9/22/23 Update
This week I focused on getting an initial design done for the DAQ. I also began to work through some of the challenges with the design. Chief among them are protecting the system from the environment and communication protocols. These ideas were mostly distilled through weighing sensor options and how each sensor would effect the DAQ system. In the group setting I attend our weekly Monday morning meeting and assisted the group in the planning for the week. We also finalized our Project Specs, but after some post submittal considerations we may need to do another pass on that. On Thursday, I went out to see the mine with the group. It was fairly productive but unfortunately we are unable to enter the mine this week. We were able to get some useful information out of the trip, especially in regards to selecting the location for power generation. The trip also allowed for good ideation for the DAQ, cooling system, control system, and power generation. We will document these ideas in our next Monday meeting I believe. A meeting with Shane has also been scheduled for next week Wednesday. Below I have attached the Monday Meeting notes and individual documentation of the DAQ for this week.
10/7/23 Update
These past two weeks I have been focusing on building the initial design and ideas for the DAQ system into a prototype design. I worked through the design of the digital system and ended up selecting CAN for our communication protocol. I also laid out the design of the CAN commination boards for the sensors. We selected the Pi Zero as the micro we would like to run the whole system off of and figured out the items that would be needed to support this decision. I went then and made selections for the power system needed to run the DAQ. I wrapped all of this up together and placed an order for all the necessary components needed for an initial DAQ prototype. Coming in the next two weeks I need to order a few supplementary parts (wire and I think I might switch our buck converter for the Pi to a more integrated solution), work on our CDR presentation, and begin the prototyping. I hope to have a working prototype by the end of October. I do need to to put more work into understanding the low power mode and how we want to execute that. I may need to purchase some sort of timing ASIC. I also don’t entirely understand the CAN transceiver’s wake-up on CAN which we might use instead of a full on shutdown.
10/28/23 Update
Parts are in for the DAQ. Ben is working on breakout boards currently and after that a prototype is going to put together. Big questions still, are flashing the microcontroller and getting the Pi programmed. Wire to be used should be ordered on Wednesday. While waiting on that, I have been working on the Power DAQ for solar panels. I have an initial design layout, but I’m still not confident on the solar panel specs so I have not specced out parts. Thomas appears to be having some issues on that front. Hopefully, on Monday we can clear the air on that and get parts ordered. I also have been coordinating with the local Professional Surveyors Society to get their assistance on getting a point cloud of the mine. Hopefully, we can plan our trip out to the mine soon. They would like a date for that trip by Wednesday, so another thing for us to focus up on this coming Monday. We may need to split up our trip into two trips.
11/3/23 Update
Slow week on progress in some regards. Sounds like Thomas has gotten his hands on the solar panels but they are much smaller than expected (25W). Makes me worried about whether or not there will be enough power to run the Power DAQ off of the solar panels and still have a measurable power leftover. Not sure Ben is at with the breakout boards but it sounds like he has had some struggles with that. My plan moving forward is to see what the group thinks about Power DAQ at our Monday morning meeting. We will hopefully be putting our solar panels next Thursday and also be taking point cloud data of the mine. The Power DAQs will most likely have to be set out on a different date, which is fine. The solar panels need to go up soon because the road will become snowmobiles only once the snow stacks up and they will be too big to get out there. Focusing on getting everything ready for Thursday will be my goal for next week. Power DAQ is secondary and the normal DAQ will be last priority.
1/26/24 Update
This week I focused on working on the SD card issue with the power DAQ. I did some research into the issue and it seems to be a two part issue with both the hardware and the software. To fix the hardware I need to identify the pin readouts whether or not the SD card is present and wire that to the Arduino. For the software it sounds like AdaFruit did some fixing of the SD library to include an SD.end() command which can be implemented to properly disengage and then re-establish communication with the SD card. If this does not work I need to find a work around using a RTC pretty quickly. The power DAQ needs to be done by the end of the week. I also need to order more microSD cards and need to register for Design Expo. I also made a diagram of what the Environment DAQ schematic should look like. Depending on Thomas’s success on getting a programmer for it and Mitch’s success on assembling it, we could be looking at starting the prototype of that this week. I have attached the schematic below.
2/3/24 Update
This week I focused on finishing the power DAQ, notching 35 hours of enterprise work, and getting it deployed by our 2/4/24 deadline. I got the SD card issue fixed and solved a lot of grounding issues that were occurring with the voltage and current measurements. I also tested and debugged the final prototype and finalized the code. I then drew up the schematic for the power DAQ and began the manufacturing and box layout. We mostly built the boards out on perf board. We only had multistranded wires and not solid core which made the whole ordeal a little messier then preferred. I made a design for the cover of the boxes when I had a moment in there too. We unfortunately missed our deadline despite my best efforts and I was only able to get one box fully done and I have the second to about the halfway point. A tough end to tough week. I have attached some pictures of the week below.
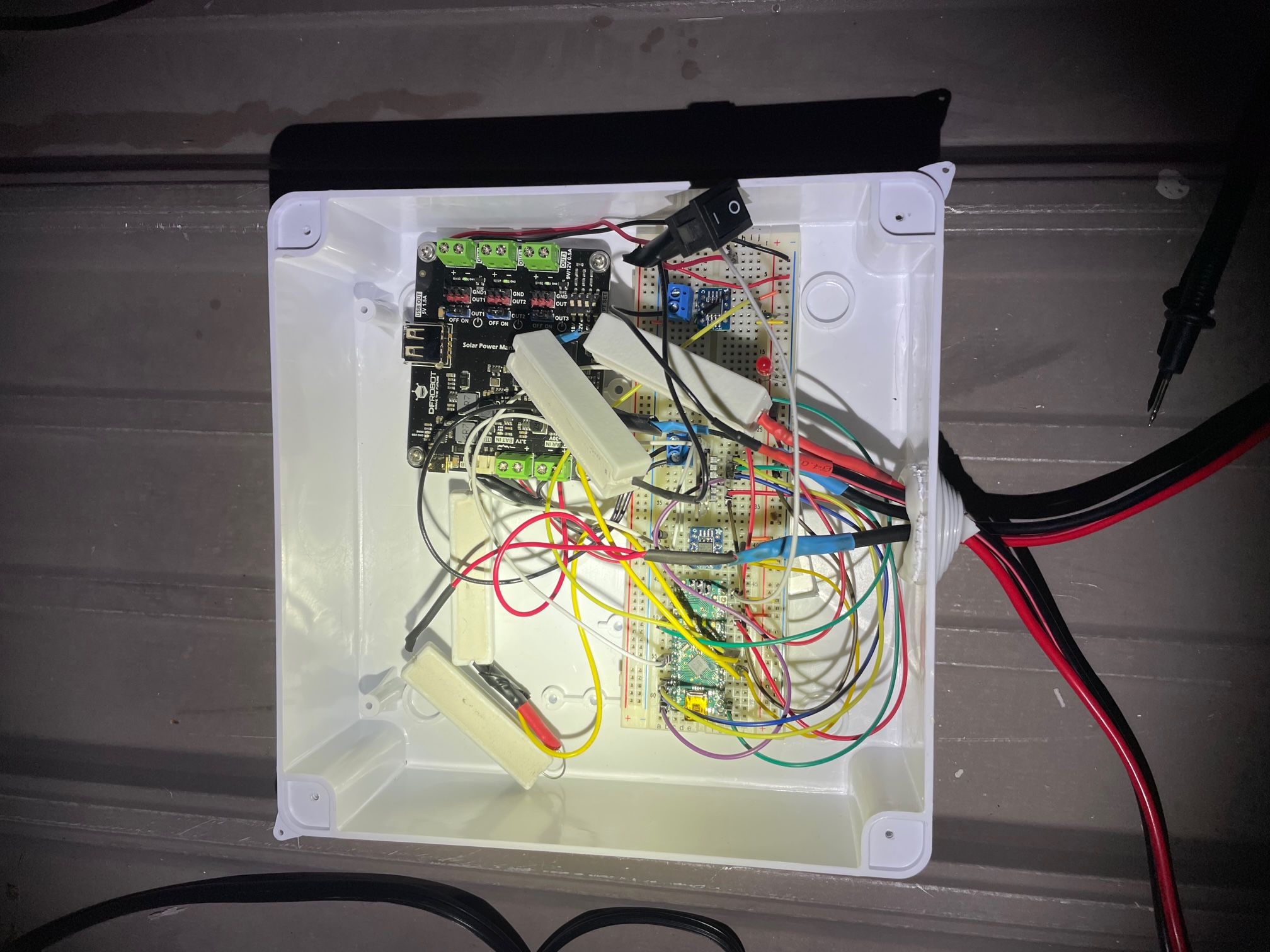
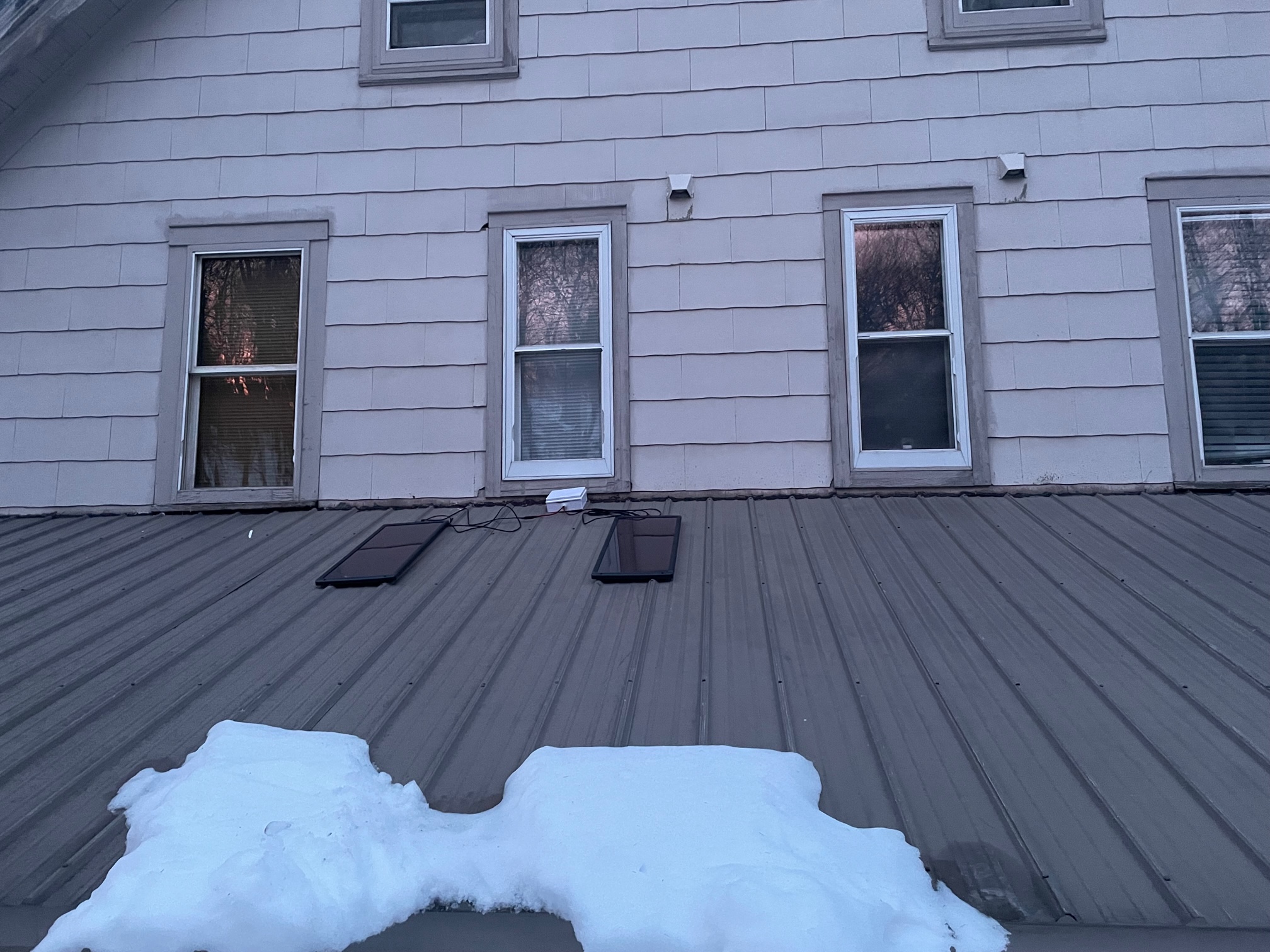
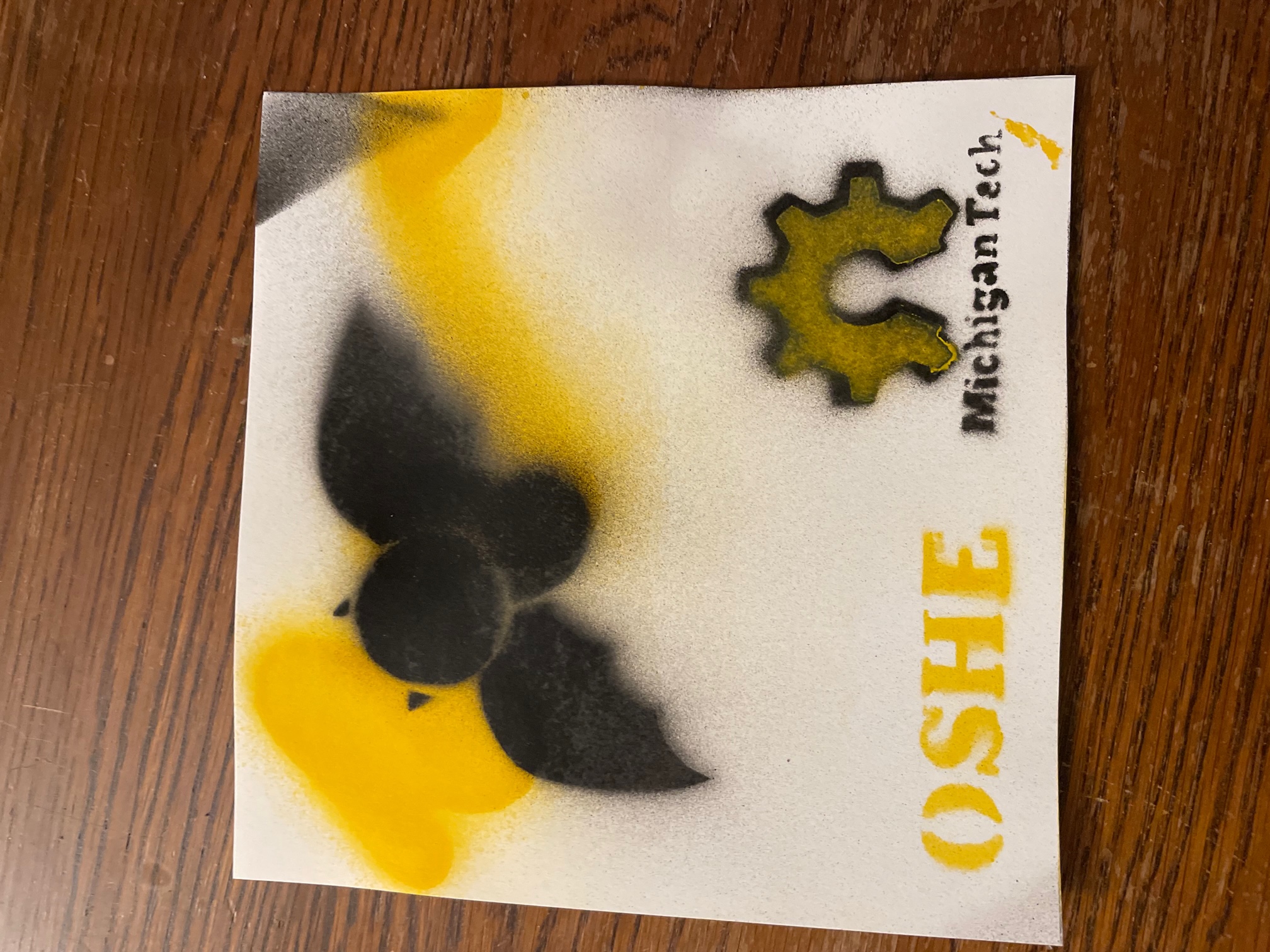
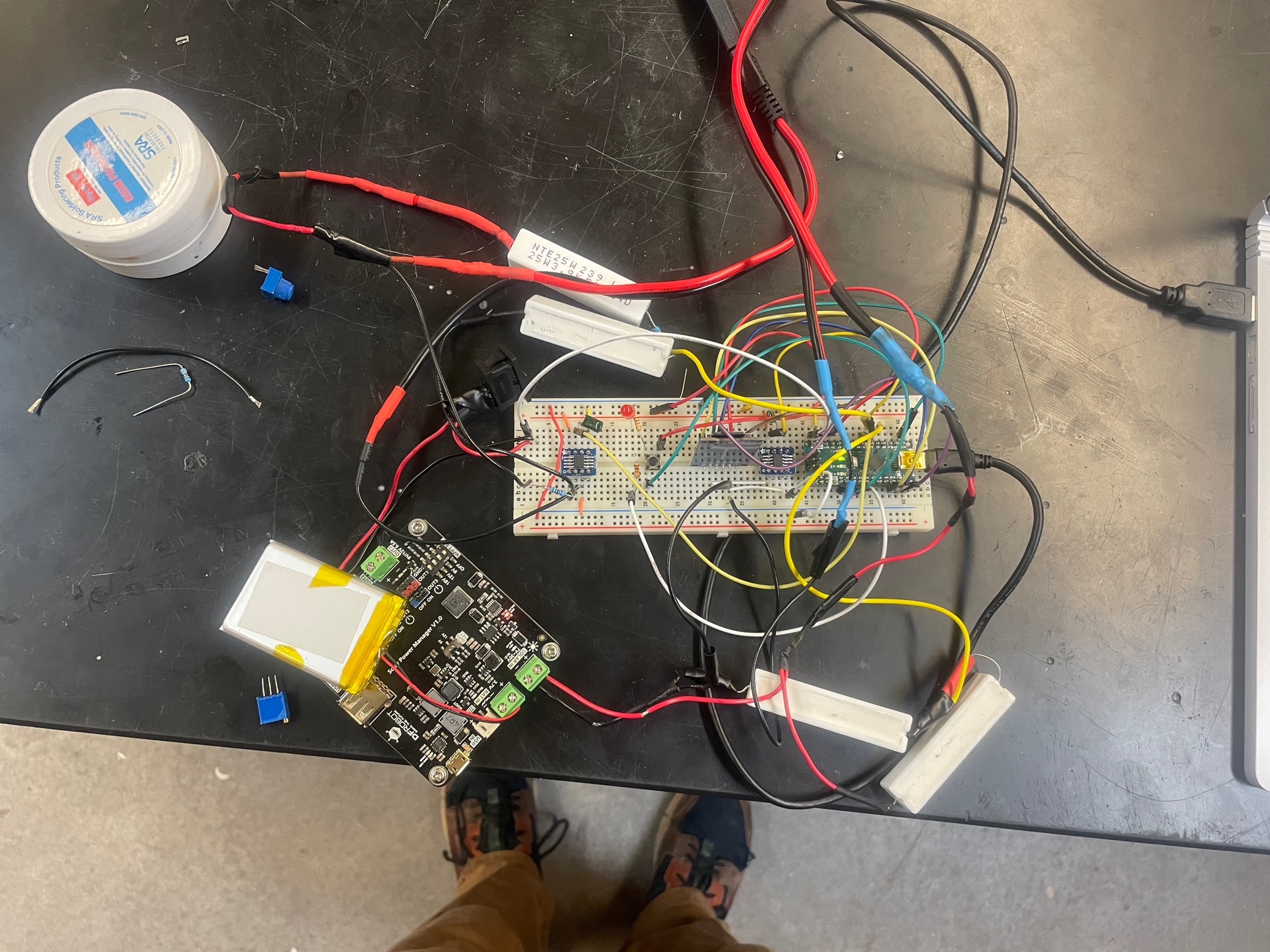
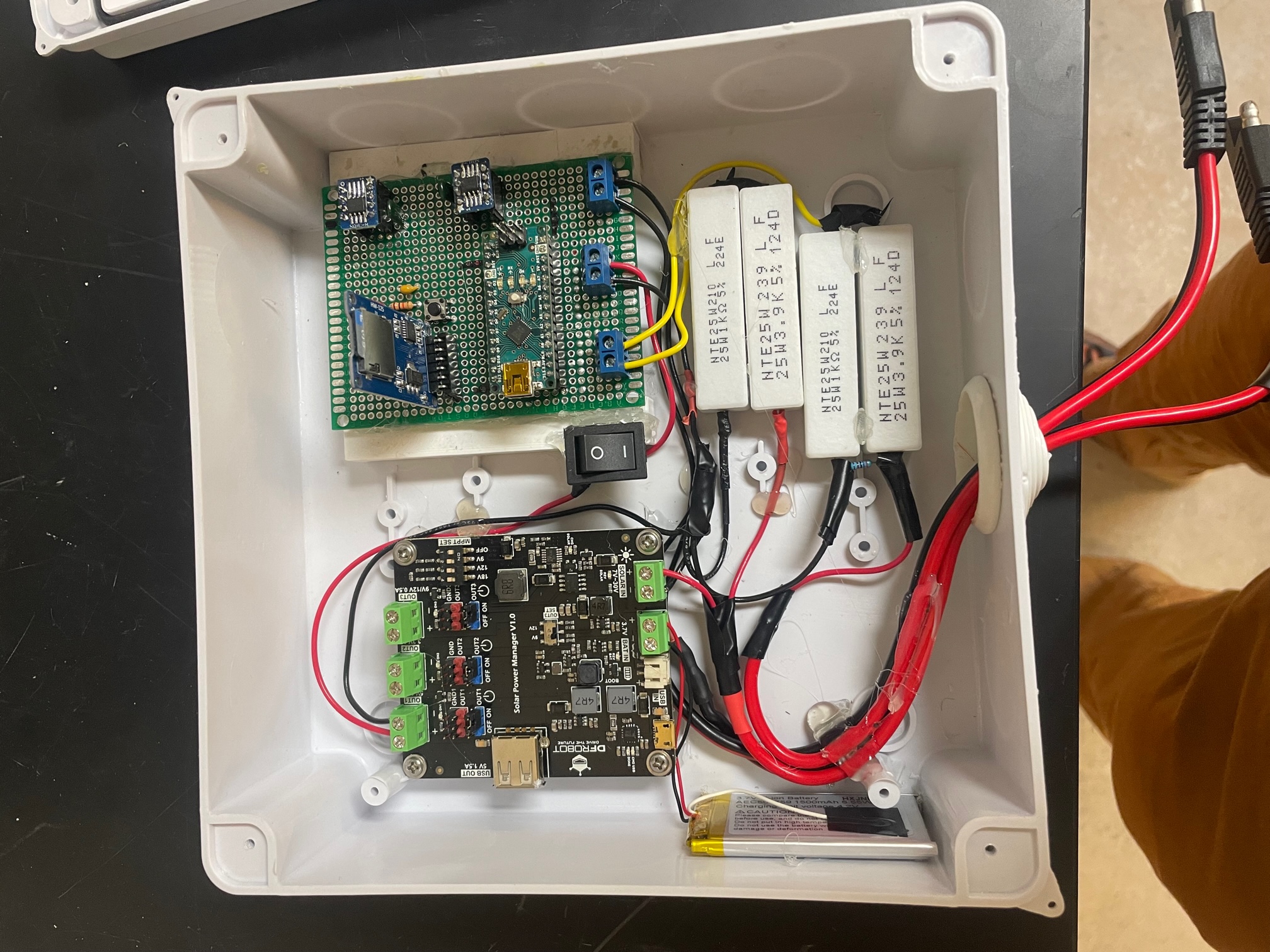
2/9/24 Update
Started to work towards midsemester goals. Trying to coordinate make up work to meet our missed deadline from last week, while keeping an eye on the road ahead. We have the environmental DAQ prototype started and it sounds like we have the KiCad files started for it as well. Would love to get a practice board laid up from the campus mill. I would like to have the prototype working and order prefab boards before break. We also have the CDR coming up and keeping our thumb on that is also in the back of my head. Next week I hoping to work on the prototype for the environmental DAQ, test out the STM programmer we just ordered, and get the our test PCB manufactured. If the KiCad files aren’t completed yet, I will hopefully get to look at those this weekend.
2/16/24 Update
This week I spent time on doing the KiCad for environmental DAQ and sourcing parts for that (considering specs, packaging, etc.). I also looked at some small redesigns for more accurate measurements and for better user experience. I think we should run the I2C through a DAQ because I am nervous about using the boot pins as doubles for that and I think we should use a constant current source with RTD because I don’t think we will be able to generate an accurate enough reading using a voltage divider. Unfortunately, this may all be moot, because the DNR and CFRES were thinking we should be headed in a different direction. At the moment this puts the whole project up in the air and we are waiting to see if we need a drastic change in scope to meet their needs. This is not the greatest time with the CDR less than a week away and with graduation at about 9 weeks out, so everyone’s a little on edge with this whole project. Our timeline was tight already and now with delay and potential scope change/scope creep we could be in for a ride on the back half of the semester. With the general slowness of communication from the DNR and CFRES, I also worry about when this will be ironed out and how long we will be in no mans land. If we need to change directions, we need to pivot ASAP and rework our spec sheet preferably before the CDR. If we are not and we just need to encompass their new goals (they want a lot of emphasis on the cooling system, the control system for the cooling system, and power specs. This is opposite of what we thought was communicated to us last time we talked to them), we need everyday we can get to accomplish this plethora of goals before the end of the semester. I attached an image of the schematic I made this week (even though it may just be a pointless relic in the future).
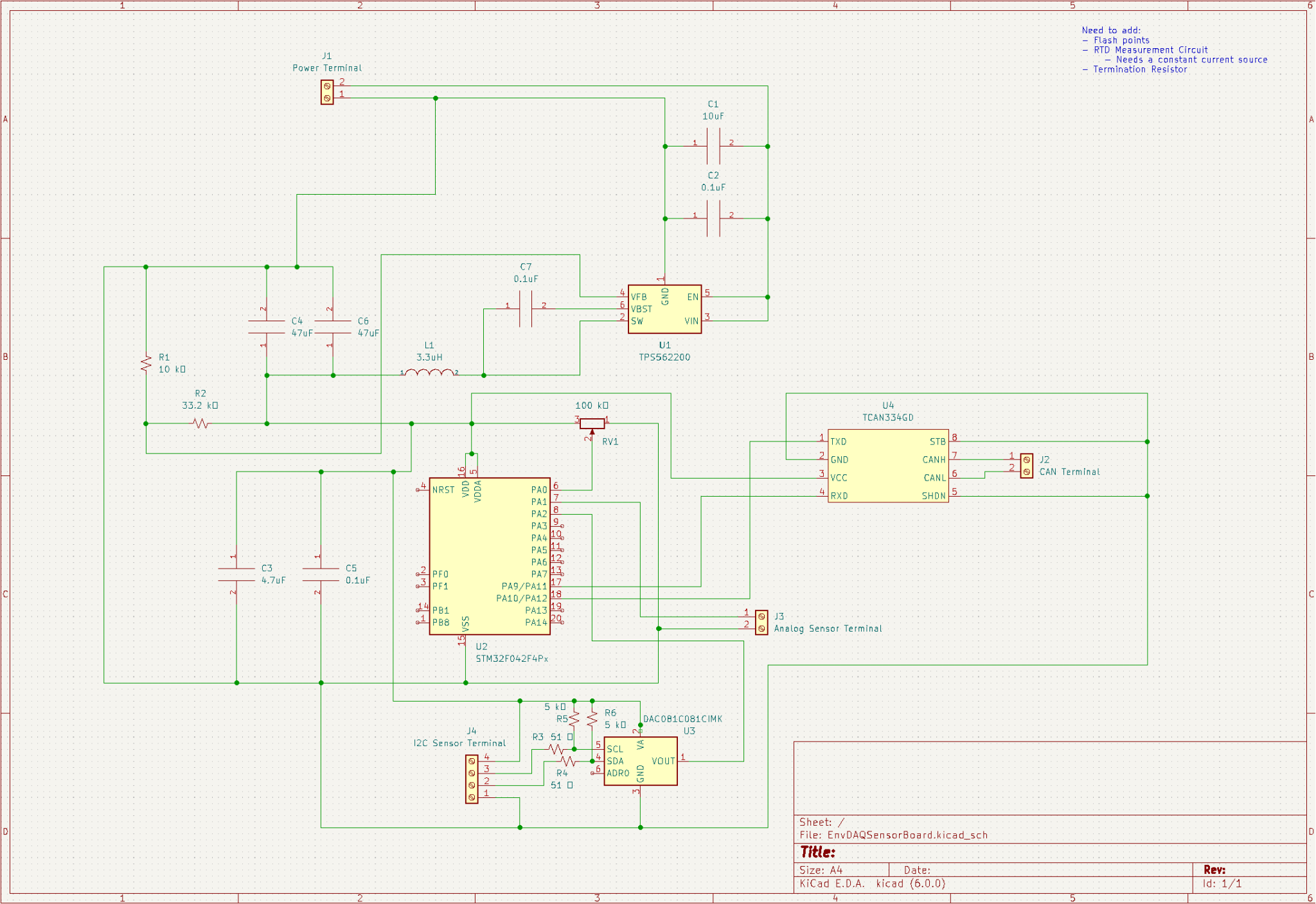
2/24/23 Update
This week was CDR week so I spent some time putting together the presentation for that and gave feedback to other groups. The biggest feedback we got from this was that our point of contact for this project has changed to a PhD candidate. We contacted him and honestly he seems to have much context for this project as we do. We’ll see if the communication in this project improves or if it continues to be the main issue of this project. In other news, we decided to just keep the environmental DAQ rolling and use it for temperature feedback in our control loop. The humidity aspect of it we are dropping completely which simplifies some things. To finalize the schematic I need Thomas to let me know which pins are needed for programming and for Ben to finish his RTD temperature test. I also need to experiment with the constant current source to properly size the current set resistor based off the bias current which I think is based on the voltage level. This will also determine whether or not current limiting resistors are needed on microcontroller inputs. I have attached images below. Not sure if the board file is perfect, might be some layout issues that I am not familiar with. Also used vias for the first time and not sure I did that in a perfect way.
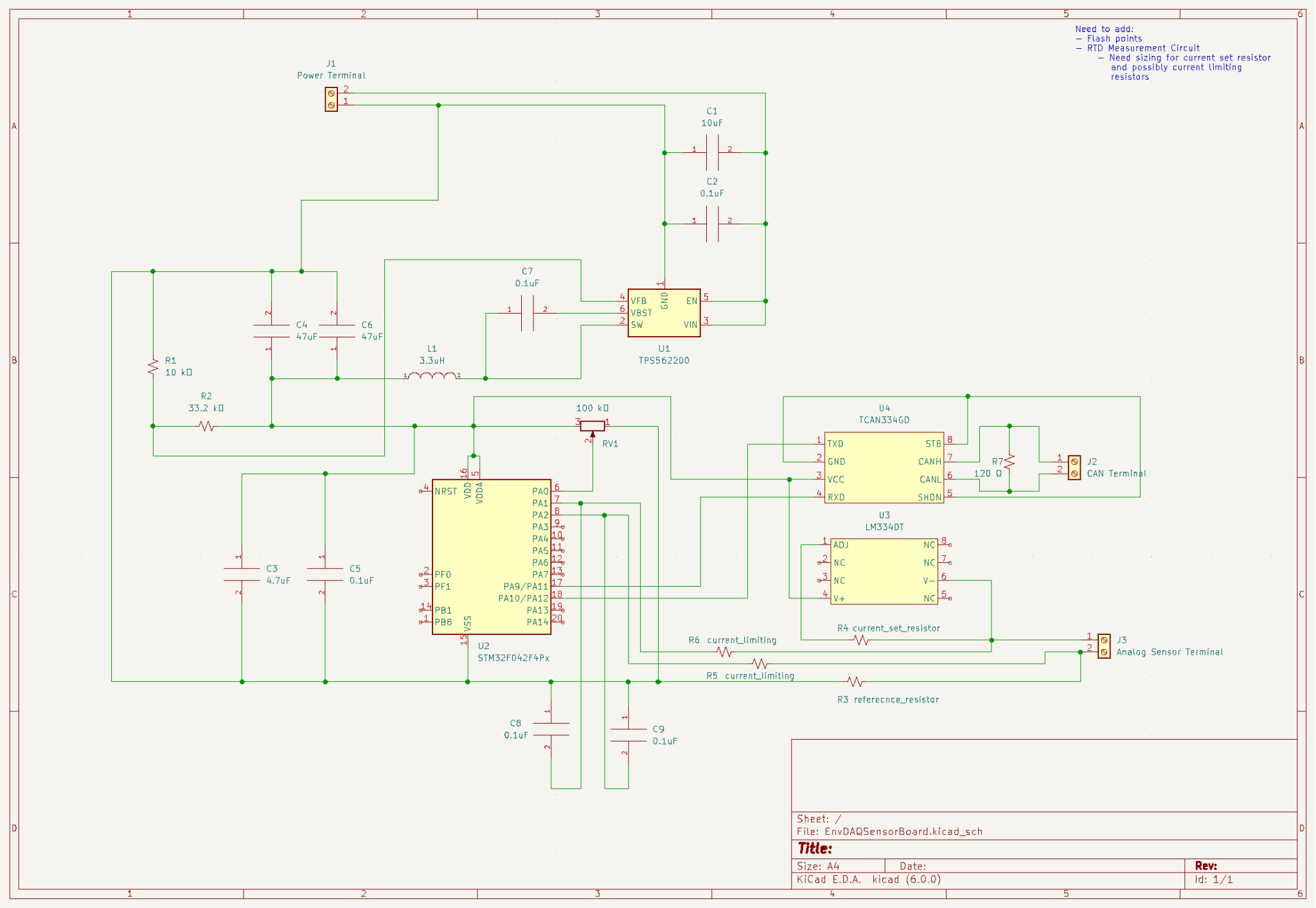
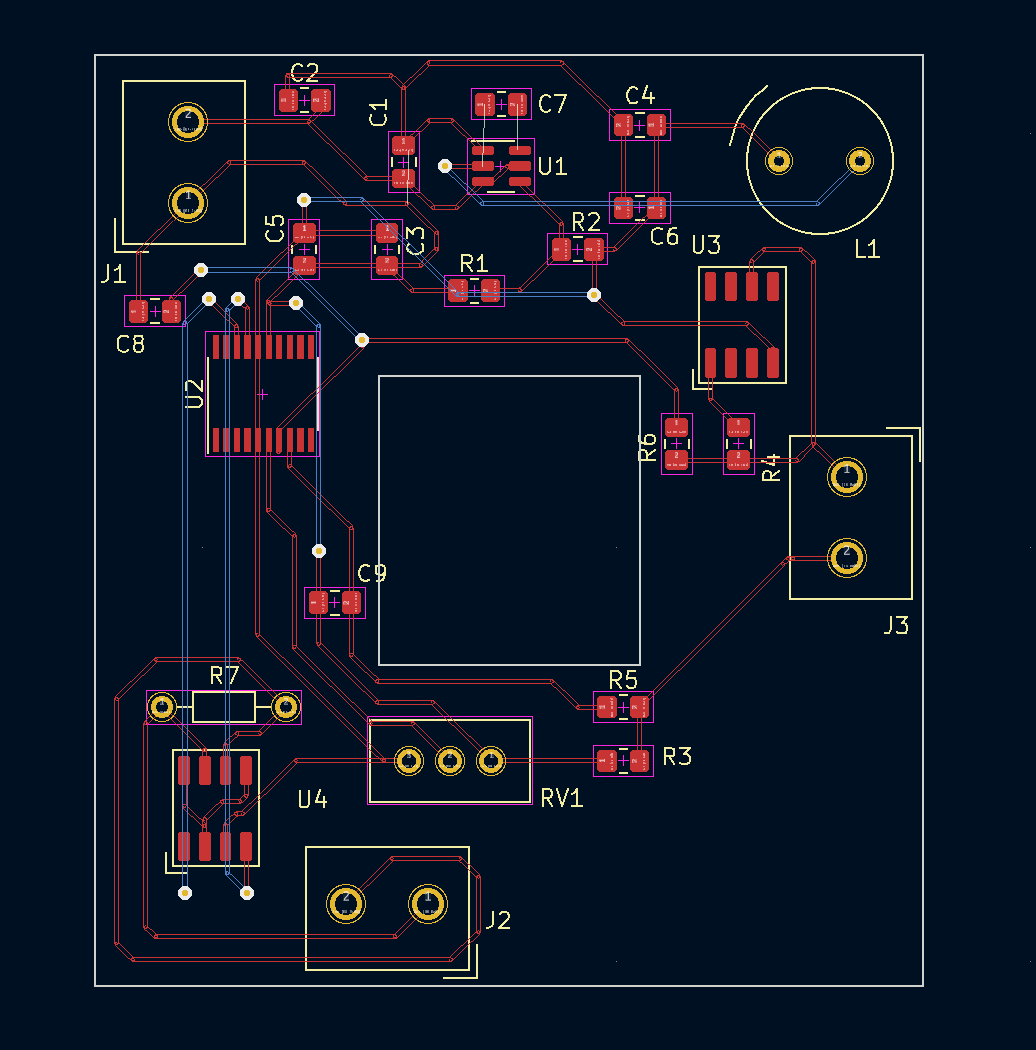
3/9/24 Update
This week I worked with Mitch to get the prototype Env DAQ working on a hardware level. We did not have much success with the IC Buck converter so I think the best bet is to take a different angle with it and look for a new part. I also got the constant current source working and have the entirety of the temperature sensing circuit working. Got some feedback on the the current board layout and I think I may switch it up a bit. I think we should have a few components on the back side of the board for better fit. I think I might switch the screw terminals out and just put in solder pads or ring terminals. Still waiting on Thomas for his programming pins and his hopeful success on that front. We really need to order this board and the timeline is not looking great.
3/16/24 Update
This week I redid the power stage of the Env DAQ to use a new, more integrated buck converter which will hopefully function better. I think I did an okay job of this but part of me thinks I could of done filter selection a bit better. I went off of the spec sheet so I think overall it will workout fine, but it might be smart to make sure the frequencies being blocked are the frequencies we are expecting to experience. Also I didn’t really consider ESR in any of this, which for our application should be a mostly trivial issue. I based along max current draw based on buck converter relationships to Ben for wire sizing. Thomas got his programming pins to me so I added them into the schematic also. I also changed some the trace width sizes for the power connections. With this I finalize the schematic and board files, I did a PCB review with the Electrical Lead. That all came back peachy, so I ordered the boards and most of the parts this week. I have attached the final schematic and board layout below. I need to order the Dwyer sensors and get wire on order from Ben on Monday. I also talked to Tanner with Ben this week and got a little more perspective on his vision and needs. Mainly discussed what he wanted from the User interface and let him know where we expected to get by the end of the semester. Next week, I hope to finalize the UI with Mitch and start the programming for that. Hopefully, Thomas can finish up his programming and we can test a section sending CAN messages back to the Pi. Ben also set up a meeting with Bay Electric so I plan to attend that on Wednesday.
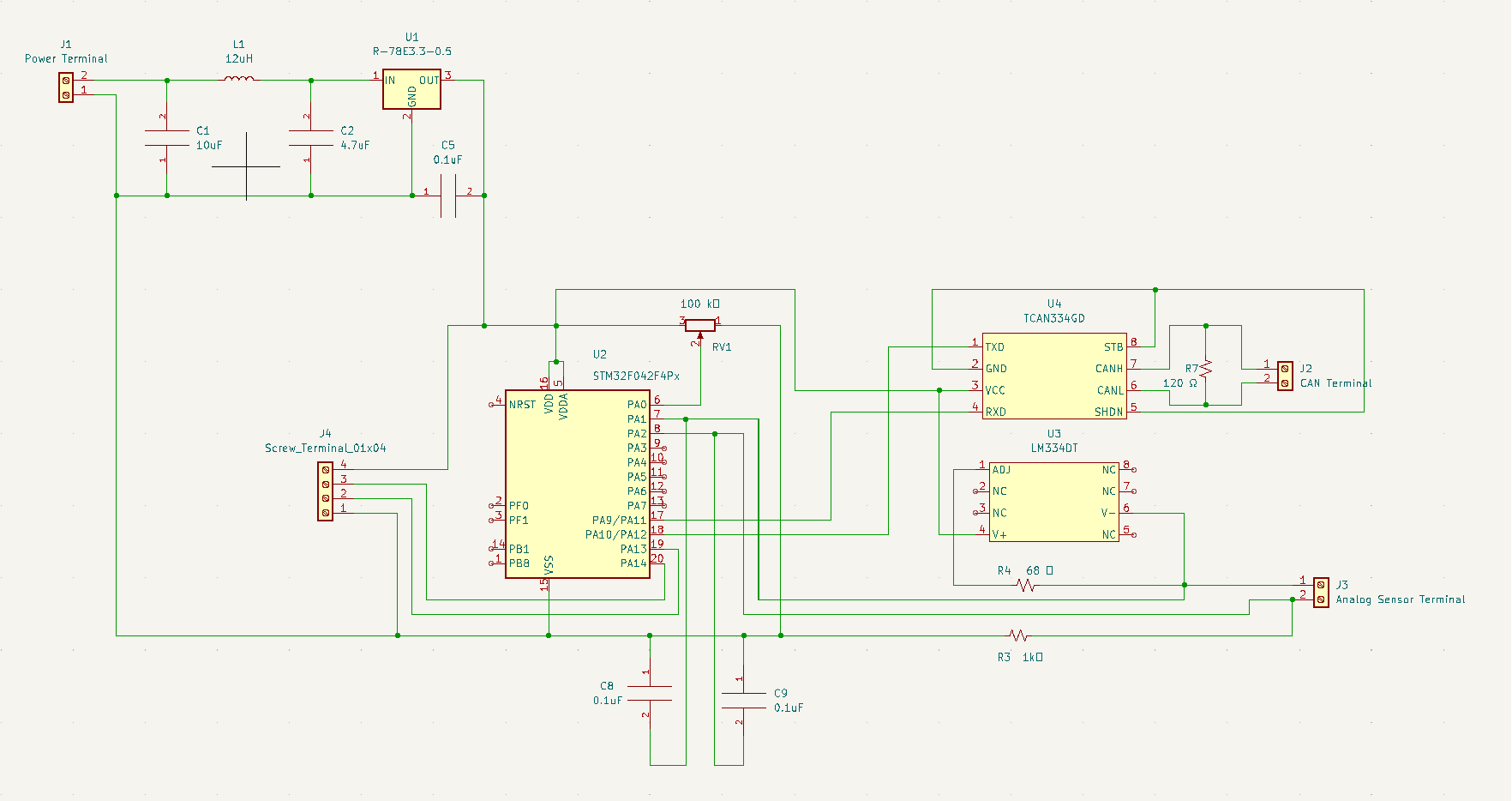
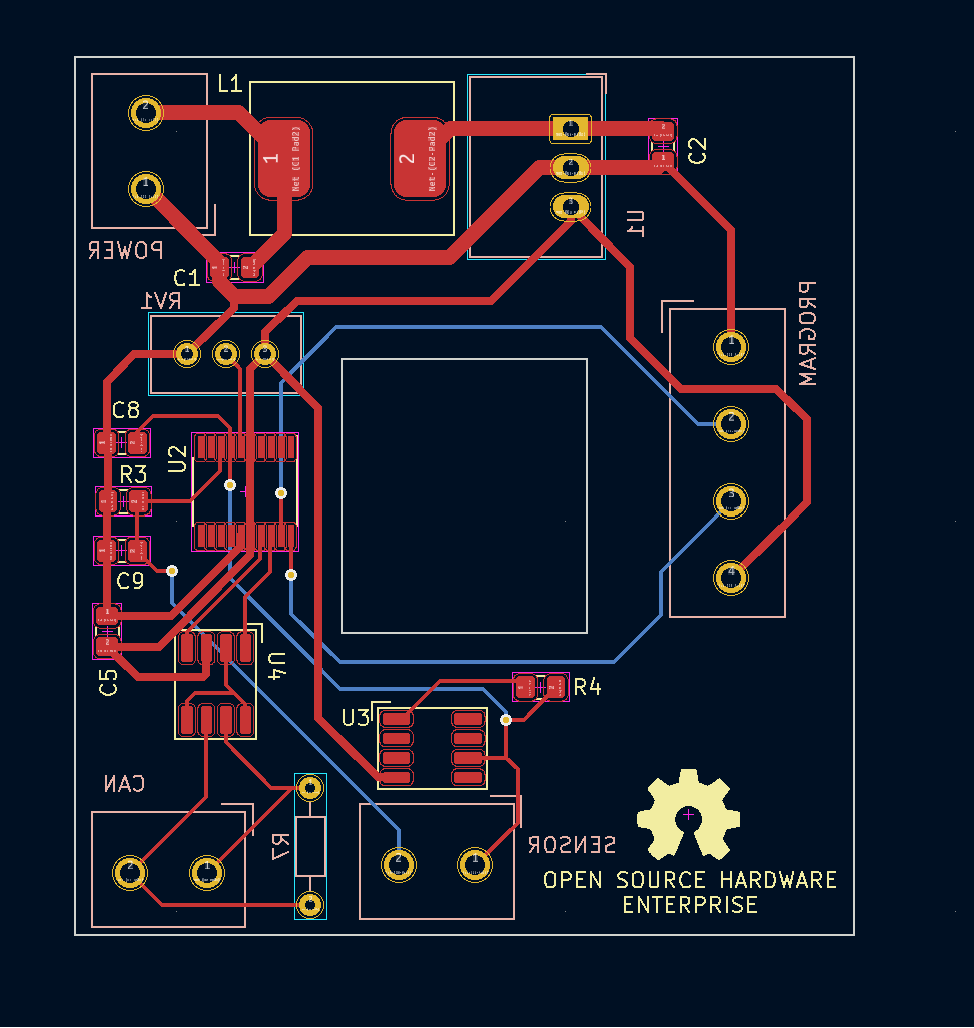
3/23/24
This week I worked on getting everything in order for assembling the initial revision. I ordered the Dwyer sensors on Monday. I went with Ben and Tanner to the mine site on Wednesday and met with Jared B. from Bay Electric. We discussed the specs of the system and what we would need in relation to solar power. He will be sending us specs of a few options, hopefully this week. Thomas retrieved power data from the DAQs. One of the microSDs did not record, so we only have one set of data but it is better than nothing. It is interesting to have but with the addition of Bay Electric into our plans, I do wonder how useful it will be. I have included a slice of the data below.
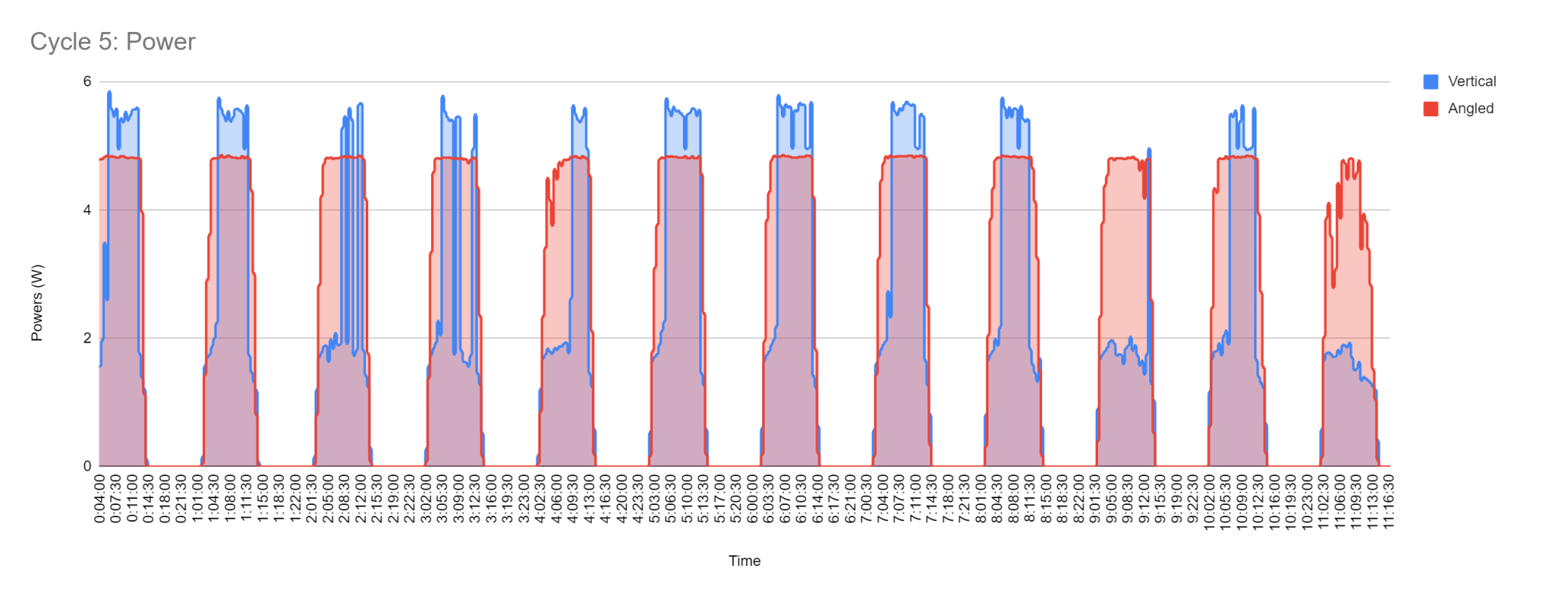
We received all parts this week, including sensors, components, and PCBs. I included a picture of the PCB fit below. I plan on soldering a few of the PCBs together and testing out the boards for functionality. Hopefully, Thomas has finally got the programming working so this can all come together. Ben has got in contact with a wire supplier and we plan on ordering wire on Monday. This means hopefully two weeks from now, we can do a power test in an environment chamber at Orbion, after we proof functionality this coming week. I also plan to support Mitch on the UI this week if it is needed.
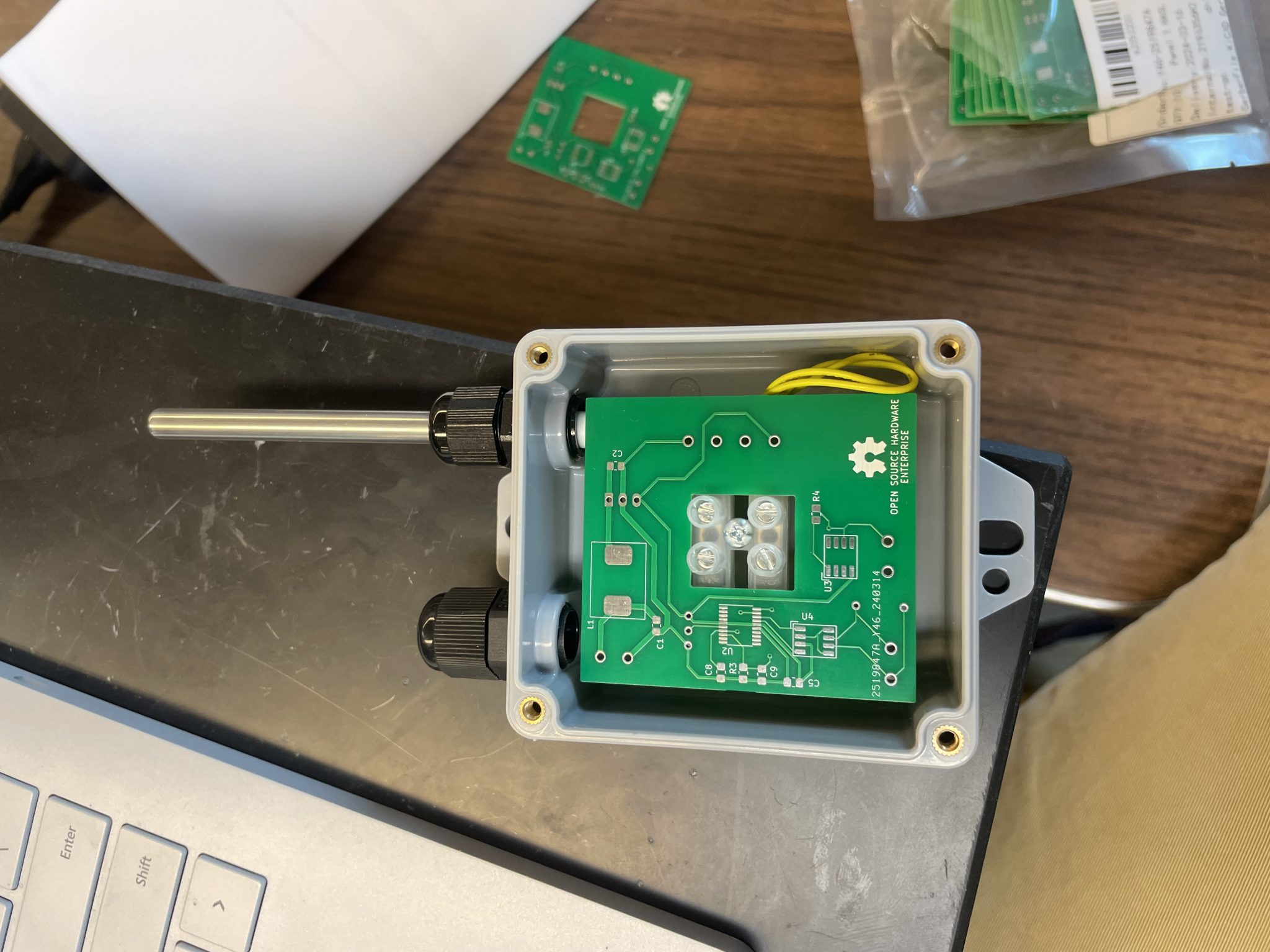
3/30/24
The start of this week I focused on assembling the boards. I went to the Plexus Lab and learned how to use the solder paste dispenser along with the pick and place machine and the reflow oven. I used this to solder most of the SMD components to the board. Unfortunately the footprint for the STM32 was too fine for the solder paste dispenser (I foolishly forgot to get a solder mask) so that got hand soldered by Ben at Orbion. One of the boards has all of the SMD and THT components on it, two are still needing the THT components. I plan on completing that early next week. Hopefully this will allow for a complete functionality test to be performed early next week. Thomas is waiting for mini HDMI wire to come in to program the Pi Zero to receive the CAN messages, but it should be in early next week. I need to have everything hooked up on the hardware side before then. Below is a picture of a completed board. The board does fit in the box but I have not tested wire for strain yet.
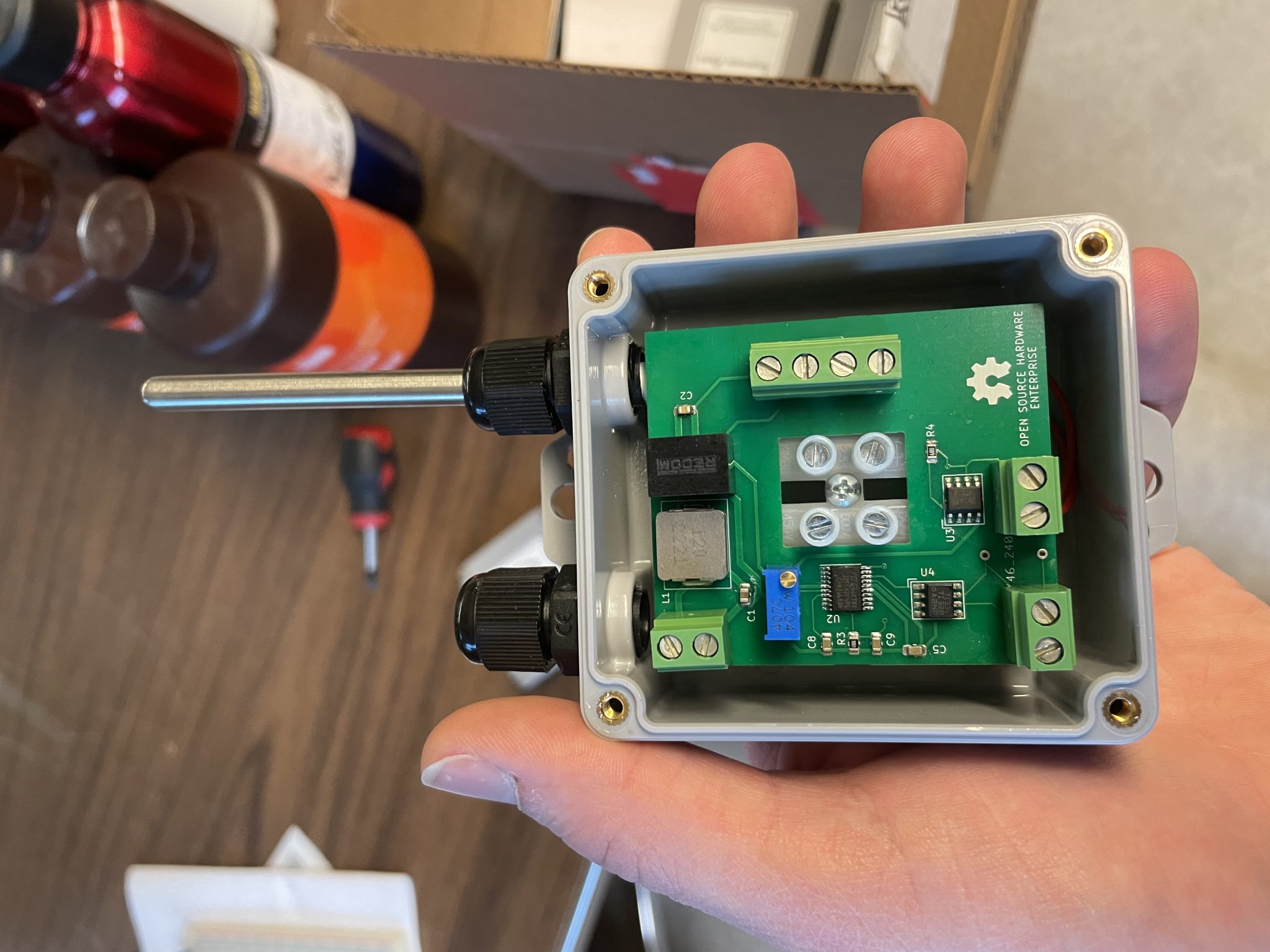
At the tail end of this week I began to design the control system for the hibernacula. I worked off of Dr. Manser model to create a discrete plant model. I then mapped the discrete model to the analog domain to create a modified PI controller. I think I am going to use the analog model to run a simulation as a test to see if everything checks out. I created the model with a single input and I think I might need to modify it to compensate for multiple outputs. We are planning on creating a weighted average (using a Gaussian distribution) and roll them into one value so I will be interested in how well this works. I am also nervous that it will create a cold band at the start and this will stop any bats from crossing into other climates. Best practice here is to run a few different simulations and create a few different maps of what the cave will look like. I am also nervous about running simulations that are suppose to model a month of temperature changes. I also probably need to figure out how to take into account distance and the cave warming because that is not included in Dr. Manser’s model. Once I get everything looking pretty I am going to map the controller back to the discrete domain and figure out the difference equations for the Nano to use. I have included the math I have used so far below.
A few odds and ends updates: I did a little back calculations on how much weight the wire mounts will have to support, came out to be about 5lb. I would think this is unlikely to be an issue but I referred it to Tanner to check in with John just in case. I proof read Ben’s first draft of the Fan report and left feedback. Also I hope Mitch can complete a dry run of the UI this week because I think it would be smart to run a usability test with Tanner and modify the UI based on that. Next week, I would like to complete a full functionality test and simulations. If wire is in early enough, a power test in the Environmental Chamber would be an amazing stretch goal for next week.
4/6/24 Update
Not a great week and at a very bad time to have a not great week. I did not make as much progress as I wanted to on the control scheme. I did an initial simulation and it did a great job of heating the cave by 1 deg C. I do not have the controller fully implemented yet, so hopefully that is the issue. I am thinking about not following down that path and doing a more common sense approach (e.g. we need not run the controller when it is this warm, bang bang style, etc.). I think that will simplify everything greatly and meet rise time specs, but nervous that we’ll get poor overshoot and steady state error. I think there are some good nonlinear methods to handling those issues though. I also found and filtered a data set to use in the simulation. Most of time this week did go towards troubleshooting hardware, because at this point no one else has the skill set to do. Had to debug the power system for a good bit. Also used what I saw to update the PCB layout, mostly better labelling and keeping all components on the topside (that is actually what caused the power system bug). Really nervous about wire strain inside the box. Other than that though, it looks really clean. Ran out of time to try and cover for Mitch on the UI. I did get everything rolling for Design Expo with the other teams, so that is good. I think in all honesty the thing I am most worried about is the team. They are very, very bad at buckling down when it is go time and it is go time. Last time this happened I got abandoned to cover for everyone and it was not fun. This week I need to get the new PCB ordered with JLCPCB doing the assembly and the controller simulation at least working. I will probably also have to spend time babysitting the behind schedule functionality test, power test, and UI.
4/13/24 Update
This week I did the final PCB redesign. I mostly focused on trying to decrease the footprint of the PCB to reduce strain on the wires. I also tightened the center cutout so that it fits better on the sensor structure. Some of the screw terminals were also rotated for better wiring positioning. I added labels to the inputs and redid some of the descriptors.
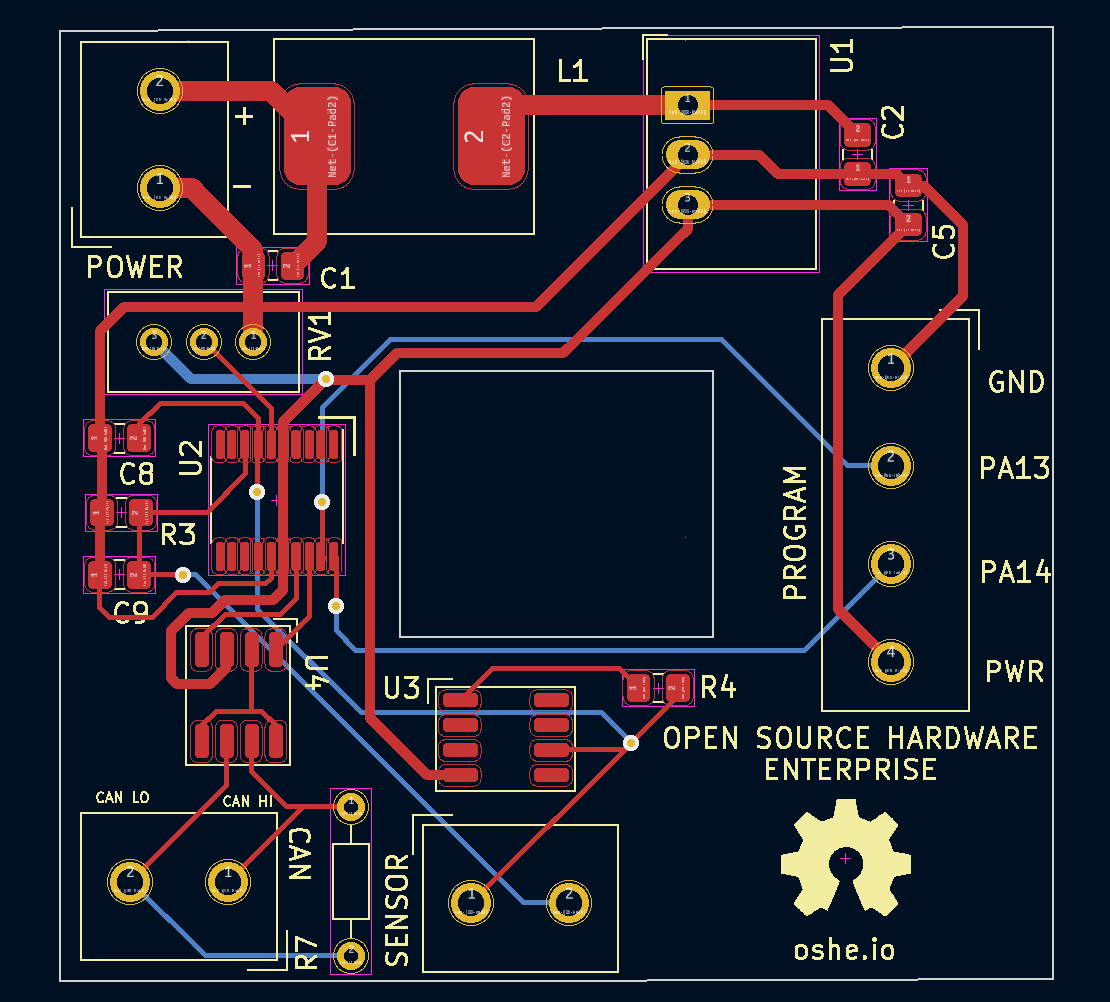
Another thing I got down was adding a second sensor on to the CAN network. I had to redo some the harnessing for that, but it looks solid. I also helped get everything prepped for Design Expo next Tuesday.
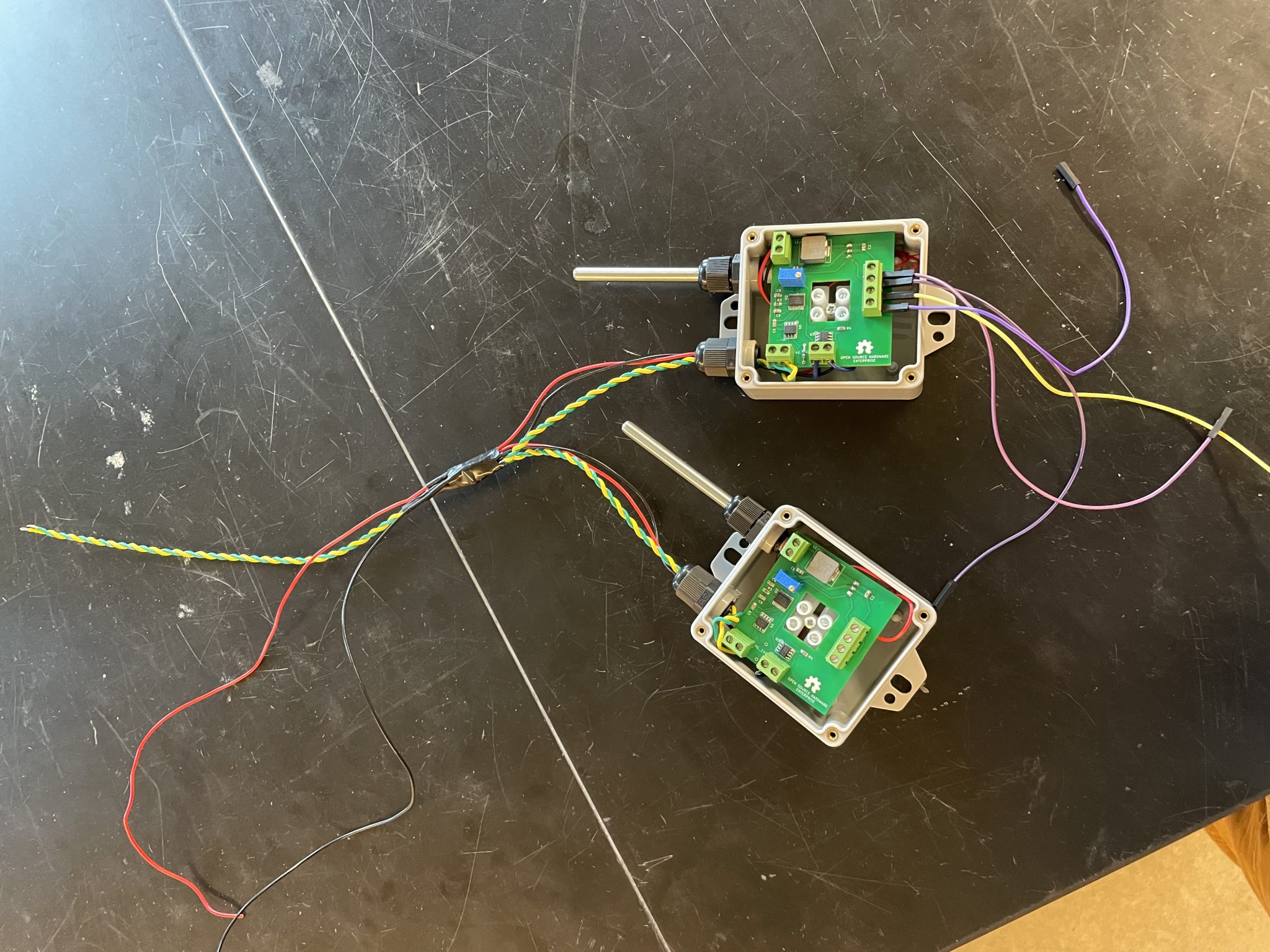
Finally, I did some more work on the control system. I have the system simulated using a relay controller (bang bang) and have initial results. I might go for a more complex controller if there is time to design one. The model is still a little too simple. I need to figure out a way to implement the heating from the walls and figure how to create the relationship between distance and fan cooling. I also need to deal with the steady state issue.

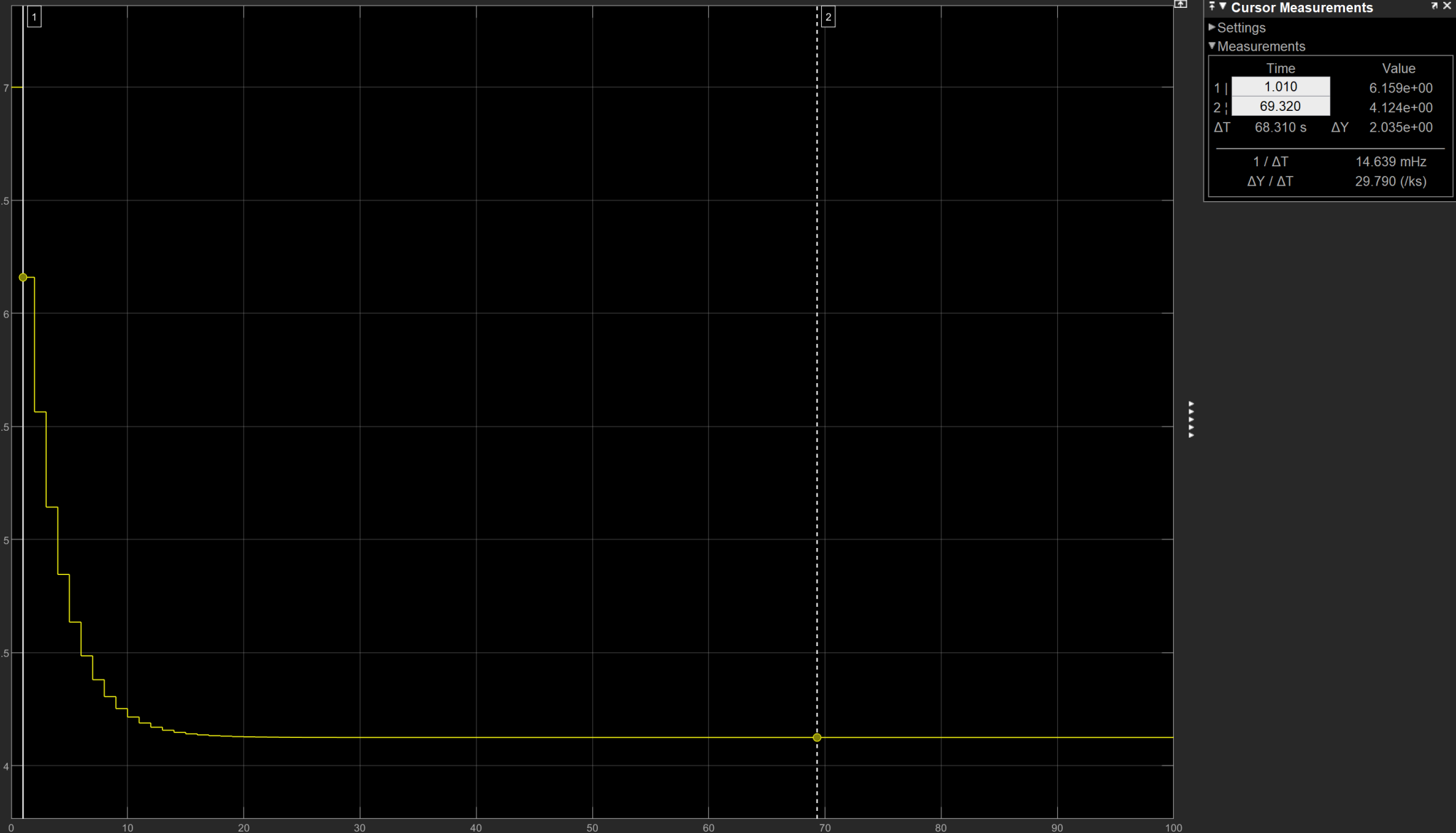
4/20/24 Update
This week I spent some time preparing for and attending design expo. Other than that I worked on improving the controller simulation. I managed to to add in a heating section based off some papers written about the Carlsbad Cave in New Mexico which gave a rough approximation for our cave (I believe that the actual rock type is different which would influence the thermodynamics a little bit, but not a lot). I also spent a good chunk of time trying to implement the February data set being used in the model. I have not seen a lot of success in this so far. It seems to be unhappy about the February data being discrete and everything else being continuous. I have tried a few methods of the discretizing the rest of the system or making the data input appear continuous but nothing has worked. I will probably continue to try a few things to get it to work in the next week along with trying to create a system for the multiple sensors. Unfortunately, we have not heard back from Dr. Manser, so I will probably have to create that system from scratch. My goal is to have a few different distributions to show Tanner on Wednesday. I have attached the current model below (with the constant input and the nonconstant input). The results from the constant input model should also be below.
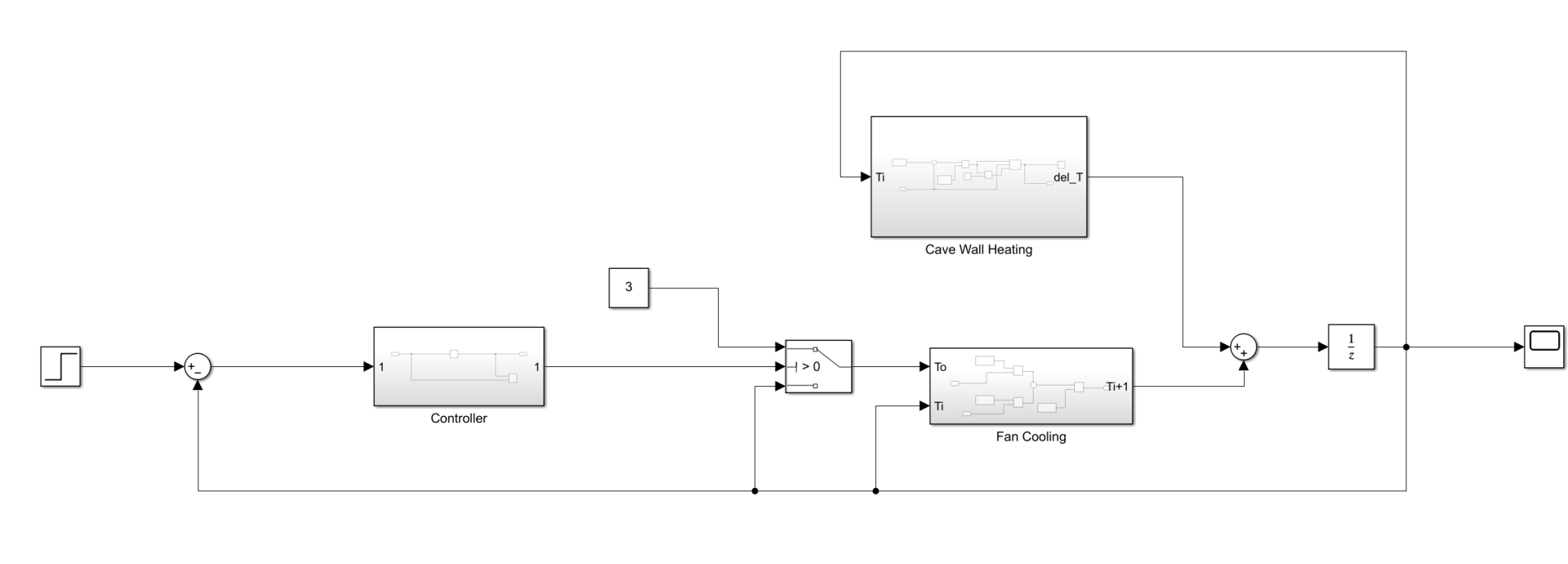
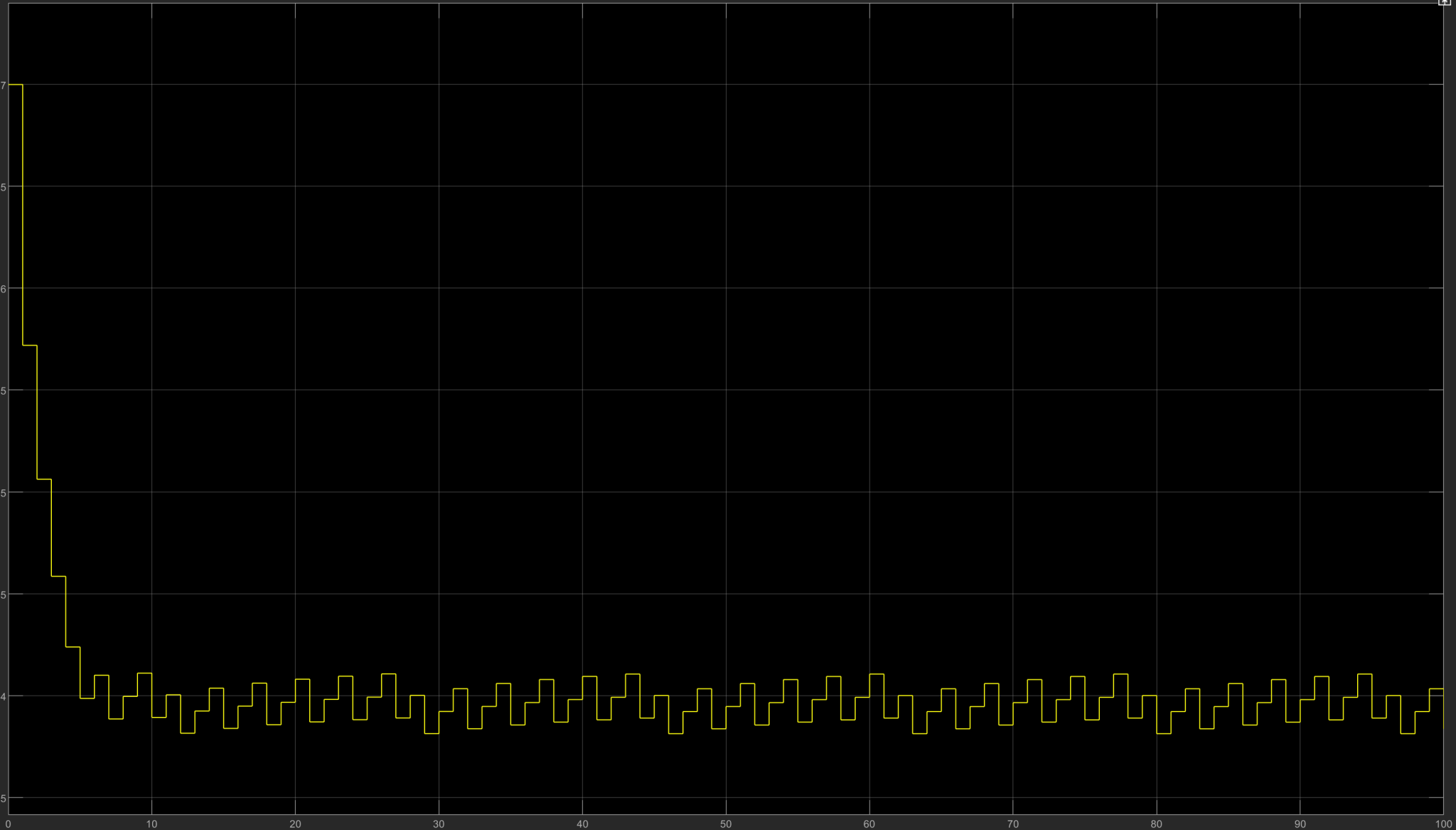
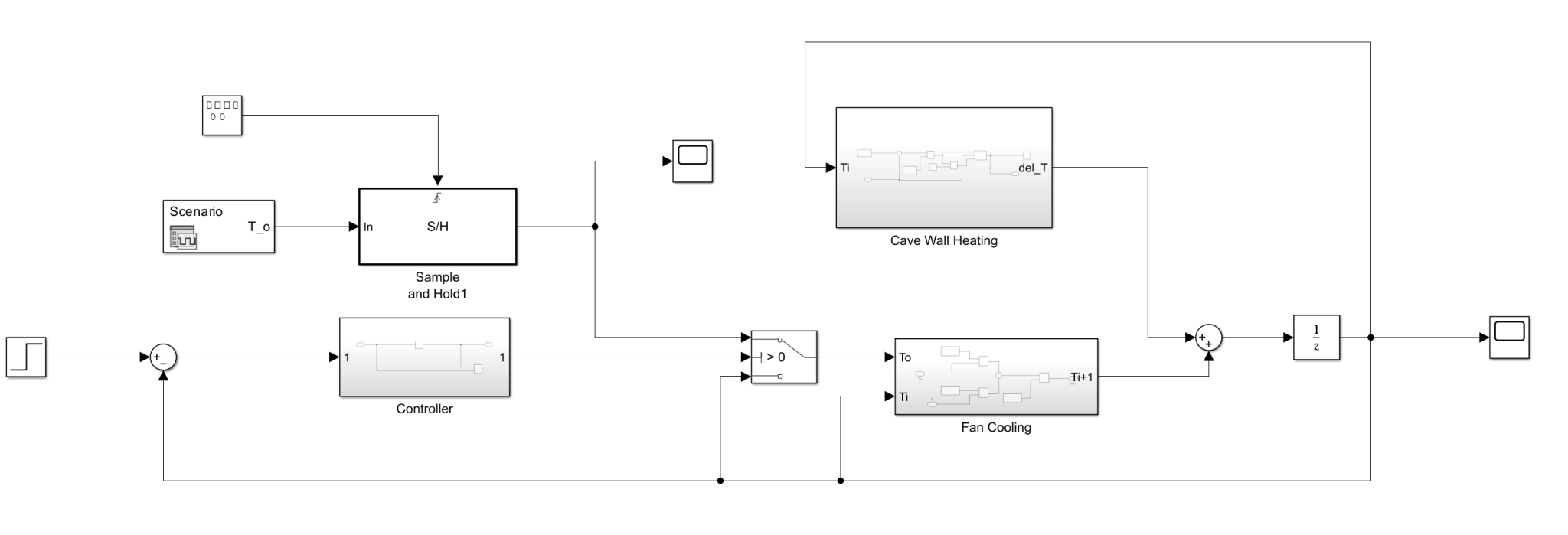
A few other minor things I worked on was getting the final part order complete and finding a relay to switch the fan. In the final stretch here, I look to put together a final look at the controller and help with the assembly of the final harness. A usability test of the UI would also be good to run but I feel like that will not happen. Hopefully, everything is somewhat tied up by Wednesday, but if we need to run over a little to Thursday for assembly, it wouldn’t be the worse.