4/19/2025 Work Loag
Reflection on work since last week
- Not a lot with exams coming up
- Project Report
- A bit of work on the report, added pictures and figures to assembly instructions
- Implemented changes proposed by report reviewer
To Do
- Finish Report:
- Update BOM for BREAD integration
- Final review before submission
Concerns
- None 😀
4/13/2025 Work Log
Reflection on work since last week
- A loooooooot of documentation
- Turns out the rewind unit is pretty complicated
- And because there is so much small information about the project there is a lot that can go wrong
- Thus: Troubleshooting Section!!
- Basically just an FAQ of everything I think could likely go wrong and how to fix it
To Do
- Finish Report:
- Update BOM with bread mess
- Take a lot of pictures for assembly instructions
Concerns
- Feels like there’s no way to actually put all of the information about this project to page without spending hours of time and dozens of pages, especially with finals coming up and 23 assignments due this week.
4/6/2025 Work Log
Reflection on work since last log
- Check off!!!!!
- Got just about everything working
- Fixed control loop on stepper side
- Tuned Infidel sensor with known thickness filament
- Got DAQ to work properly with data recording to SD card
- Set up loaf esp as live monitor with some hackiness
- Things that didn’t work so smoothly
- Stepper motor started slipping from driver overheating
- Infidel sensor instability due to:
- Lots of vibrations through rewind unit
- Lots of EMI in lab affecting hall effect sensor
- Got just about everything working
To do
- Fix stepper motor driver with heatsink (and fan if needed)
- Add better shock absorption to rewind unit to reduce knocking of infidel rocker
- Investigate Faraday cage as solution to emi problem
- Run the rewinder again, this time with ground up 3d print waste!!!!!
- With any extra time give some love to the loaf esp32?
- Fix the website’s jankiness
- Correct units
- No redundant info
- Keep track of last X measurements
- Fix the website’s jankiness
- DOCUMENTATION!!!!!!!
- Stuff I specifically should do (in addition to helping with others)
- Soldering guide
- Loaf usage guide
- Infidel sensor shenanigans
- Software/Flashing microcontrollers and best practices
- Disable external power before flashing
- Only ever flash one at a time
- Guide to tuning infidel sensor and stepper start speed
- Upload all software to osf-archive
- Stuff I specifically should do (in addition to helping with others)
Concerns
- None really, I’m a happy camper
3/30/2025 Work Log
Reflection on work since last log
- Did a lot of work on software side of rewinder
- bread integration
- can
- motor control
- infidel tuning
- Control loop software needs a lot of work
- System is running on multiple second old data, thus needs to predict input response
- Options:
- Fancy software PID loop
- Hard to implement and run on esp though could work the best
- Modify existing loop
- A lot of trial and error work, may never function fully
- New control loop based on incremental speed increases (only once every 5 mins)
- Simple, though relies on having the correct diameter as an initial condition
- Would require determination of initial speed to get a perfect 1.75
- Simple, though relies on having the correct diameter as an initial condition
- Fancy software PID loop
To Do (For the next while, not just to next week)
- Software Software Software
- Stepper Motor Slice
- Basic motor control ✅
- CAN receiving ✅
- Advanced motor control ✅
- Speed adjustment without feedback
- DAQ
- Support different CAN frame supporting: ✅
- Thermistor data
- Infidel sensor data ✅
- Fix record keeping on SD card
- Support different CAN frame supporting: ✅
- Loaf (EXTRA)
- Support new CAN frame used by DAQ
- Update web server to support the displaying of the new frame
- Try and find better solution to web server displaying?
- Other than hard coding HTML into the source code
- At least put it in one spot at the header?
- Other than hard coding HTML into the source code
- Stepper Motor Slice
- Hardware
- Get thermistor working with DAQ
- And decide where to place it (ask Konnor)
- Test stepper motor slice with our actual stepper motor ✅
- Test Loaf power from the Recyclebot power supply ✅
- Will on buck converter for 12V to 5V conversion ✅
- Get thermistor working with DAQ
- Test it all together!!!!!! (almost ✅)
3/23/2025 Work Log
Reflection on work since last log
- Ran the full recyclebot system with all parts concurrently!!!!!
- Actually spooled some filament (it’s bad filament but its filament!)
To Do (For the next while, not just to next week)
- Software Software Software
- Stepper Motor Slice
- Basic motor control ✅
- CAN receiving
- Advanced motor control
- Speed adjustment without feedback
- DAQ
- Support different CAN frame supporting:
- Thermistor data
- Infidel sensor data
- Fix record keeping on SD card
- Support different CAN frame supporting:
- Loaf (EXTRA)
- Support new CAN frame used by DAQ
- Update web server to support the displaying of the new frame
- Try and find better solution to web server displaying?
- Other than hard coding HTML into the source code
- At least put it in one spot at the header?
- Other than hard coding HTML into the source code
- Stepper Motor Slice
- Hardware
- Get thermistor working with DAQ
- And decide where to place it (ask Konnor)
- Test stepper motor slice with our actual stepper motor ✅
- Test Loaf power from the Recyclebot power supply ✅
- Will on buck converter for 12V to 5V conversion ✅
- Get thermistor working with DAQ
- Test it all together!!!!!! (almost ✅)
Concerns
- Time remaining is shrinking
3/16/2025 Work Log
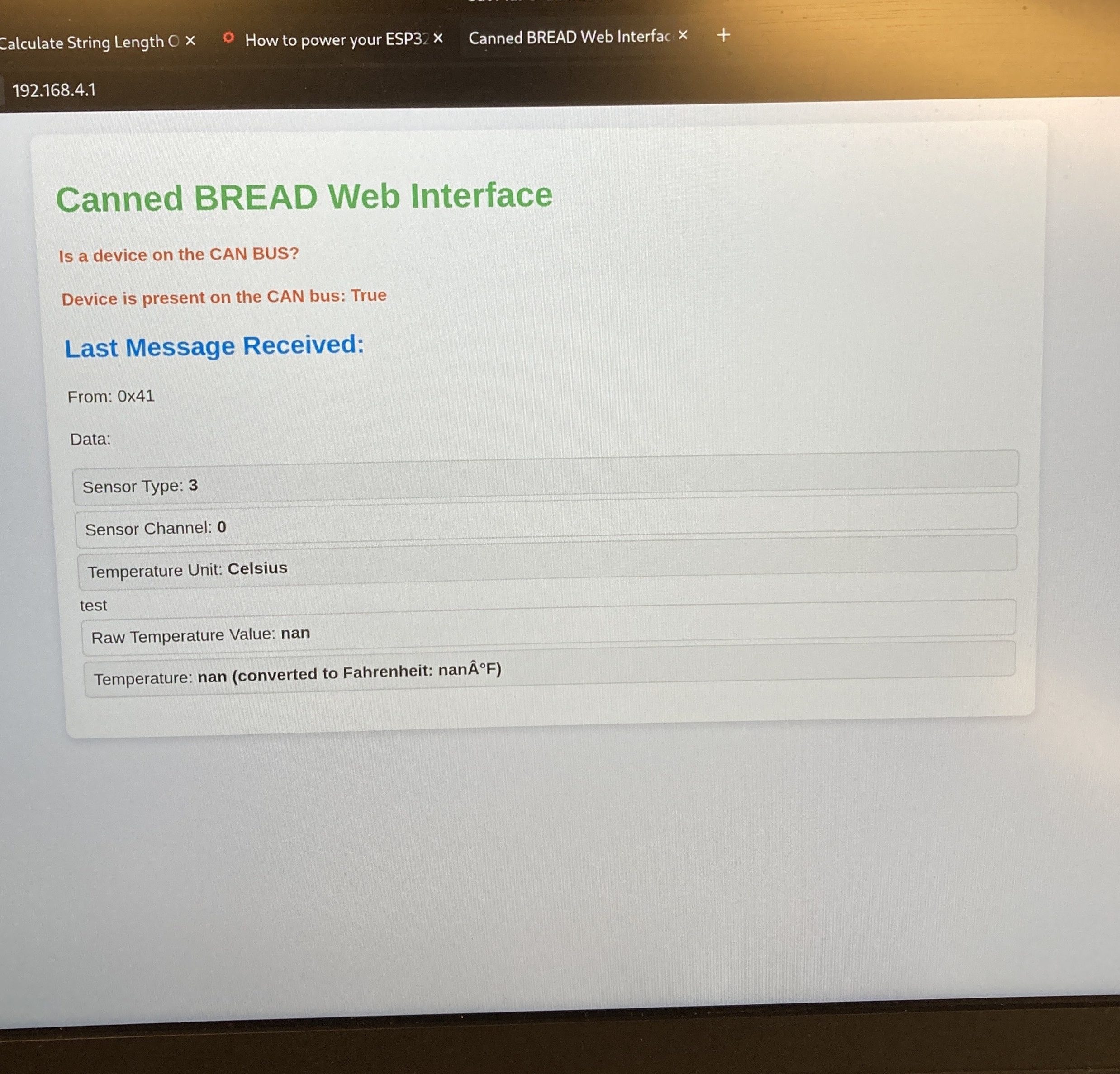
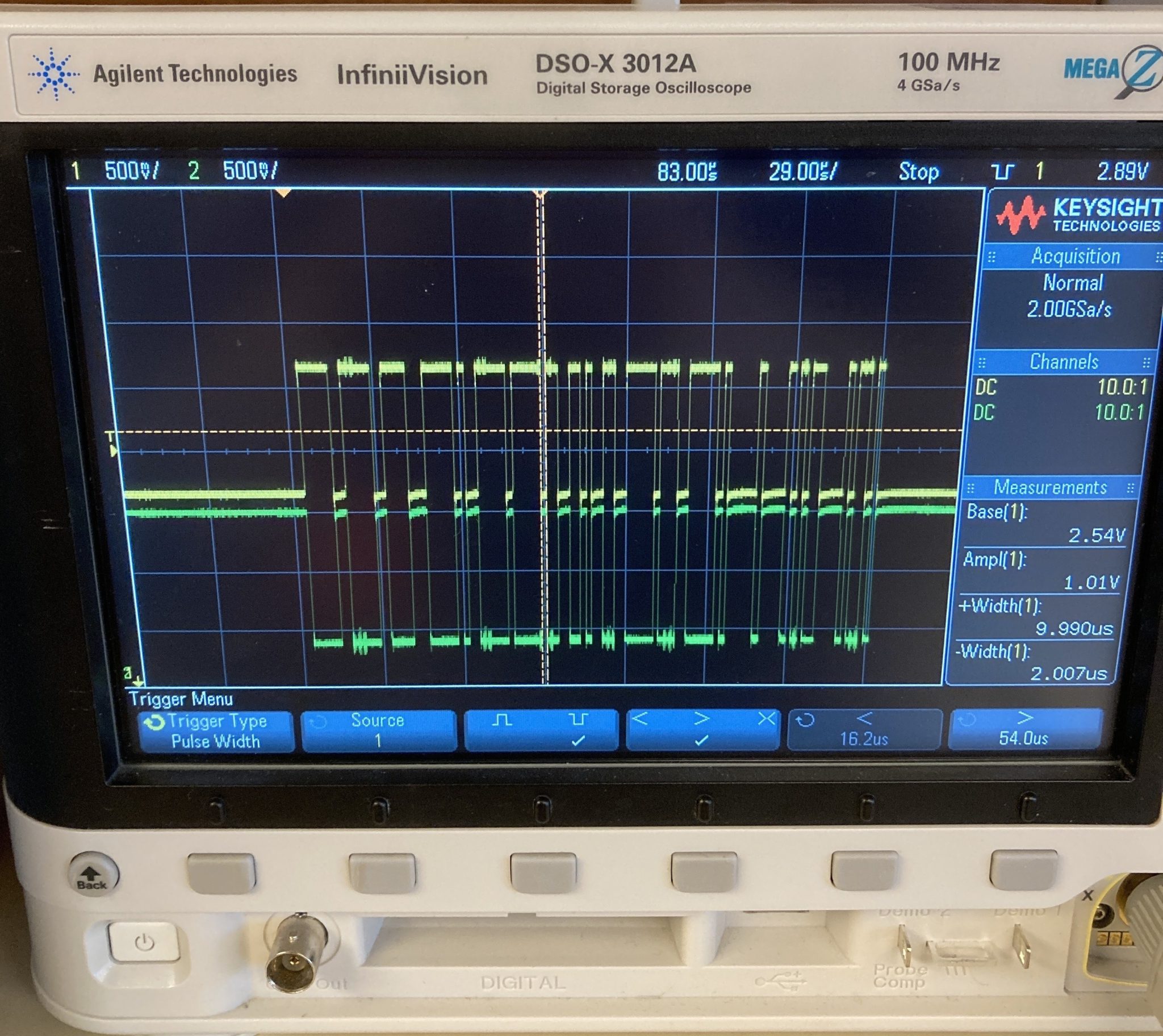
Reflection on work since last log
- Successfully achieved CAN communication on the loaf, as seen in pictures above
- Started on coding of stepper motor slice for control loop
- Updated stepper motor pcb with fixes to TX/RX lines and 12V power for motors
- Figured out how to hook up the Infidel to BREAD DAQ
To Do (For the next while, not just to next week)
- Software Software Software
- Stepper Motor Slice
- Basic motor control
- CAN receiving
- Advanced motor control
- Speed adjustment without feedback
- DAQ
- Support different CAN frame supporting:
- Thermistor data
- Infidel sensor data
- Fix record keeping on SD card
- Support different CAN frame supporting:
- Loaf (EXTRA)
- Support new CAN frame used by DAQ
- Update web server to support the displaying of the new frame
- Try and find better solution to web server displaying?
- Other than hard coding HTML into the source code
- At least put it in one spot at the header?
- Other than hard coding HTML into the source code
- Stepper Motor Slice
- Hardware
- Get thermistor working with DAQ
- And decide where to place it (ask Konnor)
- Test stepper motor slice with our actual stepper motor
- Test Loaf power from the Recyclebot power supply
- Will on buck converter for 12V to 5V conversion
- Get thermistor working with DAQ
- Test it all together!!!!!!
Concerns
- Just time
3/9/2025 Work Log
Reflection on work since last log
- Presented at general meeting
- Talked with GE sponsor with updates
- Stepper motor slice PCB came in
- Fully soldered
- BREAD Loaf and DAQ fully tested separately and together
- Communication over CAN from DAQ to Loaf ESP32
To Do List:
- Update PCB with fixes (RX/TX swap, screw terminal size)
- Test the new stepper motor slice
- Test the CAN bus with arbitrary communications
- Connect thermistor and infidel to DAQ (Consider infidel on stepper?)
- Write control loop software to adjust the rewind stepper motor
Concerns:
- Main power to the stepper slice enters through a smaller terminal than expected
- Overcurrent could cause connector to melt
- Need to check datasheet for current capabilities
- Worst case power inputs just need to be soldered directly to pcb
- Control loop software could be non-trivial
- Need to be very careful not to create a positive feedback loop from motor overcompensation
2/16/2025 Work Log
Reflection
- Did cdr presentation
- Finished soldering bread loaf
- Figured out where our stepper slice pcb went (stalled at review, shane missed email)
To Do List:
- Test loaf hardware for any work needed
- Add the resistor patch to the back of the pcb
- Test CAN software, get DAQ and loaf talking
Concerns
- Stepper slice not being here sucks, will have to do some soldered breadboard work in the future to test the bread slice before it arrives here
2/4/2025 Work Log
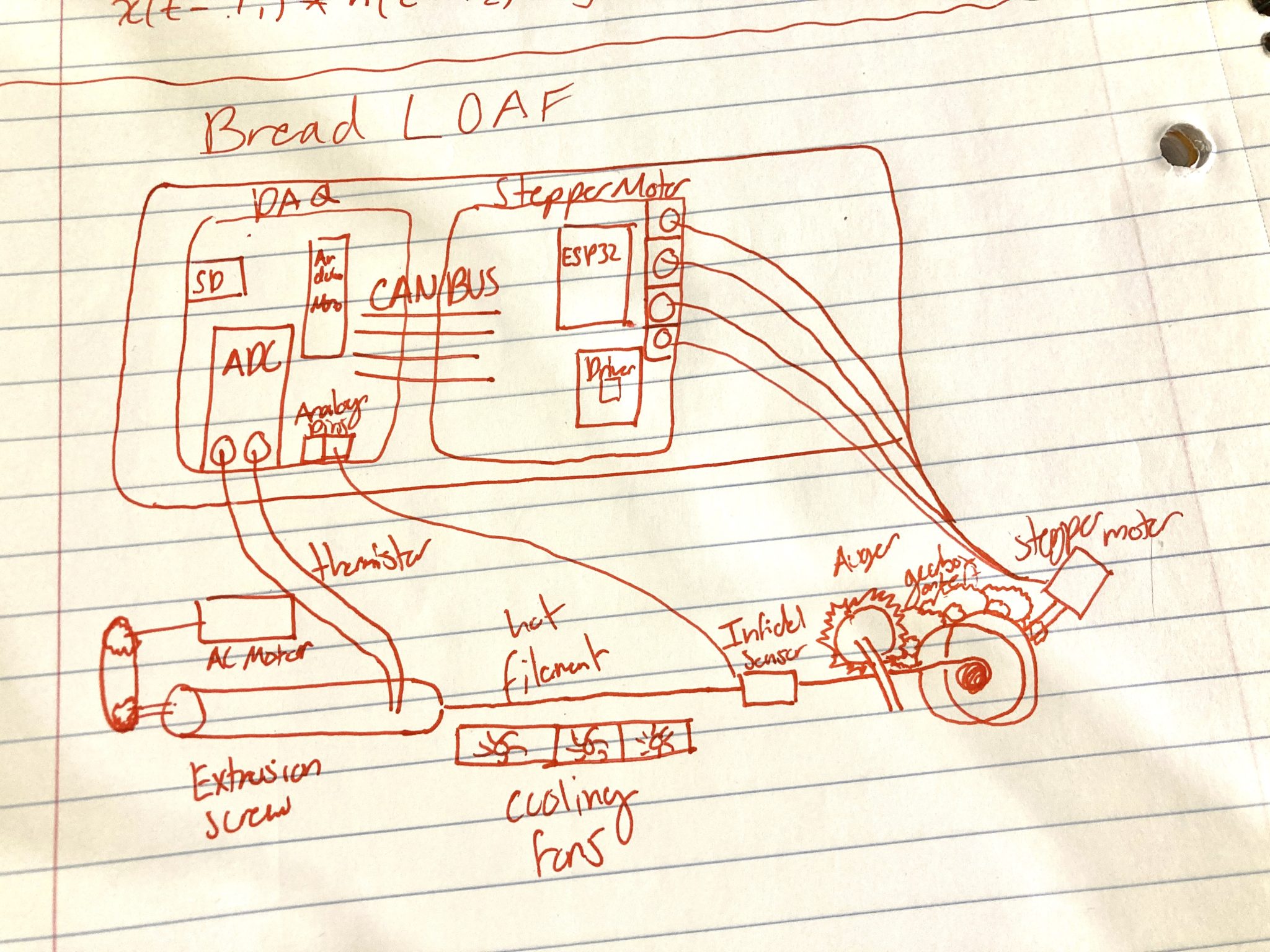
Reflection
- Not a lot due to exams and protodash.
To Do List:
- Need to finish soldering the loaf, hopefully solder slice before CDR too
- Look further into inkbird thermistor
- Looks like there’s probably no output
- Once done soldered test can on new loaf
Concerns
- May need to crunch a bit to get things done before CDR. Hopefully slice pcb comes in on time and we can start testing more of the whole thing.
1/26/2025 Work Log
Reflection:
- Got dev environment set up for esp32 programming, turns out the vs code extension is only for the official vs code application, not the codium build I was using (screw you microsoft >:[ )
- Properly got the loaf repo to build and flash on the esp32, with a couple quick fixes due to code not compiling (should probably do a pull request)
To Do List:
- Look into inkbird thermistor monitoring with the bread DAQ given to us
- If no digital output: look into shielded cables for analog output?
- If no output at all: cry?
- Ask to borrow the spare bread loaf for testing my own CAN code betwixt esp32s
Concerns:
- Inkbird not having signal output would be reaaaaaaly inconvenient, and would force us to use secondary thermistors
1/23/2025 Work Log
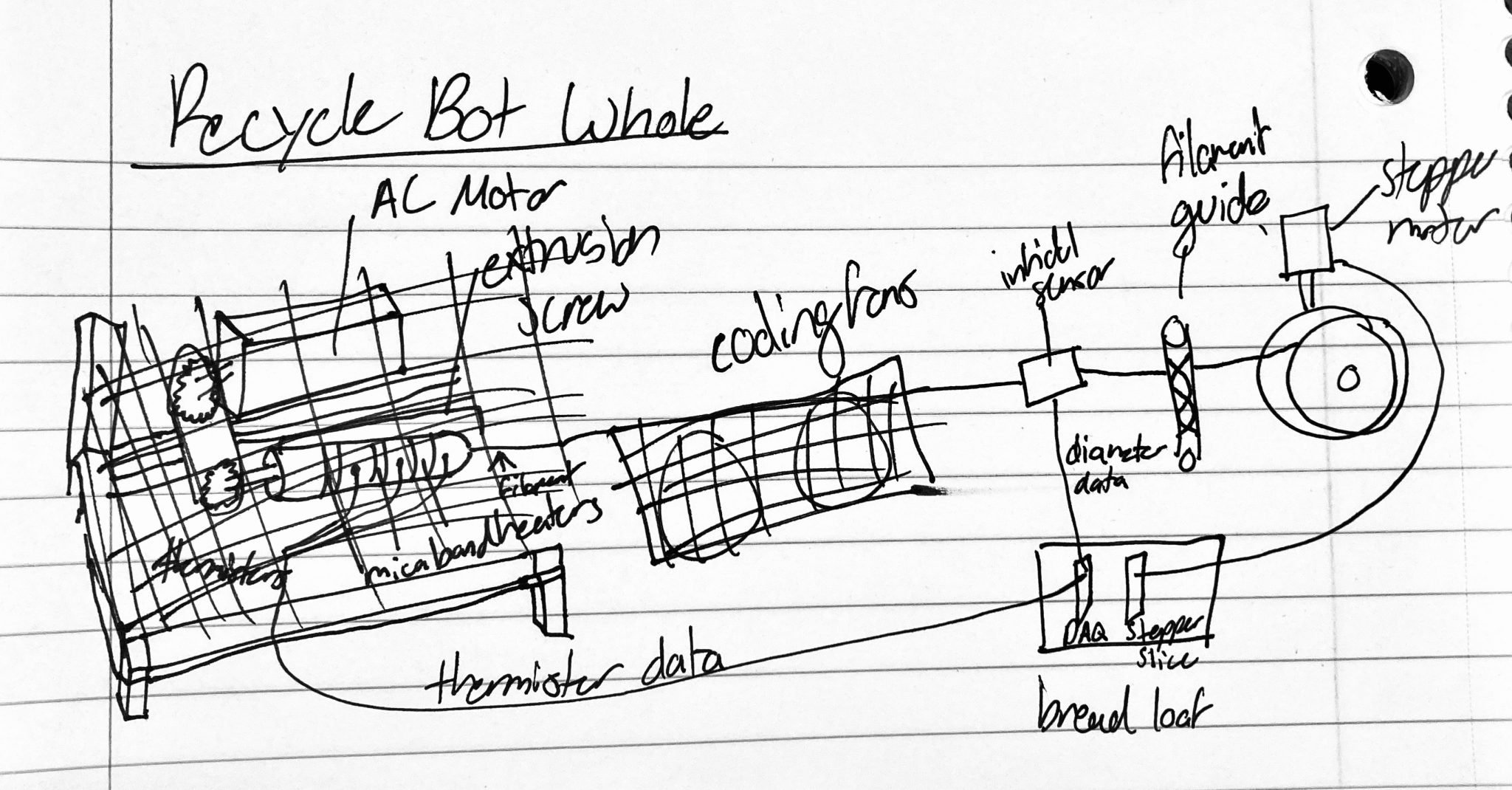
To Do List:
- Set up development environment for esp32 programming
- Get CAN bus working for esp32 on breadboards
- Look into setting up thermistors (inkbirds) for Bread DAQ
Concerns:
- PlatformIO vscode extension is not listed on their marketplace
- Needed for esp32 programming
- May need to install manually
- If inkbird do not support digital thermal readings will have to use ADC on DAQ
- May cause signal retention issues with long analog signal
10/14/2024 Work Log
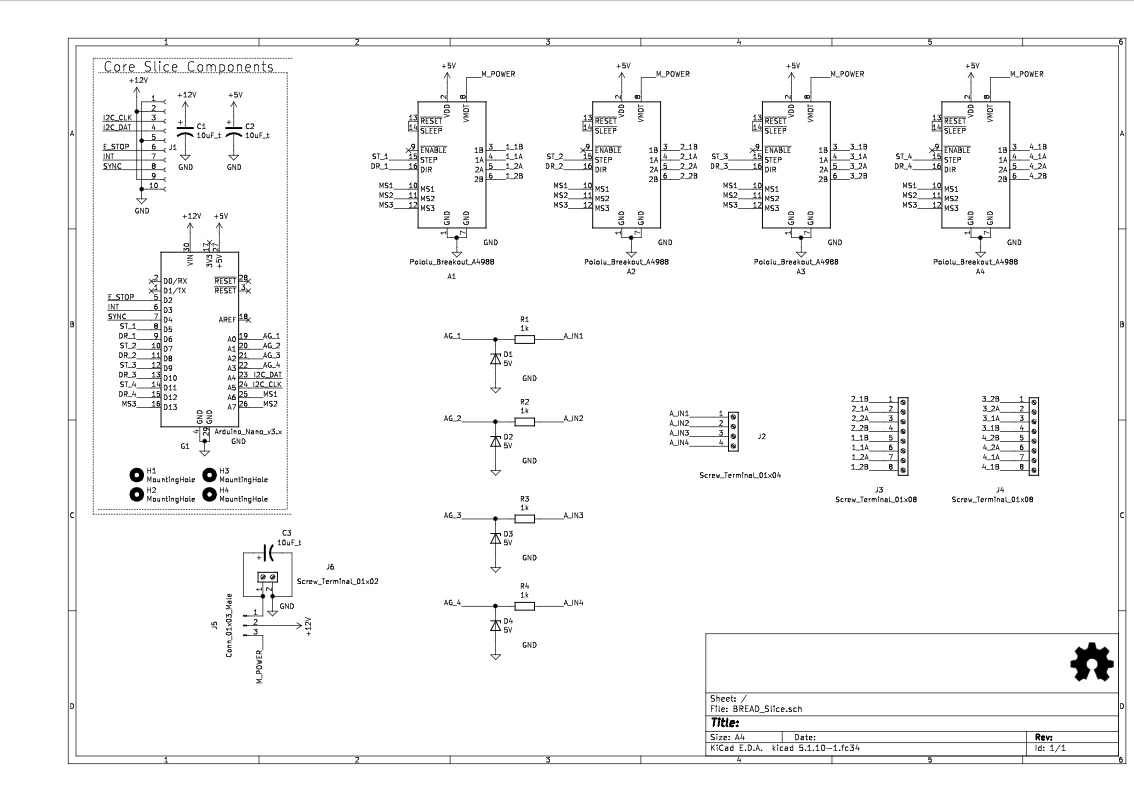
Reflection on last two weeks:
- Very productive, though progress is very split up due to the Proto-Dash event as well as CDR week
- CDR presentations took up a considerable amount of my work on Recycle-Bot, though we also had some very successful meetings to discuss future plans, both with Shane at our enterprise’s weekly meeting, as well as our individual team meetings with the rest of the Recycle-Bot team. We also had a great meeting with Brett Hildebrand from the bread team regarding our implementation of bread within our project, deciding to move forward with the new bread slice and loaf design being developed right now.
- As a result of moving the focus of our bread integration to a new platform, we are going to need to redesign the stepper motor bread slice made for the old bread specification to the new one, important changes include:
- Using the new edge connector instead of the old through-hole pin headers
- Updating the communication protocol on the loaf to be CAN instead of I2C
- Adding CAN transmitters and receivers to adapt the Arduino nano controller on the old slice to support CAN instead of I2C
- Regarding Proto-Dash, the event as of writing has roughly two days left until the deadline, with progress being very good. The team all communicated really well together, which allowed us to finish our prototype in just two meetings, with our only remaining requirements for the project being the video presentation of our prototype, which will happen on Tuesday (10/16/24) though i will not be present due to having class.
Goals for next week
- Get started on the updated bread slice, possibly discuss migration to an esp32 board instead of the Arduino nano on the old design
- Pros: no need for CAN transmitter and receiver, better future proofing from extra performance
- Cons: need to rewrite the software
- Work with Jeff and John to start modeling the parts needed for the rewind unit
- Filament guide
- Gear ratio/Belt for guide
- Infidel sensor
- Stepper motor to filament reel interface
- How it will all be supported on the chassis
9/29/2024 Work Log
Device Operation Diagram:
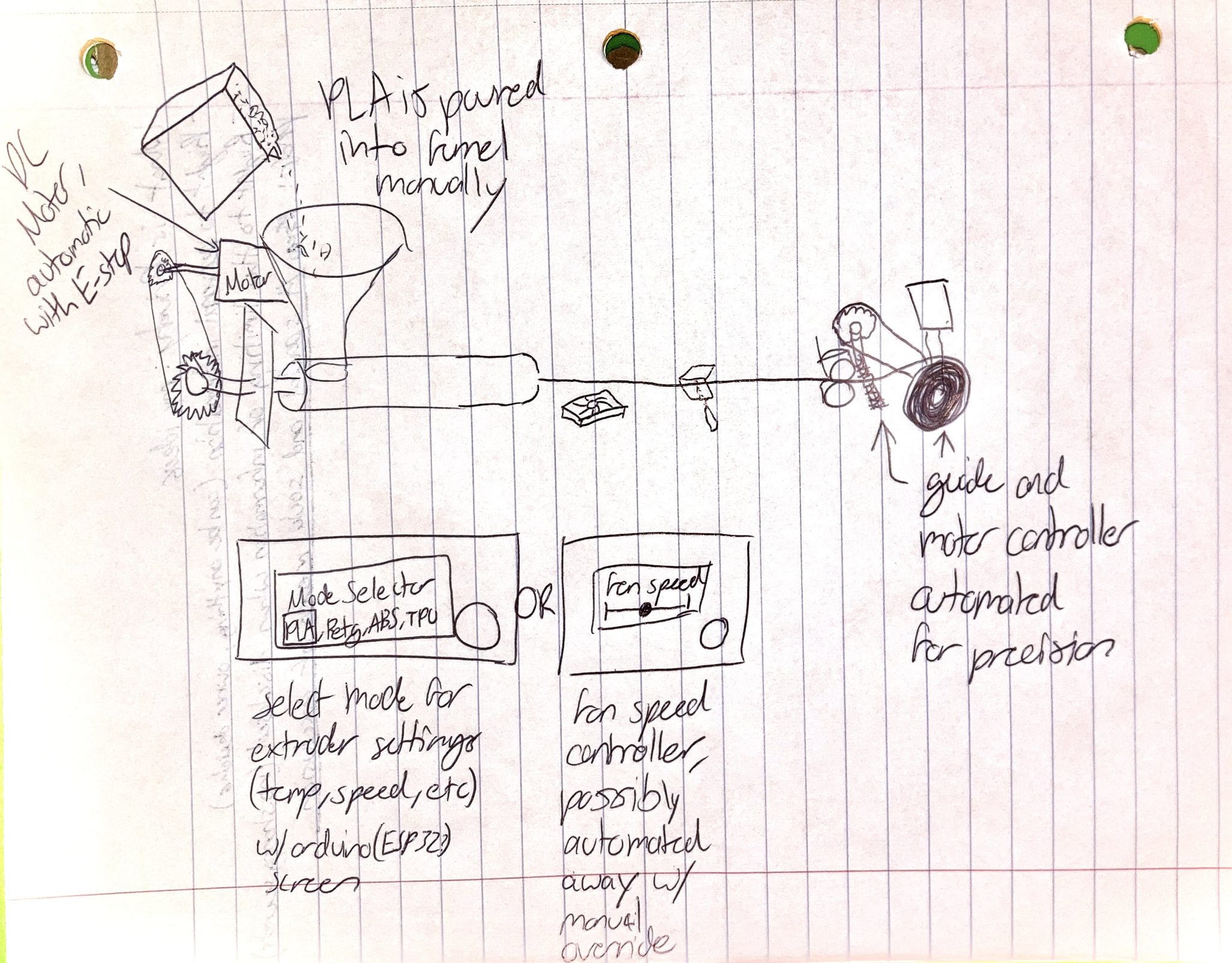
Reflection on last week:
- Slow progress due to career fair and exams, but progress was made nonetheless, particularly on my team with the gauge sensor, which has been narrowed down to using an optical sensor with a pinhole camera and mirrors, which will give good accuracy without touching the filament directly, allowing for measurement without risk of deformation.
- We put in our first purchase request, with many of the parts needed for the project’s first revision
- The CDR process has been started, with us prepping materials for the presentation
Next week’s to do list:
- Finalize a decision on and purchase a stepper motor option that is compatible with the stepper motor driver slice BREAD has already designed
- Start working on rewind guide 3d models and structural design for the stepper motor / gear ratios / belts
9/22/2024 Work Log
Reflection on last week:
- Good progress communication with BREAD, we have a much better vision for the electronics for the system now that we’ve communicated with the BREAD team.
- Our surprise presentation during the Thursday meeting went quite well, with us putting together a good representation of our project.
- The parts list for the rewind unit is ending up a lot more complicated than expected, sourcing a stepper motor and driver that will be compatible with bread will take a lot more care than originally anticipated, though much of the heavy work on understanding what we need is done, now we just have to find parts that meet all our needs.
- We took a look at some ideas for the structural and 3d printed parts needed for rewind, though this is the area the least progress occurred at.
Next week’s to do list:
- Finish putting together a part list for the main control loop for the rewind unit, including:
- Stepper motor
- Motor control driver
- Bread slice (using pre-existing BREAD motor controller slice)
- Gauge sensor (optical, hall effect, capacitive, etc)
- Work with the rest of the team to put together an idea for the main BREAD loaf (how many slices, arduino/esp, etc)
- Finish putting together ideas for the structural design and 3d printed parts needed for the rewind unit.
- Start to work on the (custom designed) part for the auger to guide the filament onto the reel.
9/13/2024 Work Log
Design Drawings:
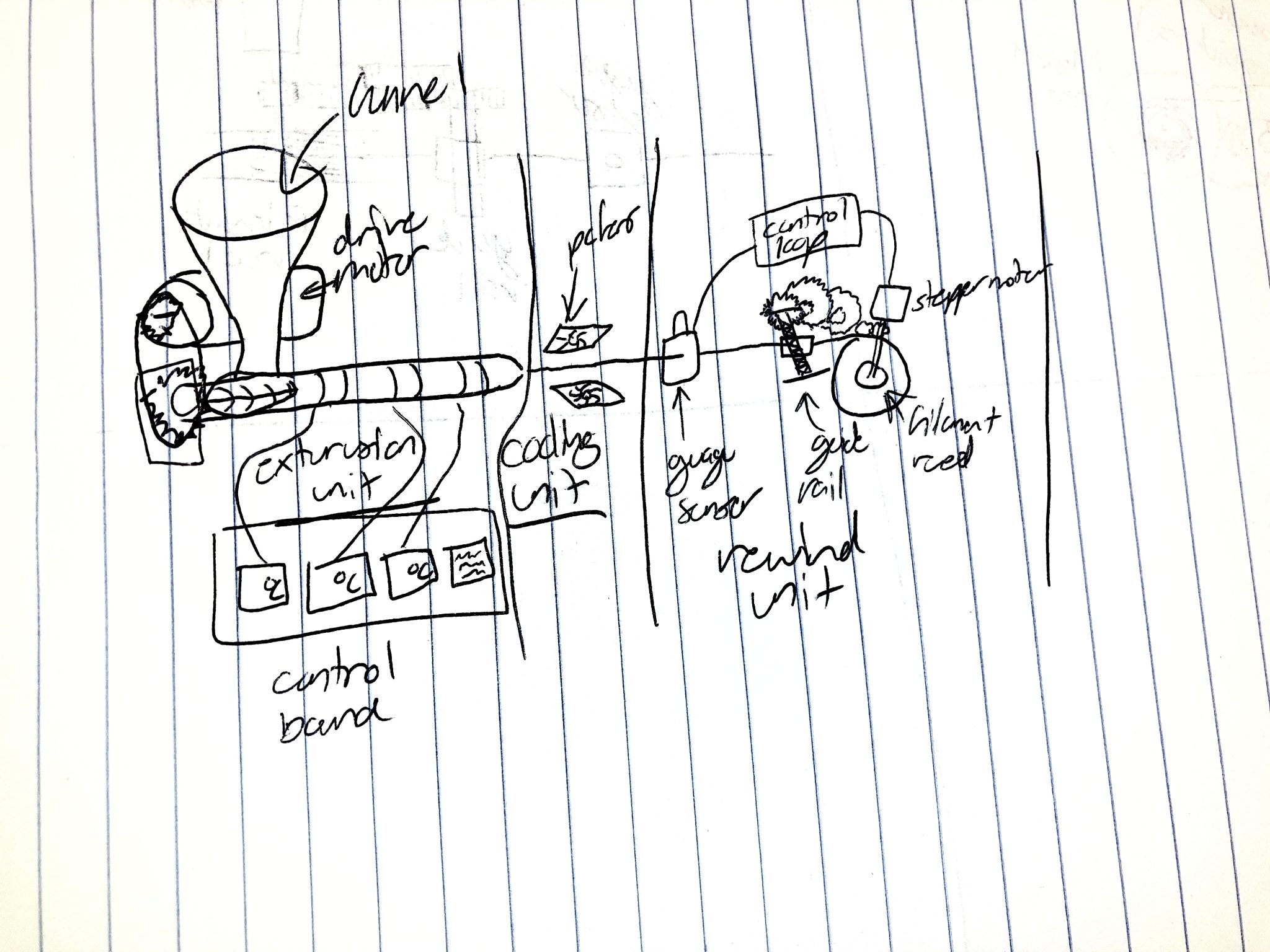
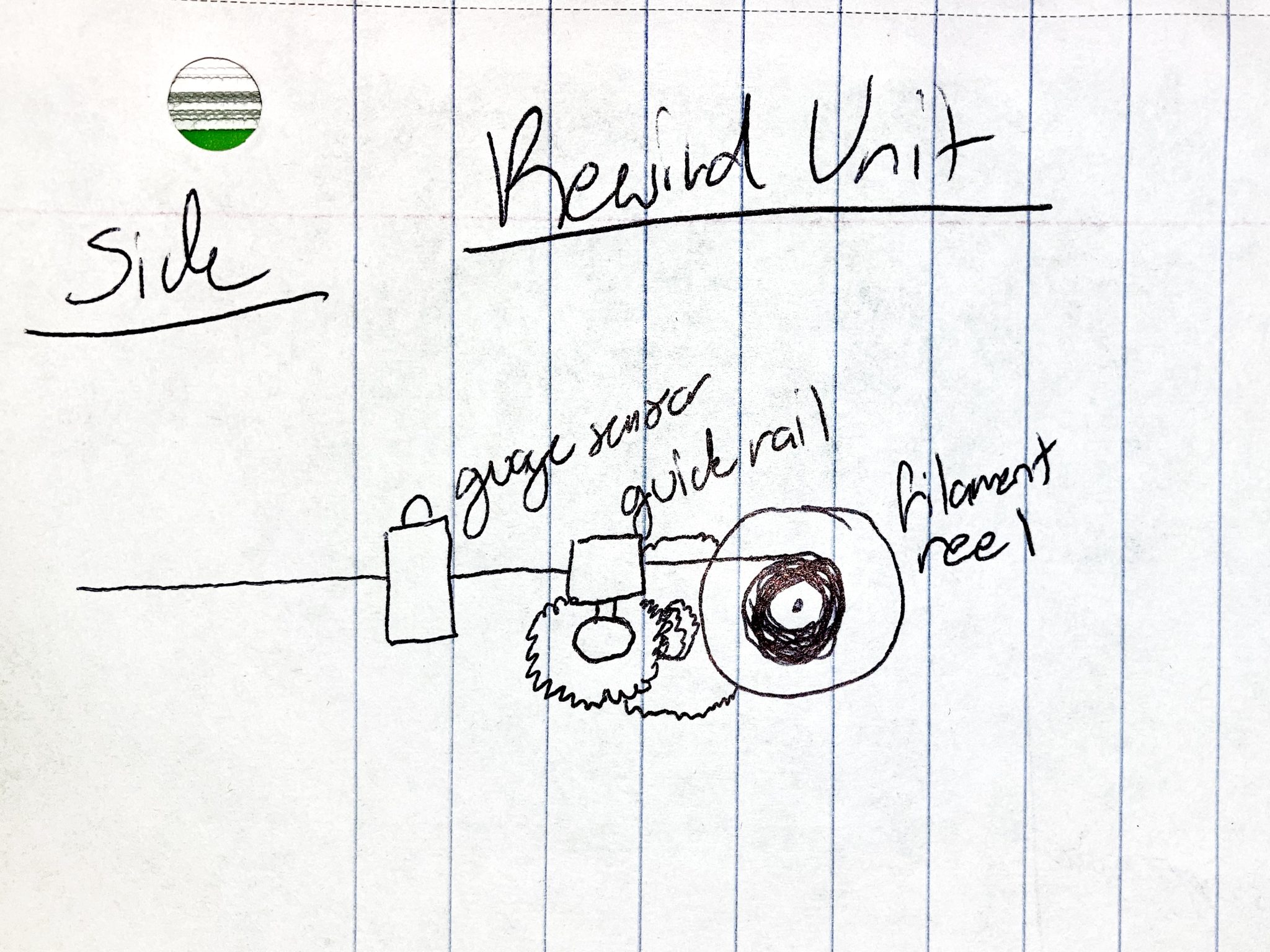
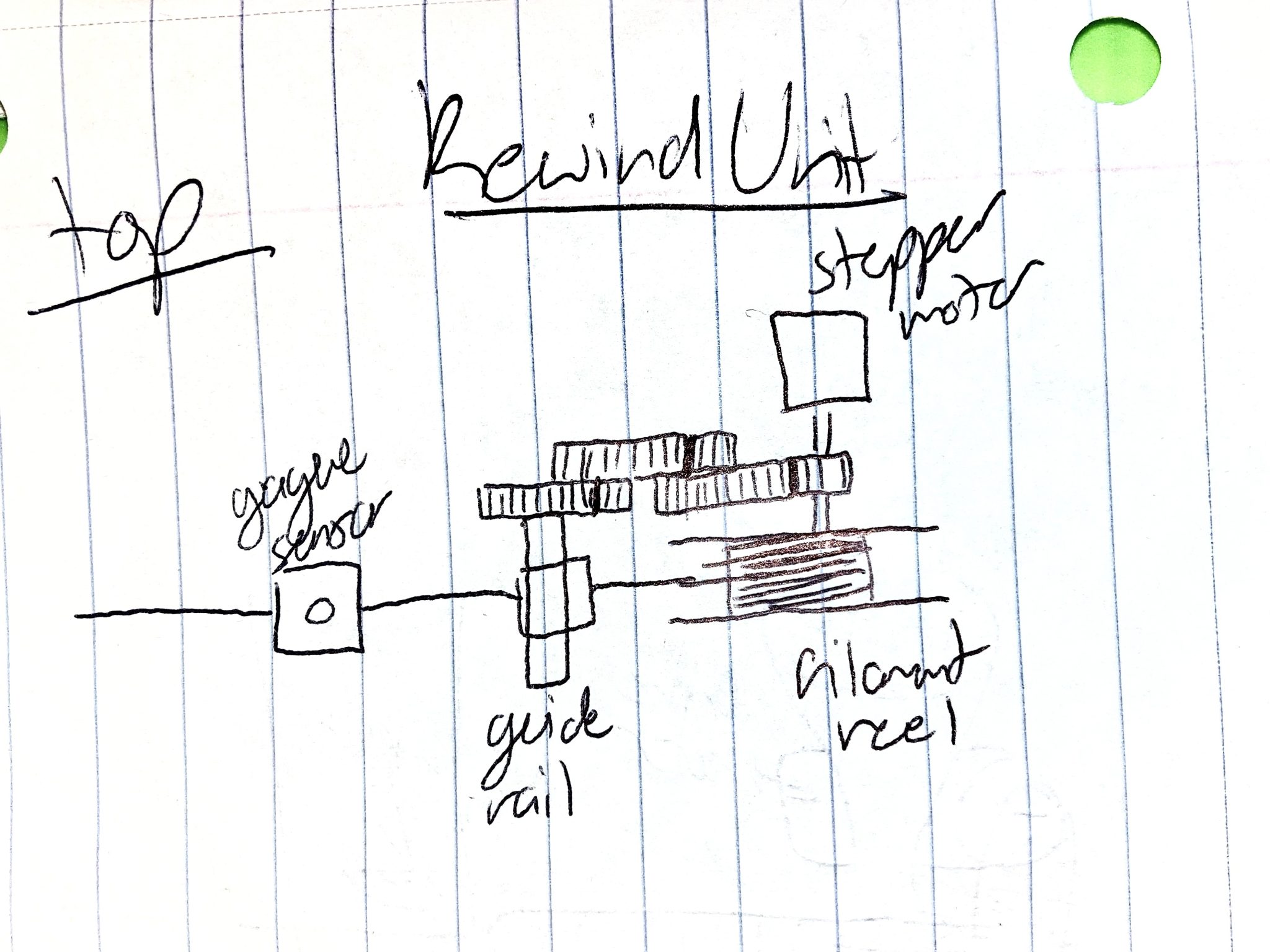
To Do List:
- Work with Jeff Gillis and team leads to put together the initial design for the rewind unit structure
- Put together a parts list for the basic elements of the rewind unit
- Stepper motor
- Gauge sensor
- Aluminum Extrusions
- 3d Printed parts
- Communicate with BREAD on working out the design of the control loop for the rewind unit
- Work with John Schneiderhan on getting the 3d printed parts we need (Material, Size, Integration, etc)
Concerns:
- N/A