
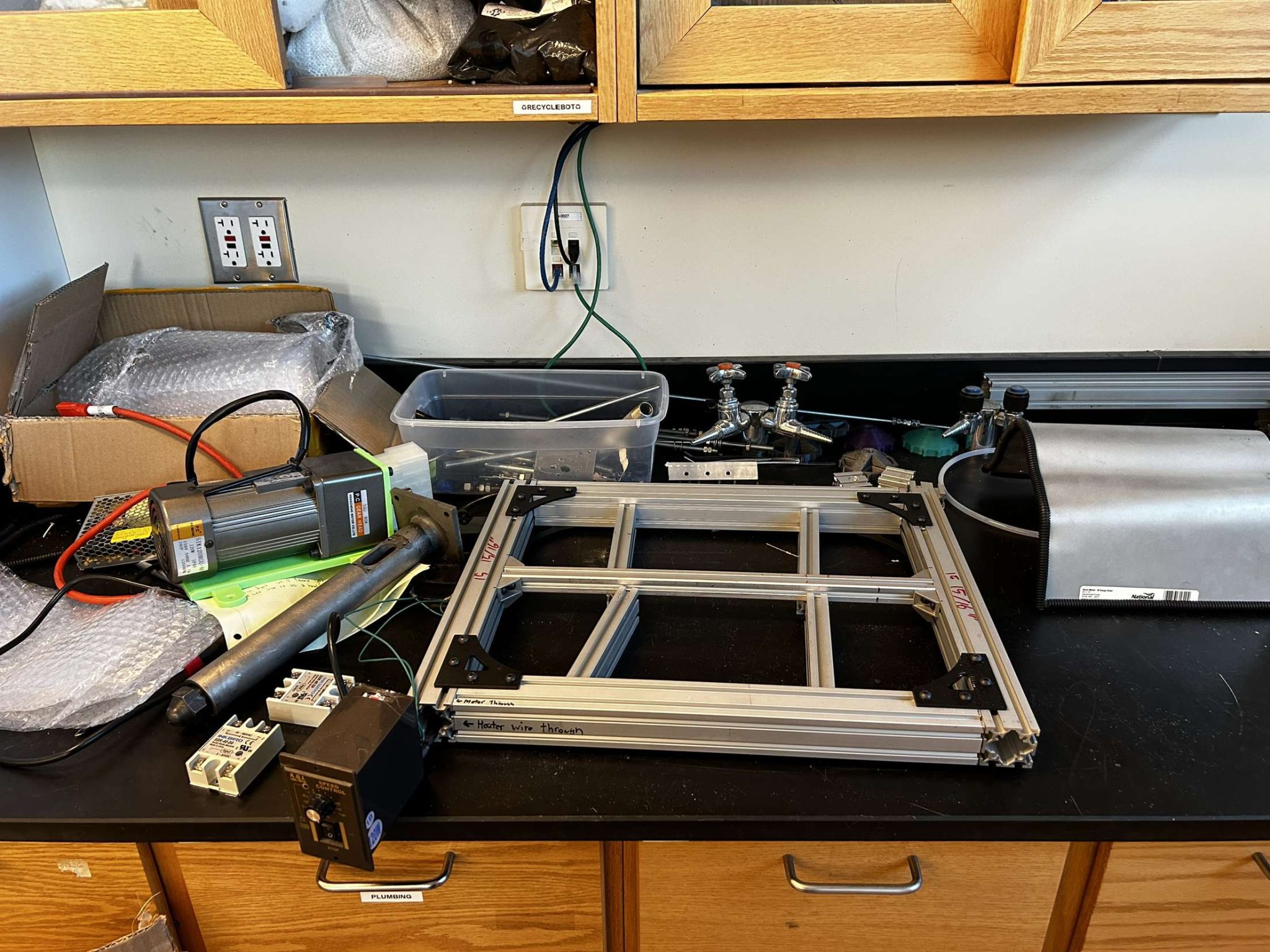
This week I cut the internal frame pieces for the unit, know we can begin the process of mounting the motor and barrel to the frame. We also got word from EMI that Recyclebot should be funded so work will begin with their team to organize the future of the project.
3/31/2024
This week I work on my lab task of going through the 3d filament. This involved a manual inspection of the filament quality. I also order a selection of parts from temperature controllers to gears for the actual units. In the coming week construction will continue. Below is an image with dimensions of the frame so far.
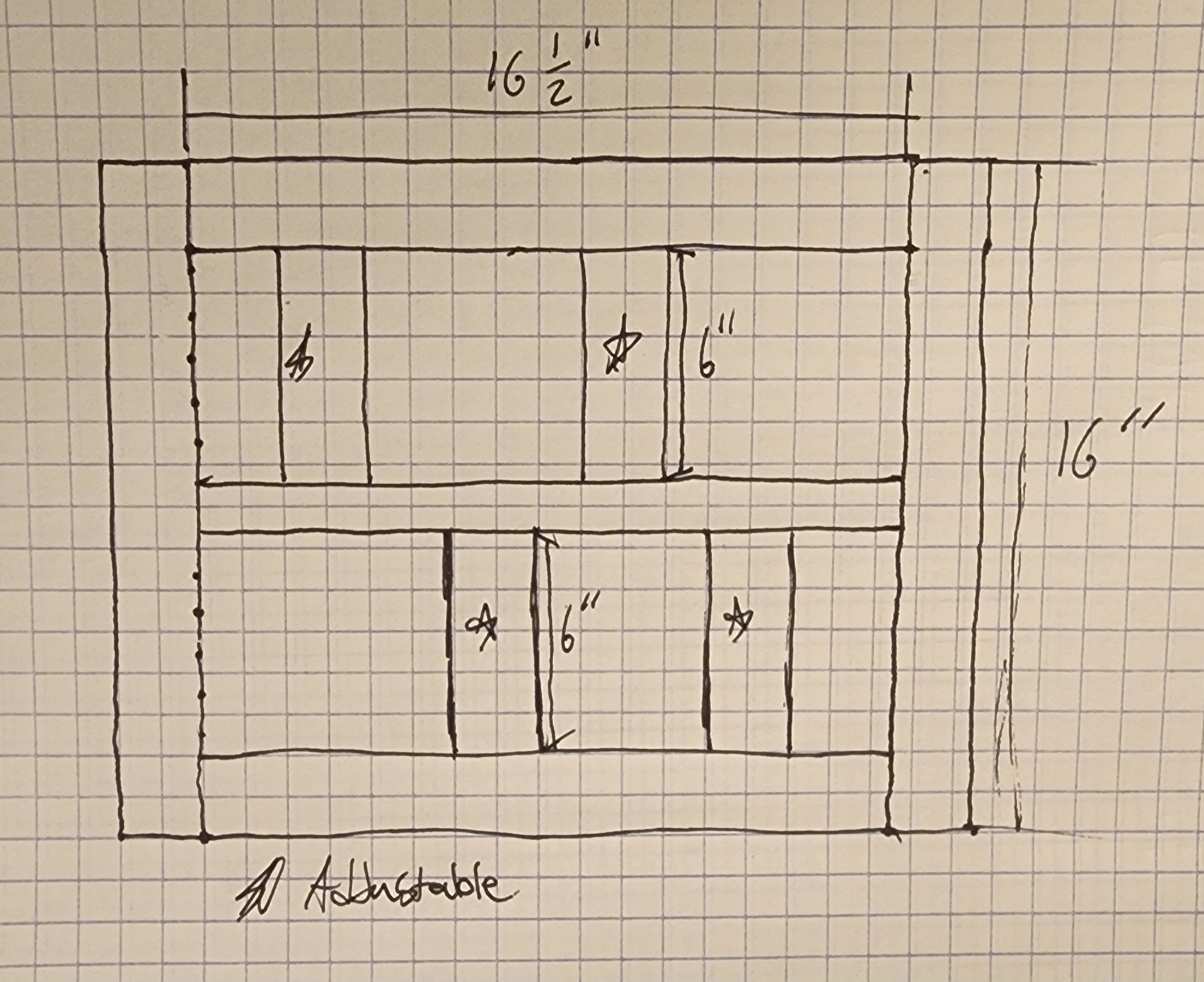
4/7/2024
This week a lot was done. First as a group we made our social media post, and did the rough draft of our report. Our group as wrap the barrel in nichrome wire. I personal worked on the barrel mounts included in pictures below.
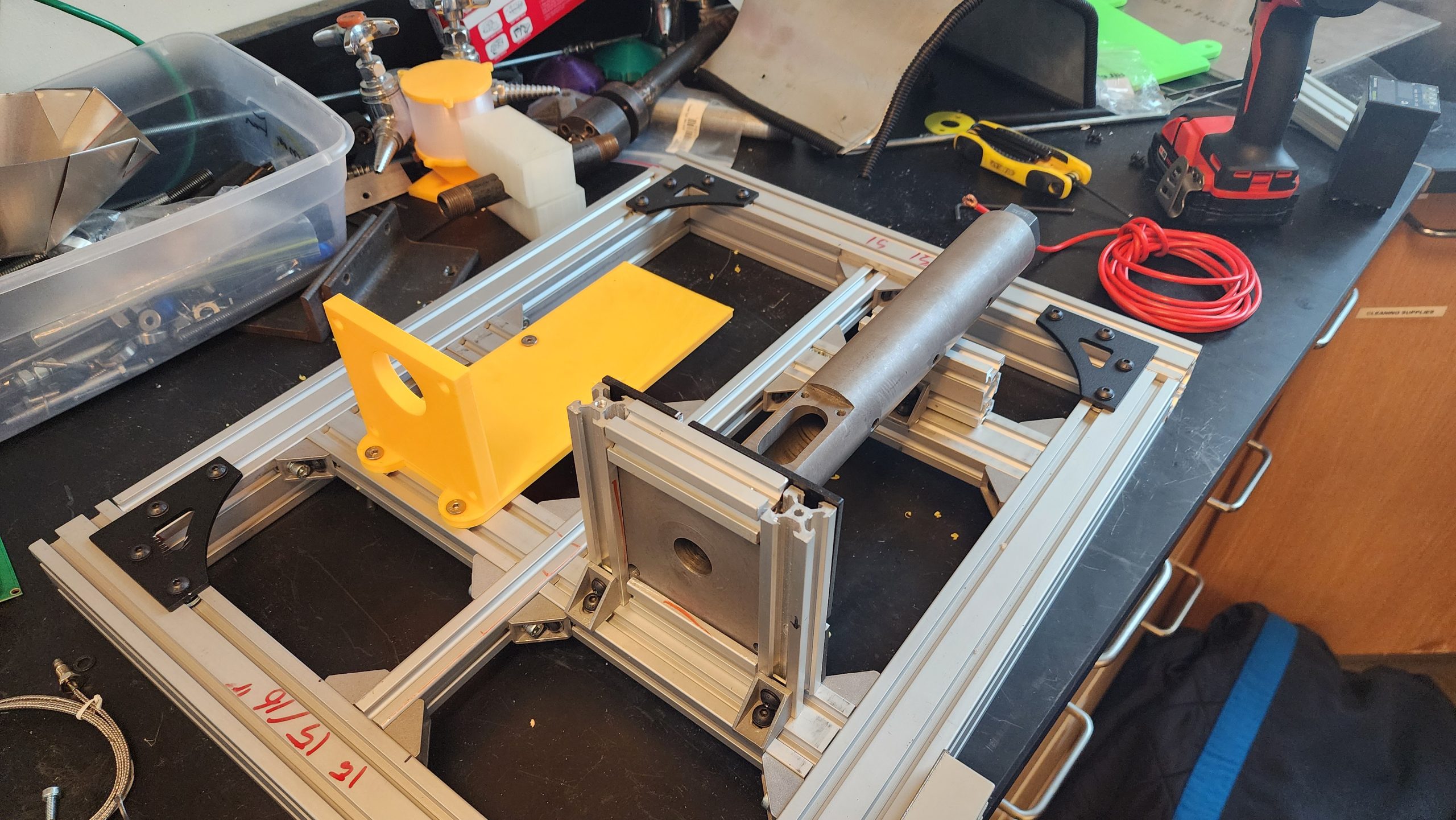
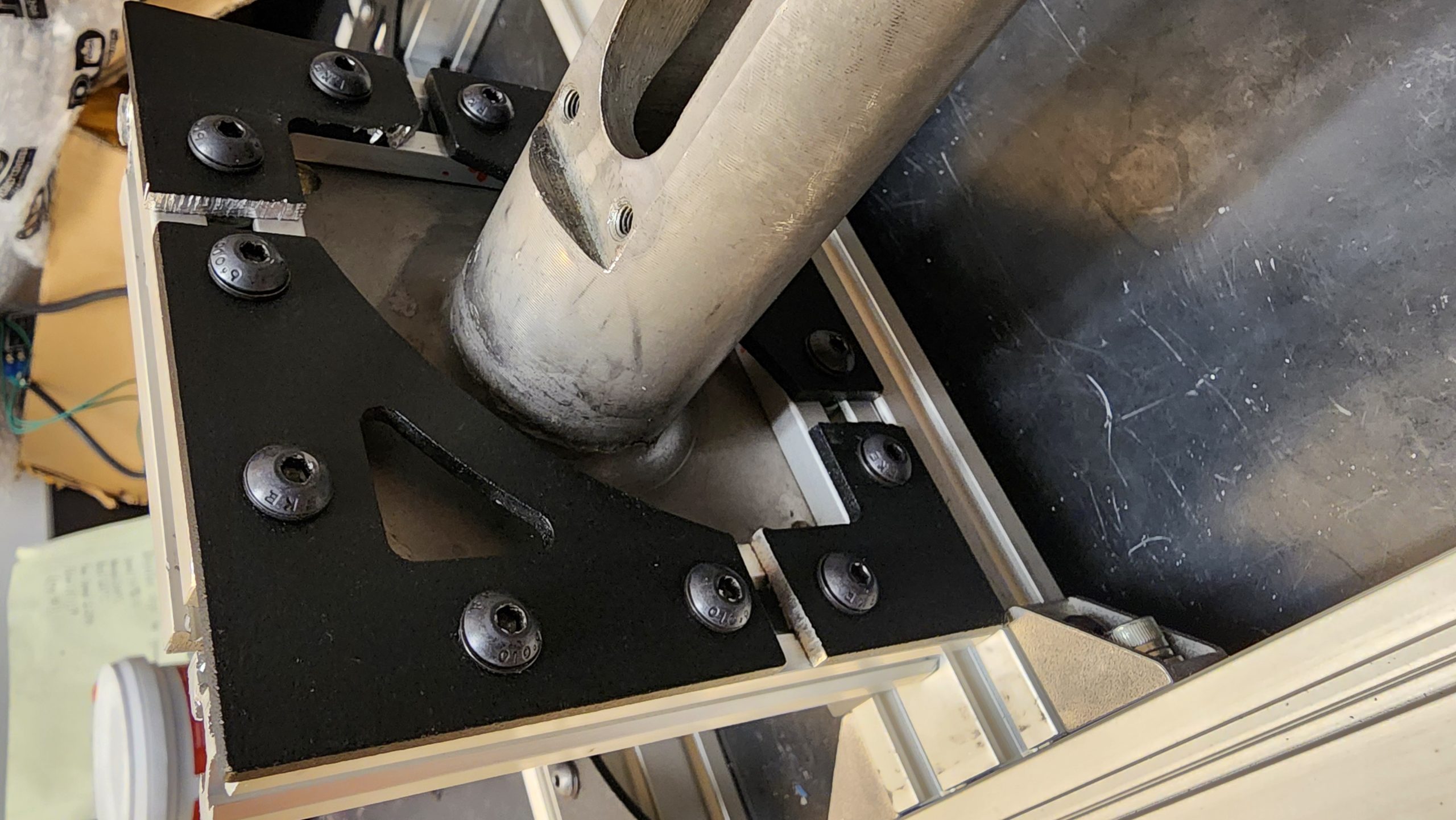
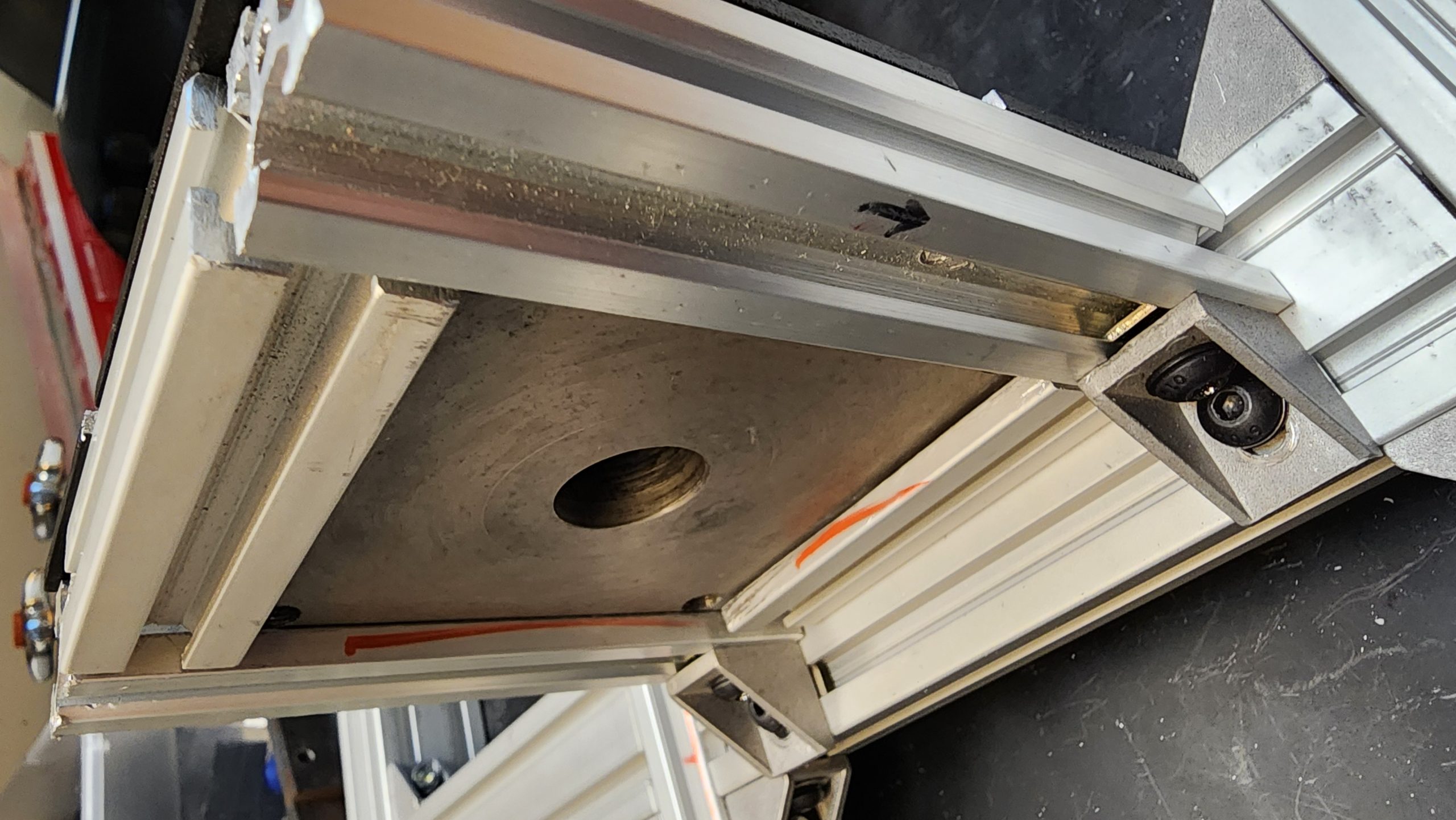
This involved first cutting 80/20 aluminum extrusion to size. Then expanding the gap between the slots. The all of the piece were slid onto the barrel and attach with the 2 L Brackets, and 2 L Brackets cut down to size. Then the areas around the mounting holes was mark and cut out with dremal / hacksaw / tin snips. Then it was placed onto the support mounts.
4/13/2024
This week has mostly been spent on preparing the slides for EMI and preparing the final report for this semester. I also work on the first iteration of the back plate to hold the screw in the extruder. I would consider this first attempt a failure with room to improve. The plate just has too much wiggle room. I think it might be salvageable, but a redesign might need to be done. The barrel was also wrapped with corresponding temperature zone this week.
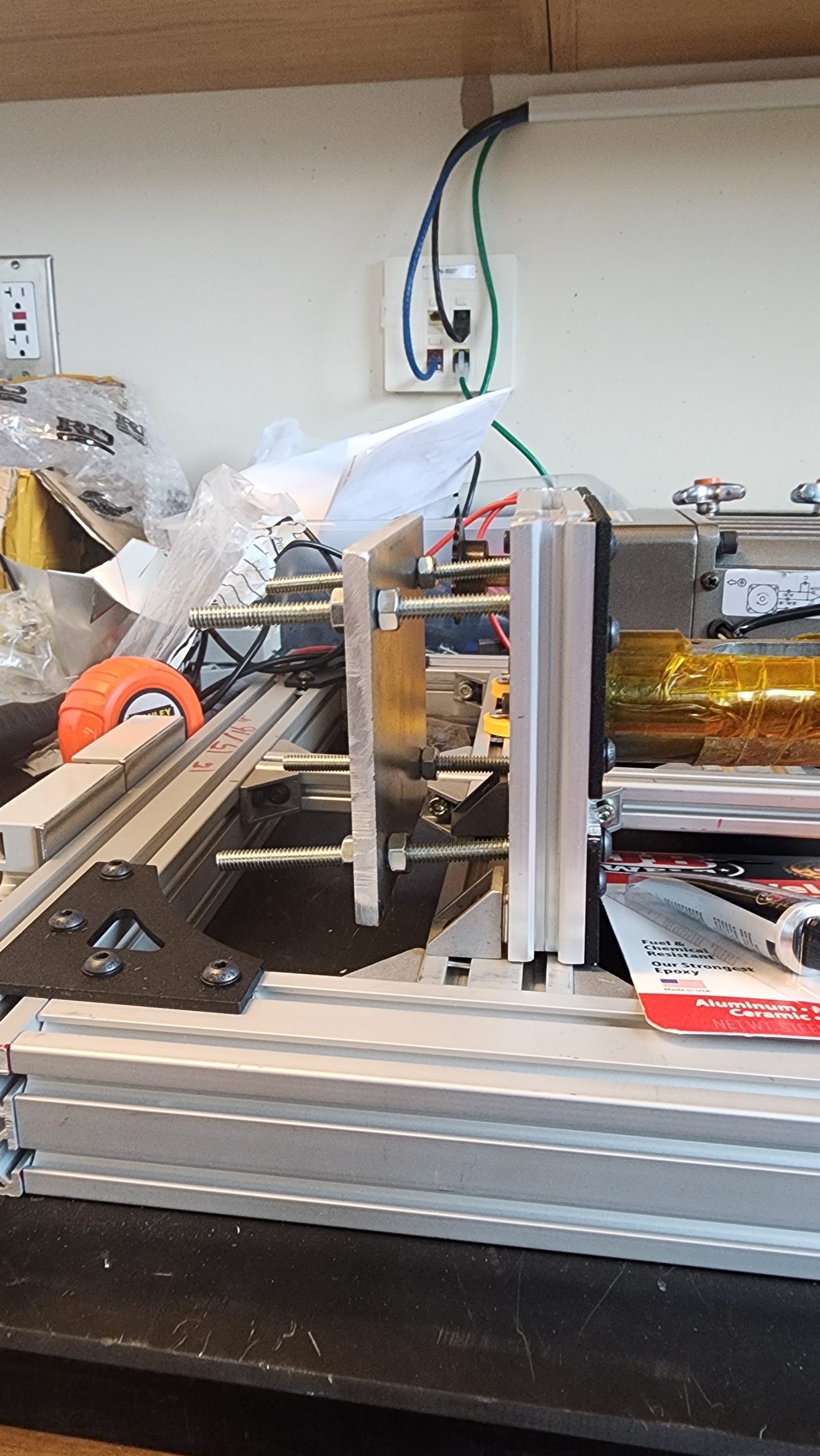
4/20/2024
This week was spent working on all the documentation for this year. We had our meeting with the EMI team as a year wrap up. The slides are located in the Recycle Bot drive. The rest of the time was spent working on the final report. The last thing for the year will be completing the final report. We look to come out to a fast start next year with a solid plan from the beginning.
9/13/2024
So far this year most of the work I have done is organizational stuff. I have been working on getting meetings together, talking to sponsors, writing presentations, and finalizing or project spec. We have also been working on designing the various units. The coming week we will be finalizing the designs of the unit, making a part list, ordering parts, and I will begin adding safety and screw backing on the unit. Below is a rough drawing of the design I plan to build to brace the screw in the barrel. It will be a plate of metal braced in aluminum extrusion to provide support. Then a thrust bearing will be placed in the center. When the screw is slide into it, the brace will lock the screw in that position in the barrel and the thrust barrel will allow it to spin freely on the plate.
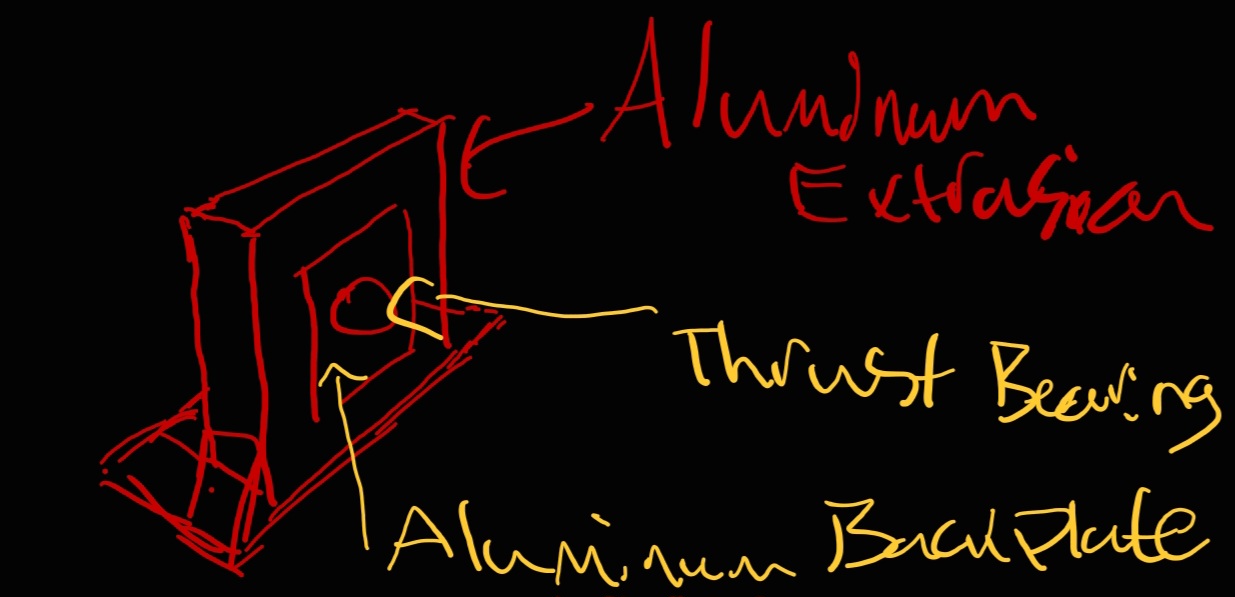
9/22/2024
This week I worked on organizing time to meet with our sponsors at GM, we will be taking them on a tour of the lab and project. I also worked on finalizing our parts list on looking into options for our new heating elements. In the coming week I plan to order parts, working with staff to get all of the aluminum extrusion cut, and building the brace plate for the extrusion. I will also be assisting the team with looking into a proper gauge system.
9/29/2024
This week I worked on adapted vacuum chamber, which expanded the size and added a heating element to the chamber.
Also, I printed the mounting brackets for the aluminum extrusion, and I built the frames for the cooling and rewind unit. In the coming week, we will be working on the electrical work for all of the units but mostly working on the CDR slides for our presentation Friday.
1/23/2024
Today, I mostly focused on running the extruder for an extended amount of time to look into long term use of the unit. There were some issues with overheated material in the barrel from other start up, and I forgot to try the resin prior to use so it had a very glass texture, but we were able to run for a significant time of about 1.5 hours without incident. Other task I will be working on for the week will be find an option to tension the chain with and looking into option for insulation the barrel.
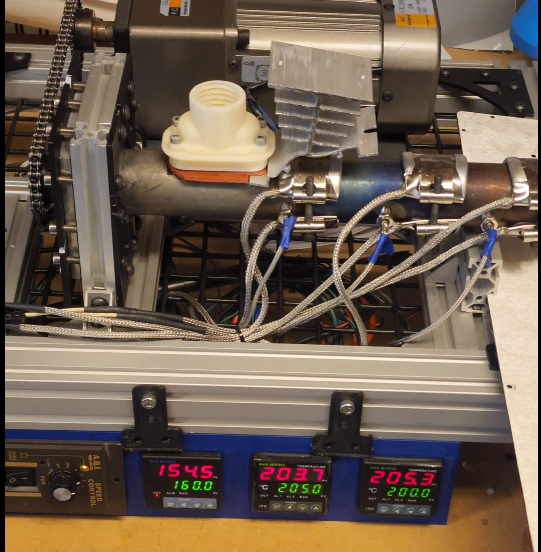
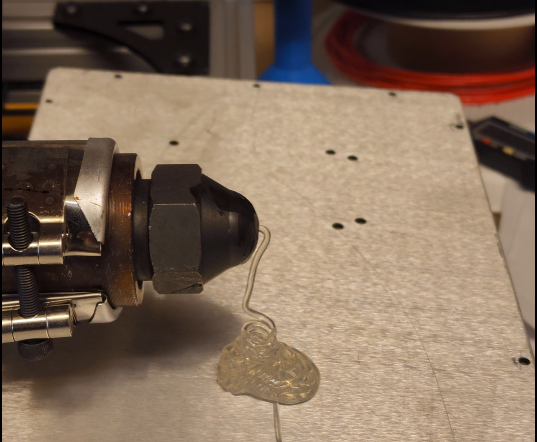
1/26/2025
This week I plan to work on the following,
-Insulation for the extruder
-Chain tension system for the extruder
-Work on meeting time with the sponsor
2/4/2025
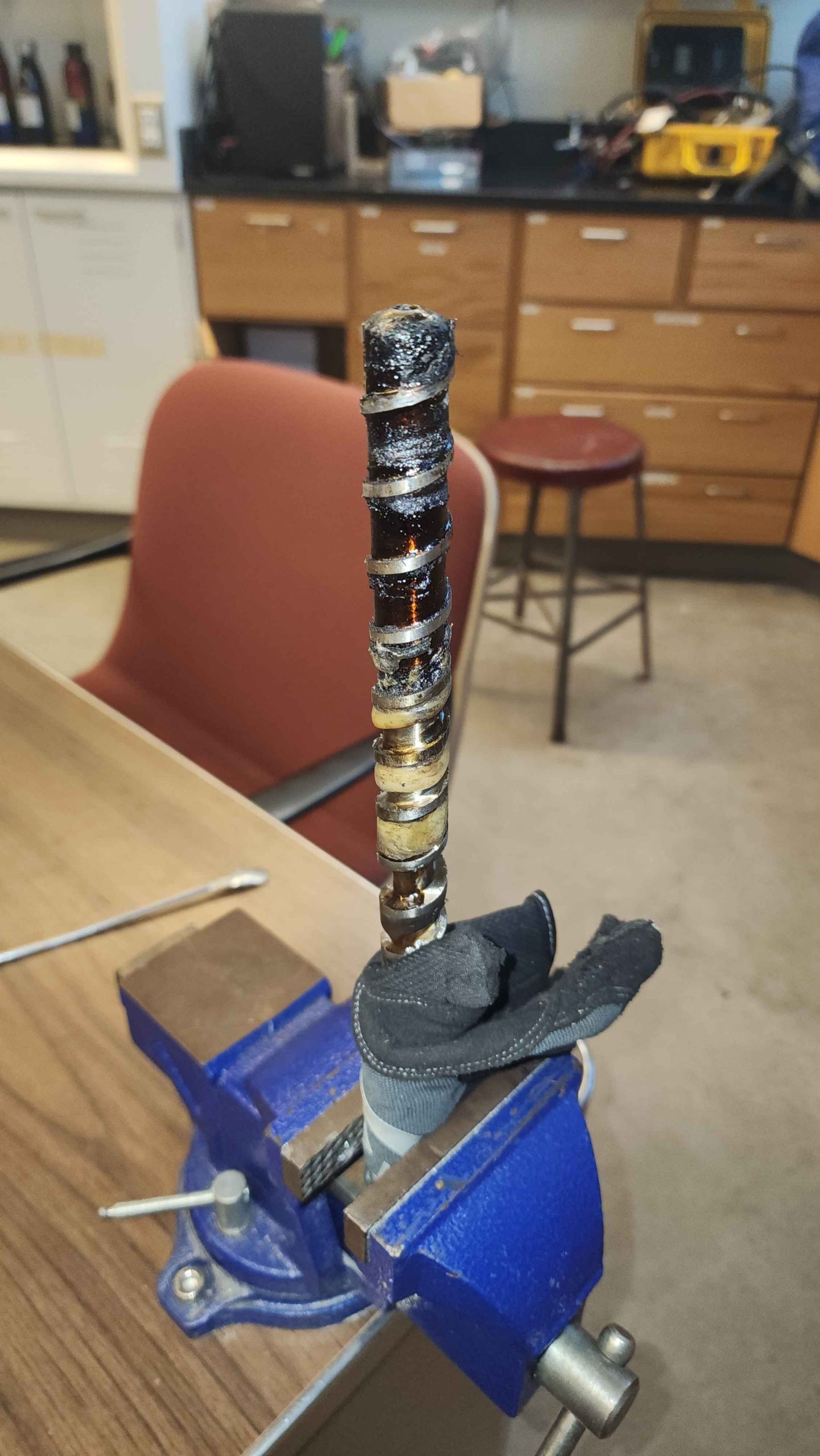
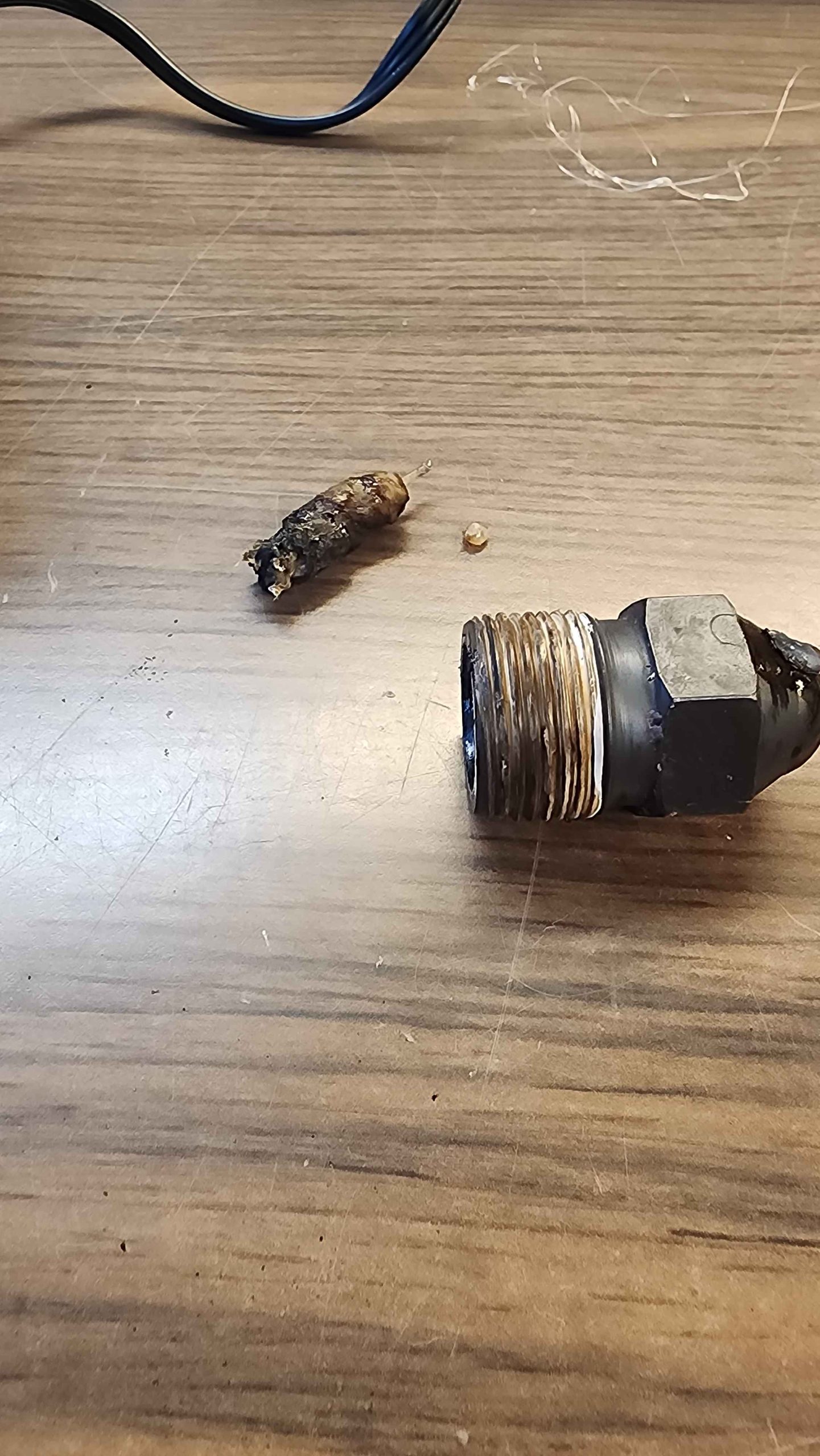
During this week’s run time, a grade of resin got stuck in and blocked the barrel. This prevented material from entering the system, pushing molten plastic up the feed of the unit, and burning the material down from the plug due to it speeding too much time getting heated. I was not able to accomplish my tasked outlined last week as most of my time this week was spent correction this action by dissembling the extrusion unit and cleaning all of the involved part. My plan for this week is to accomplish all of the stuff outlined last week.
2/16/2025
Most of this weeks’ time was spent preparing for CDR. I also worked to order insulation for the barrel and a new nozzle for extruder at a 2.5mm size rather than a 1.75mm size. This should improve our ability to hit the diameter set point. Next week will be a short week for me as I have travel towards the end of the week, but I will focus on preparing for the next items I order and also preparing for a meeting with the EMI team.
3/2/2025
Most of the following week will be spent catching up on work after the break. I will be working to implement a new nozzle and insulating on the extrusion barrel. These were ordered during the last break. I will also be checking on the unit for general wear and tear. I will also be working on organizing two presentations, one for OSHE and one for our sponsors at GM.
3/10/2025
Most of this week was spent preparing for the two presentations we had this week with OSHE and the sponsors. We have received the new nozzle, but the insulation has not arrived yet, so we are waiting on that before getting to work with it. It sounds like the electronics team is getting close, so testing may soon be coming up as the next couple of weeks come around.
3/17/2025
Progress has been made with the rewinding unit. Testing should begin over the next week. The insulation for the extrusion barrel has gotten more completed. It will now consist of three band to hold the section between the mica band heaters. These will have holes cut for the thermistors. Then the rest of the insulation will be used as a overwrap for the rest of the barrel. The chain tension previously mentioned may not need to add as the changes in the nozzle may account for that.
3/23/2025
This week was spent preforming the first test run of all the unit as a whole. It was mostly successful. We were able to make 400g of mildly on spec material. This is expected for this run as the control loop on the motor wind was not completed finished. During the following week we plan to continue testing and will include the control loop to try and match industrial specs better.
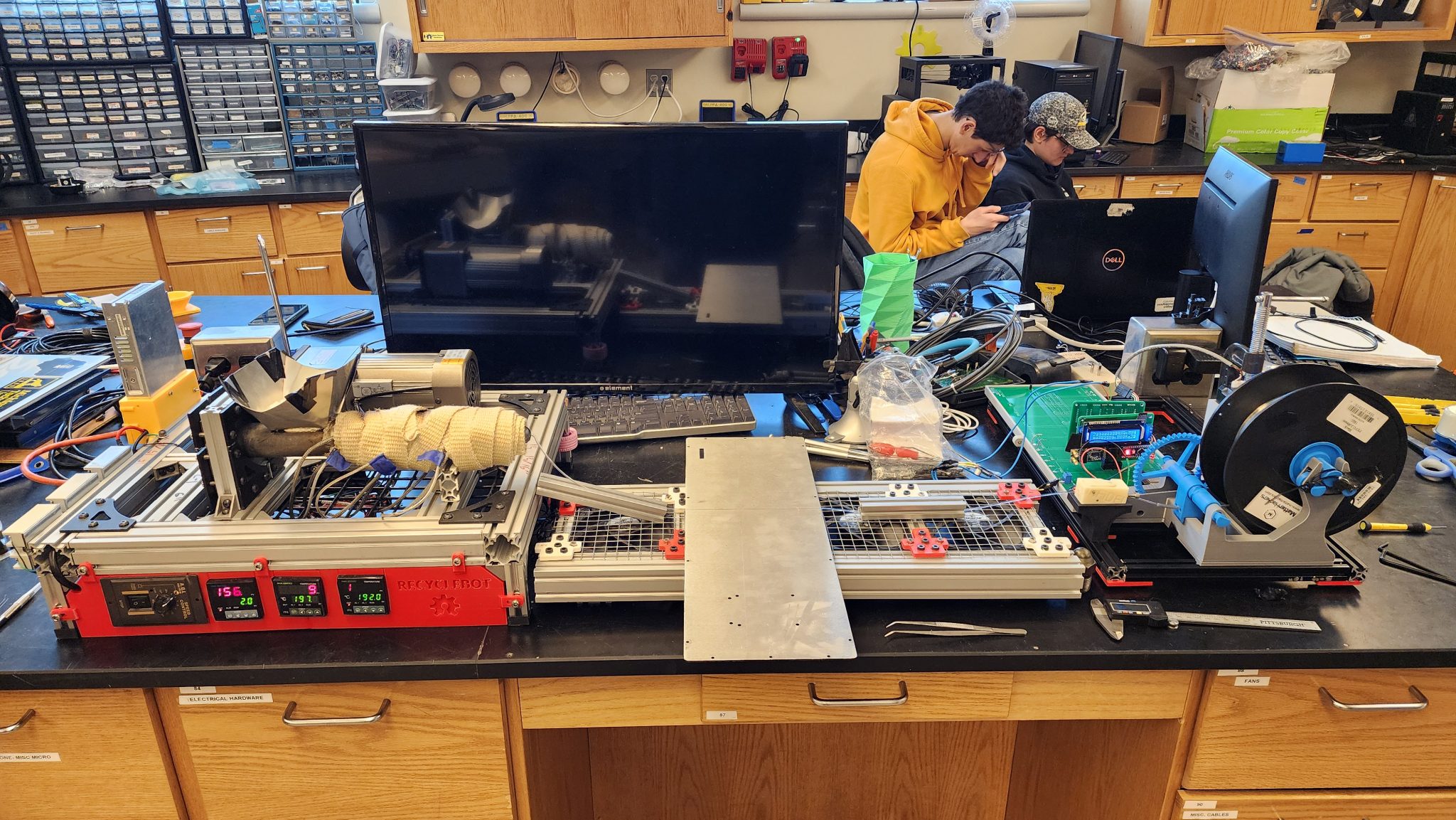
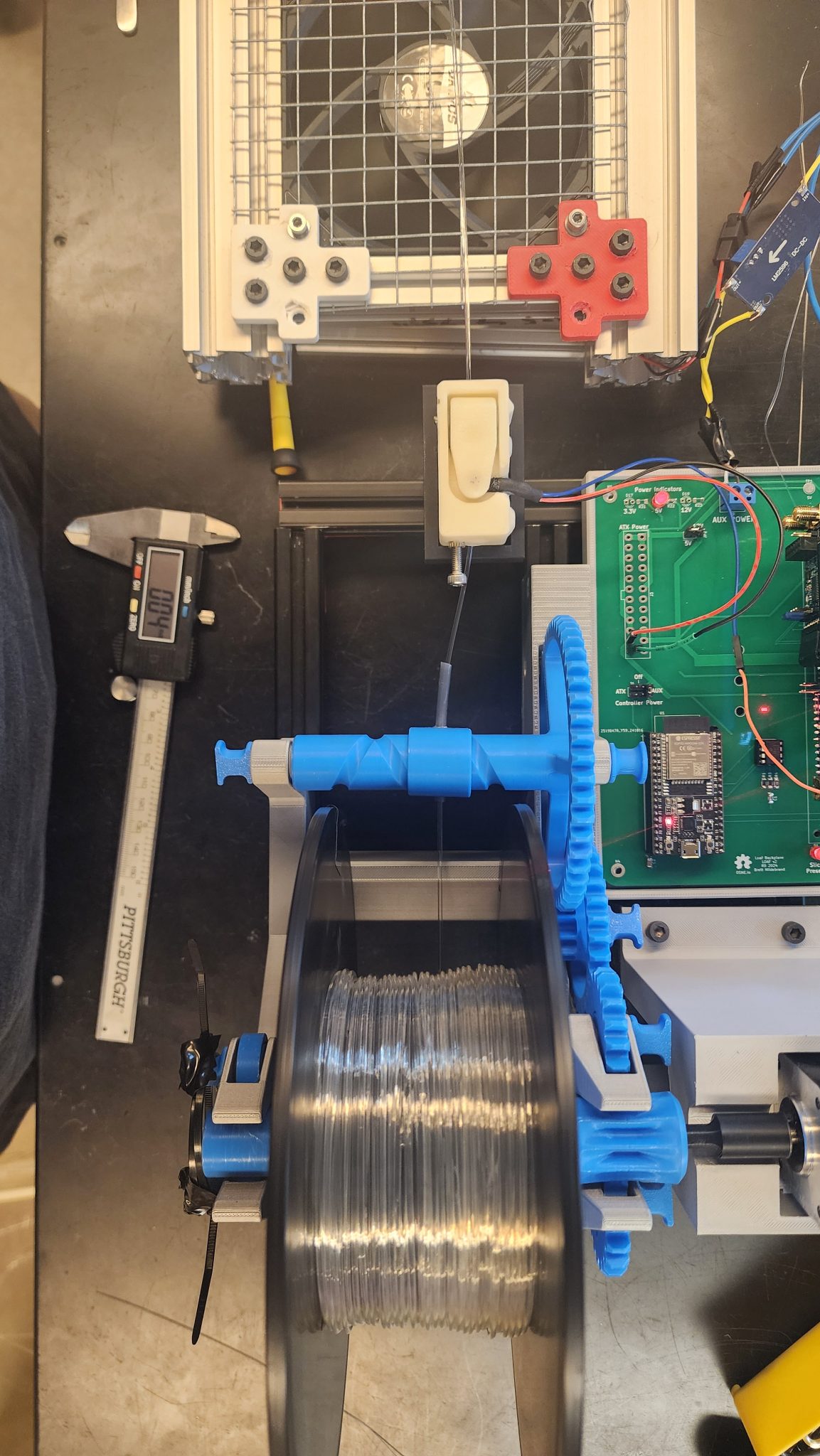
3/30/2025
The second attempt of running real filament was made this past weekend. Most of my time was spent running the actual extruder and trying to support the rewinder team. While a good effort was made, issue with the rewinders control unit prevent good consistent material. Team members will be reaching out for support to various people more knowledgeable in controls. Our check in day is Wednesday, so another attempt to produce filament will be done on that day or prior to it.
4/7/2025
Most of this week was spent preparing for design check in. Prior to that we started running the unit for another test. We were able to run at about a .15 mm tolerance for a while. Due to some electric issues, we had a failure of the motor that ran the rewinder and had to shut down. The rewinder team has made correction and are preparing for another run this Thursday.
4/13/025
This week I spent most of my time prepping for design expo. After design expo I will be working on the final report.