2/16/2025 – Week 6 Update: This week we put in the digikey for the Raspberry Pi Hat components. Work has continued on the o-ring seal test and the new fish body. O-ring test should be printed by the end of this week.
1/19/2025 – Week 2 Update: This week I finished modelling the new caudal fin motion system, and ordered the parts we need for it. Next week I need to start designing the new body of the fish, as well as create a way to test using O-rings to create a waterproof seal instead of gaskets.
END OF FALL SEMESTER
9/20/2024: Over this past week I have worked on assembling the 3D printed gearbox, as well as the rest of the robot. I have run into a few issues with clearance for the motion system, which I will be working to correct this week. By the end of this week I hope to be able to demonstrate working motion of the tail of the fish.
9/13/2024: The first goal OSTR has this semester is to build the OpenFish robot defined in the research paper. Then, we will start designing our own which will include on-board power, wireless communication, buoyancy control, and on-board sensors.
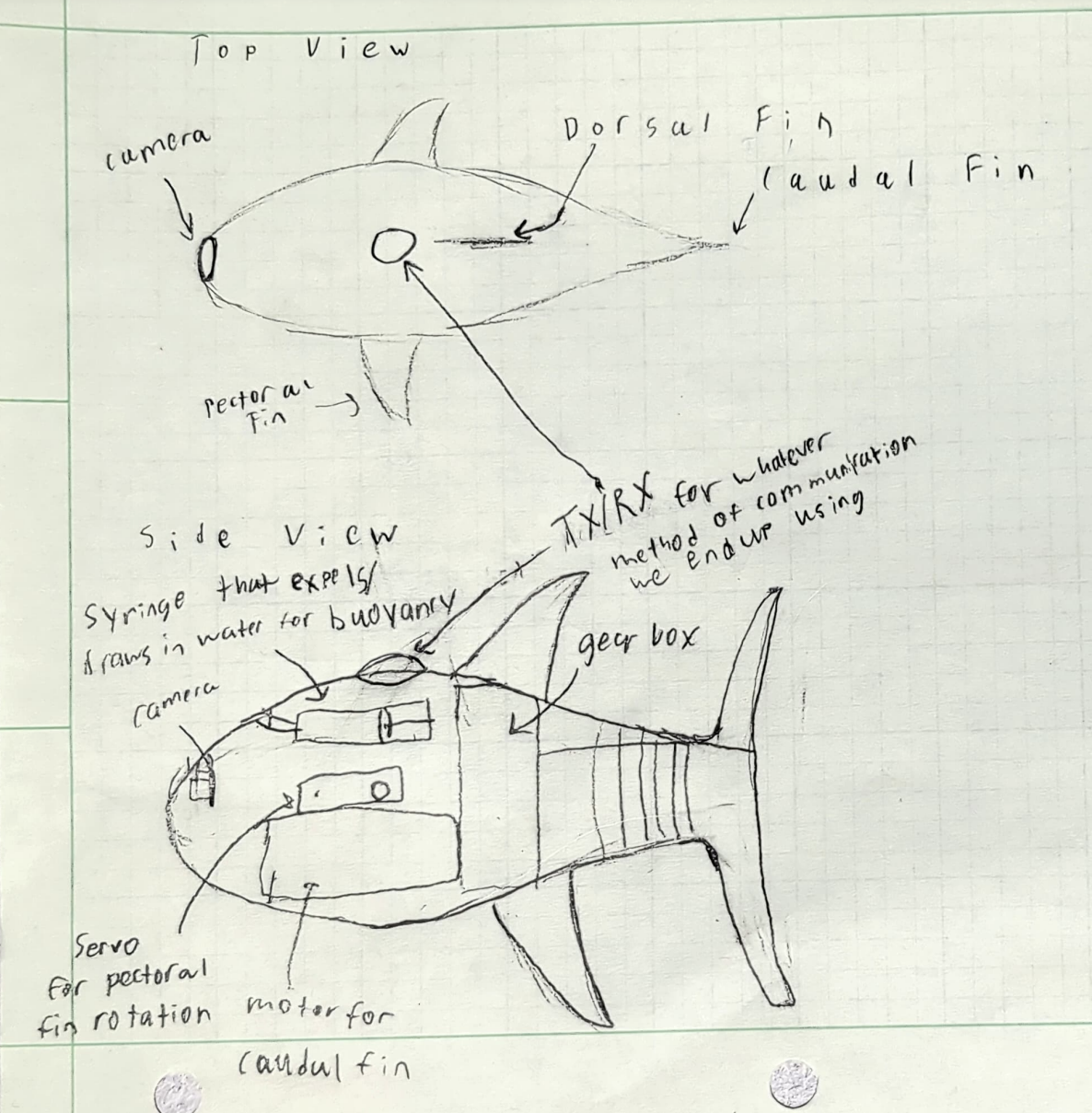
To do list for this week: Print right angle gearbox housing, print remaining three gears, assemble right angle gearbox, continue assembling the rest of the fish robot, purchase fishing line, and look into waterproofing 3d prints.
END OF SPRING SEMESTER
3/23/2024:This week we heard back from Len Switzer that our funding had been approved. The aluminum extrusion for most of the frame has been cut and assembled.
3/16/2024: Printed one of each bracket type to test fit with the frame, and printed the new mount for the motor that should better support it. Next week I will be working on updating the CAD for the hopper.
3/9/2024: Finished CAD of the new motor mount. The main change I made was moving the holes off of “tabs” and onto the main body of the mount.
3/2/2024: Spring Break
2/24/2024:Finished cad for 3 different bracket types, and started reworking the previous motor mount so it will work with the new frame design.
2/17/2024: Started designing new brackets for the 20 mm aluminum extrusion that can be 3D printed instead of having to buy some. This should allow us to make progress while we wait to get funding.
2/10/2024: Started a basic CAD model of the new aluminum extrusion frame.
2/3/2024: This week we met with Len Switzer to discuss funding, and are working on filling out the proposal. I have started making the design in FreeCAD, and we have selected the extrusion barrel and screw and should be ordering it early this week. My biggest concern for next week will be figuring out the dimensions for the extrusion barrel as I continue to work on the CAD.
1/27/2024: Our goal for the next couple semesters will be redesigning recyclebot from the ground up. This semester we will focus on the heating and extruding module. For this week we are focusing on meeting with Len Switzer to discuss EMI funding, finalizing a purchasing list and a budget for the semester, and starting to design the module in FreeCAD. My biggest concern for the next week is how long it will take for us to receive funding, as the extrusion screw and barrel we are planning on ordering can have a long shipping time.
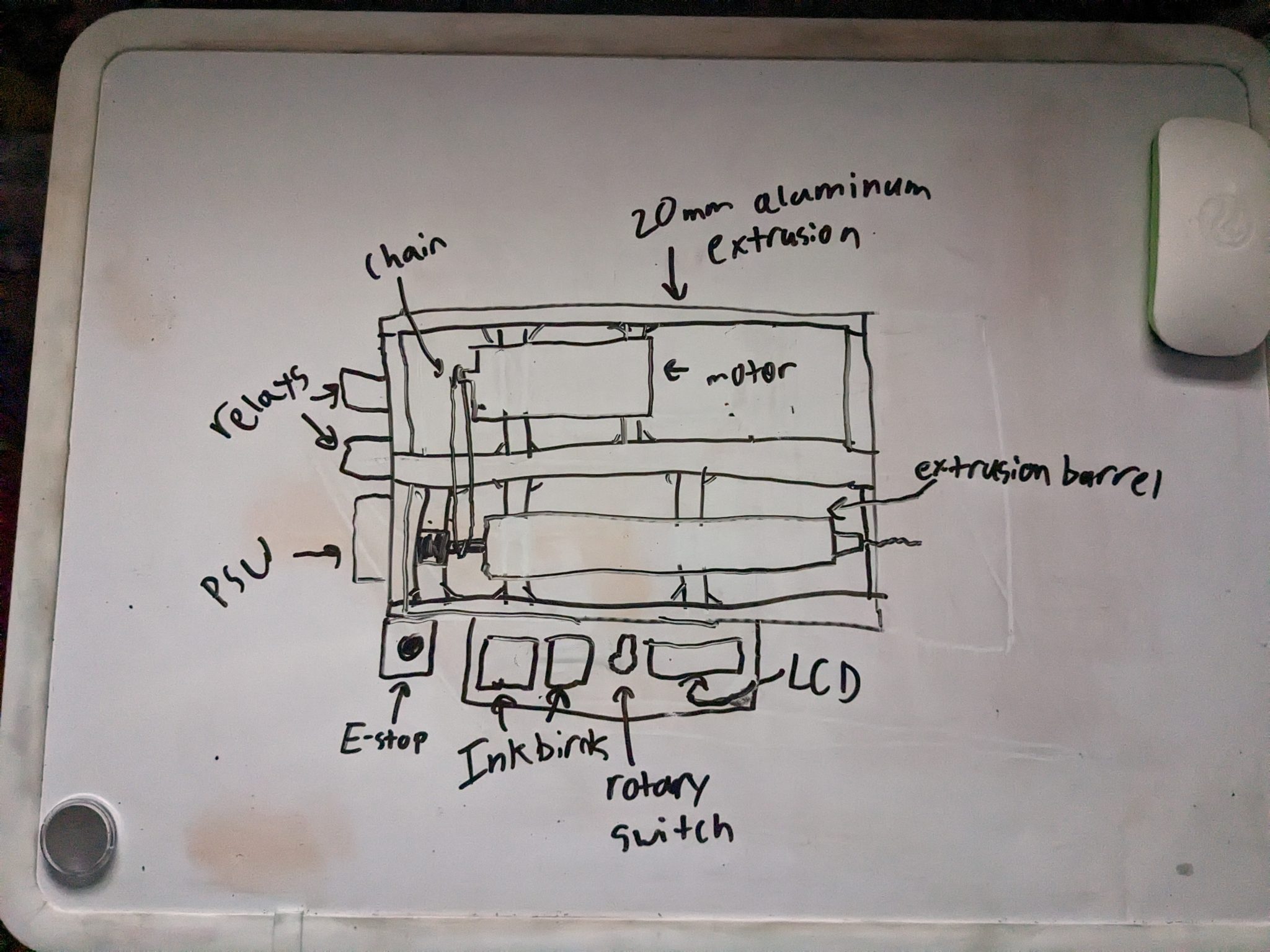
11/4/2023: After taking apart the hopper we discovered what caused last weeks failure. Overtime the pressure in the extrusion pipe deformed the hopper, forming a hole that partially melted pellets could flow through. At this point the entirety of Recyclebot has been disassembled and we are working on ways to improve our design to keep this from happening.
10/28/2023: While running the purge cycle this week, we ran into an issue that put too much force on the legs of the hopper. There was also black molten plastic leaking out of the back of the extrusion pipe. We are looking at ways to reinforce the hopper legs and to figure out why the plastic was leaking out.
10/7/2023: Working on airtight hopper redesign, first prototype will be printed later this week. The new design will include three pieces, a base, main tube, and a lid. All three pieces should be able to form an airtight seal with each other to prevent the filament pellets from absorbing moisture from the air.
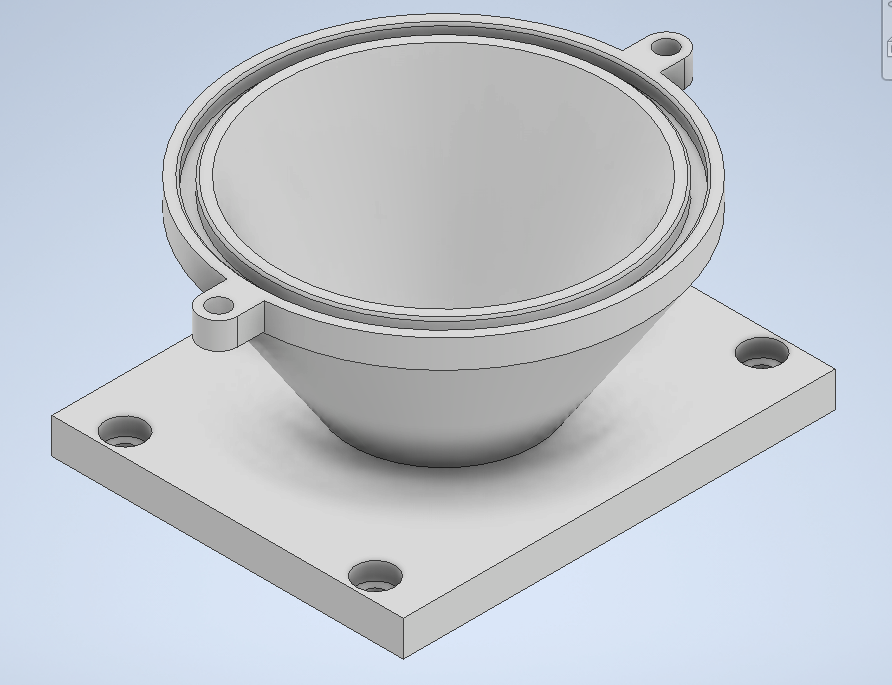
9/30/2023: Printed motor mount and motor adapter and attached them to recyclebot. Started designing the new hopper.
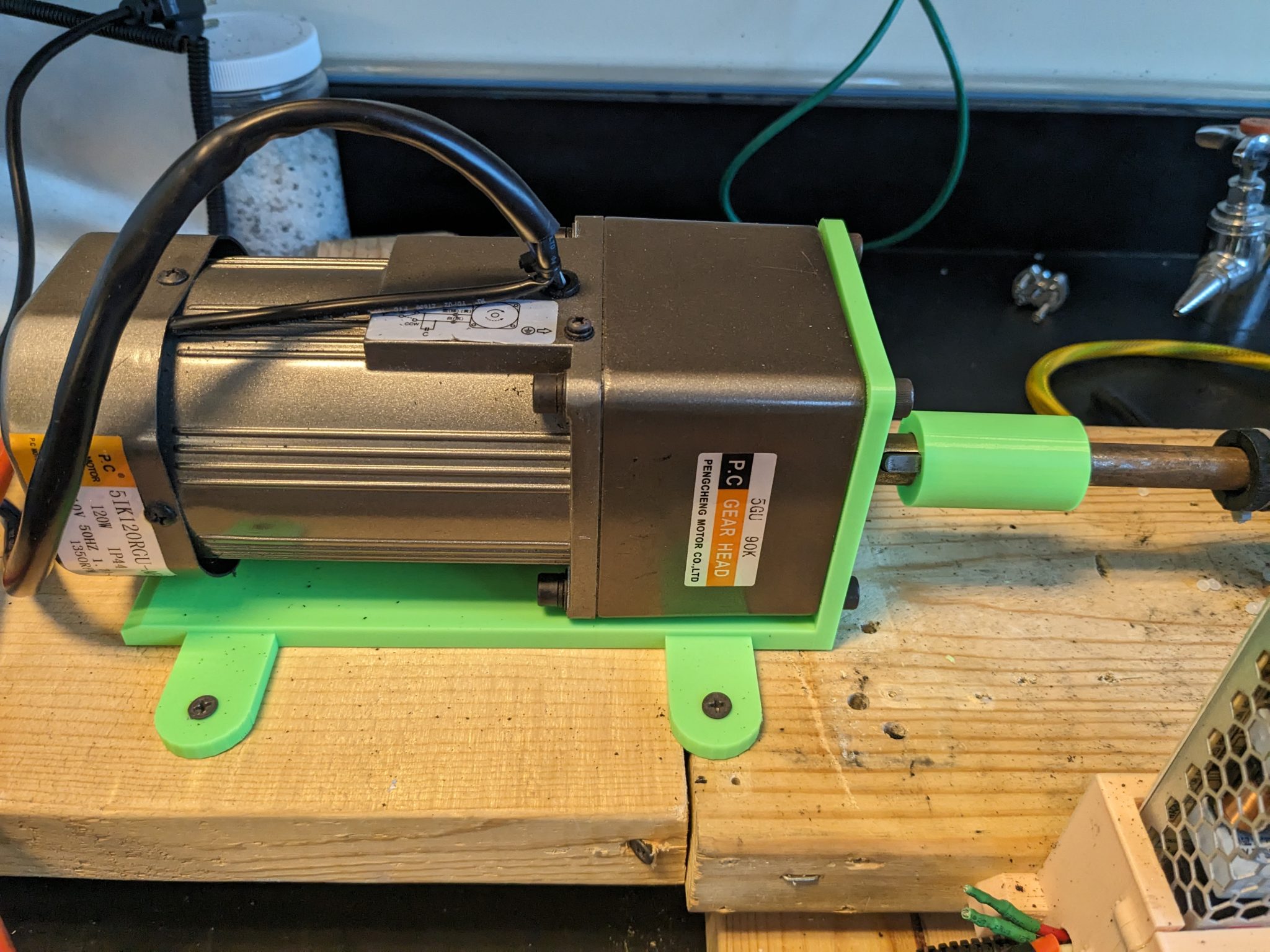
9/23/2023: Selected a 51k120rgu-af to use as a gearmotor to drive the extrusion screw. Designed a new mount to hold it. Next steps will be printing the motor mount and wiring the motor into the rest of the system, and starting work on the redesign of the hopper.
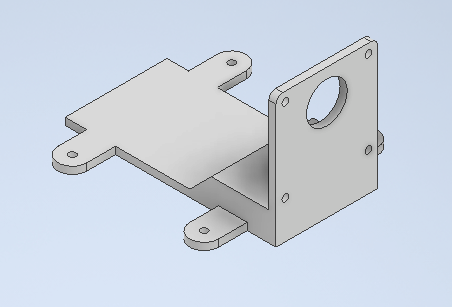